Asset management and facility management are two different, yet interconnected strategies within a facility. Asset management focuses on tracking, maintaining, and optimising physical assets like machinery and equipment to improve performance and lifespan.
Facility management, on the other hand, oversees the people, processes, and infrastructure that keep buildings, utilities, and work environments running smoothly and safely.
Failing to differentiate between the two can lead to unexpected equipment failures, higher maintenance costs, and slow operations. For example, a factory might prioritise equipment maintenance but overlook HVAC systems, causing overheating and production delays.
This article explains asset management vs. facility management, highlighting their key differences, similarities, and how they work together to improve operations in a facility.
What is Asset Management?
Asset management (AM) is about tracking and maintaining assets like machines, equipment, and infrastructure to reduce costs, minimise breakdowns, and extend the life of equipment.
Fundamentals of Asset Management
The fundamentals of asset management include:
- Tracking and monitoring assets to improve operations
- Preventive and predictive maintenance to reduce downtime
- Risk management and lifecycle optimisation to extend asset lifespan
- Cost control to scale operations sustainably
3 Types of Asset Management
Here are three types of asset management:
- Physical Asset Management: Focuses on managing tangible assets like machinery, equipment, and infrastructure to improve performance and lifespan.
- IT Asset Management (ITAM): This tracks and optimises hardware, software, and digital assets to improve cybersecurity and cost efficiency.
- Fixed Asset Management: This deals with long-term assets like buildings, land, and heavy machinery to meet compliance with depreciation and financial reporting.
Benefits of Asset Management
Here are some benefits of asset management:
Reduces Downtime and Failures
AM uses scheduled maintenance, performance tracking, and automated monitoring to reduce machine downtime and prevent unexpected failures. Tools like CMMS, IoT (Internet of Things) sensors, and root cause analysis help teams track, detect, and fix machinery issues before they break down.
Extends Asset Lifespan
Asset management extends lifespan by preventing overuse, scheduling timely repairs, and improving equipment performance.
Lowers Maintenance Costs
Research shows that predictive maintenance strategies can extend asset lifespan by 20-40%. Asset management lowers maintenance costs by shifting from reactive to preventive/predictive maintenance planning. This helps you reduce both direct and hidden costs.
Improves Productivity
Asset management involves real-time monitoring using automated tracking systems like IoT sensors. It uses existing data to analyse your asset’s performance, quickly respond to potential issues, schedule maintenance, and assign repair jobs proactively.
Meets Safety and Compliance Standards
Asset management makes sure your equipment is maintained, inspected, and operated within regulatory guidelines. Through routine maintenance and real-time monitoring, it lets you identify safety risks before they cause accidents.
Supports Better Decision-Making
Asset management supports better decision-making by providing real-time data, historical performance insights, and predictive analytics. This allows you to prioritise maintenance budgets, optimise asset usage, and plan for spare part replacements before failures occur.
Real-time Visibility
With clear visibility into asset health and costs, asset management helps you allocate resources more effectively, reduce unnecessary expenses, and improve long-term capital planning.
What is Facility Management?
Facility management oversees people, infrastructure, and processes to maintain buildings, utilities, and safety systems. It improves operations, supports asset performance, and ensures a functional, safe workspace.
Its role includes managing maintenance, optimising resources, and upholding safety standards while preventing infrastructure-related disruptions.
Fundamentals of Facility Management
The fundamentals of facility management include:
- Asset maintenance and management to prevent equipment failures
- Space and infrastructure management to optimise facility layout for better workflow
- Energy and sustainability to reduce power, water usage, and costs
- Workplace safety and compliance to meet regulatory standards
- Technology integration to track assets, automate maintenance, and improve operational workflow.
Types of Facility Management
Facility management has two main categories:
Hard Facility Management (Hard FM)
This category focuses on the physical infrastructure of a facility, such as HVAC systems, electrical wiring, plumbing, fire safety, and security systems. These elements must be maintained to prevent workplace hazards and operational downtime.
Soft Facility Management (Soft FM)
This category focuses on people-centric services like workspace management, cleaning, and compliance with environmental regulations. This ensures a safe, organised, and efficient working environment.
Benefits of Facility Management
Here are some benefits of facility management:
Optimises Space Usage
Facility management involves careful layout planning to optimise your facility’s space. It helps you reduce wasted space by accurately placing your assets to match your workflows and shorten employees’ travel time.
Improves Budgeting
This involves calculating and planning facility-related costs, such as maintenance, renovations, and spare part upgrades.
Reduces Energy Costs
Facility management lowers energy costs by automating controls, maintaining energy-efficient equipment, and monitoring resource usage.
It also promotes sustainability by incorporating renewable energy sources like solar panels and waste-reduction systems to cut costs and reduce environmental impact.
Promotes Employee Safety
Facility management maintains a hazard-free work environment, enforcing compliance with safety regulations and implementing emergency response plans. It involves regular inspections of buildings, fire suppression systems, and ventilation to prevent workplace accidents.
Asset Management vs Facility Management: Exploring the Main Differences
Asset management and facility management may seem similar, but they have different objectives, scopes, and operational impacts.
Here’s how they differ:
1. Primary Focus: Assets vs. Infrastructure
Asset management focuses on tracking, maintaining, and improving individual assets (e.g., machines, IT systems, production tools). Facility management makes sure buildings, utilities, and overall workspaces are well-maintained.
2. Goals: Performance vs. Functionality
Asset management focuses on keeping assets operational, maximising their lifespan, and optimising performance. Facility management maintains overall workplace functionality by managing employee safety, space usage, and regulatory compliance.
3. Scope: Equipment vs. Work Environment
Asset Management focuses on assets that need regular monitoring and repairs. Compared to AM, facility management covers everything that makes a workspace functional, from lighting and ventilation to security and waste management.
4. Impact on Business Operations
Poor asset management leads to equipment breakdowns, higher maintenance costs, and production delays. Poor facility management results in safety risks, excessive energy use, and workplace discomfort.
Quick Comparison: Asset Management vs. Facility Management
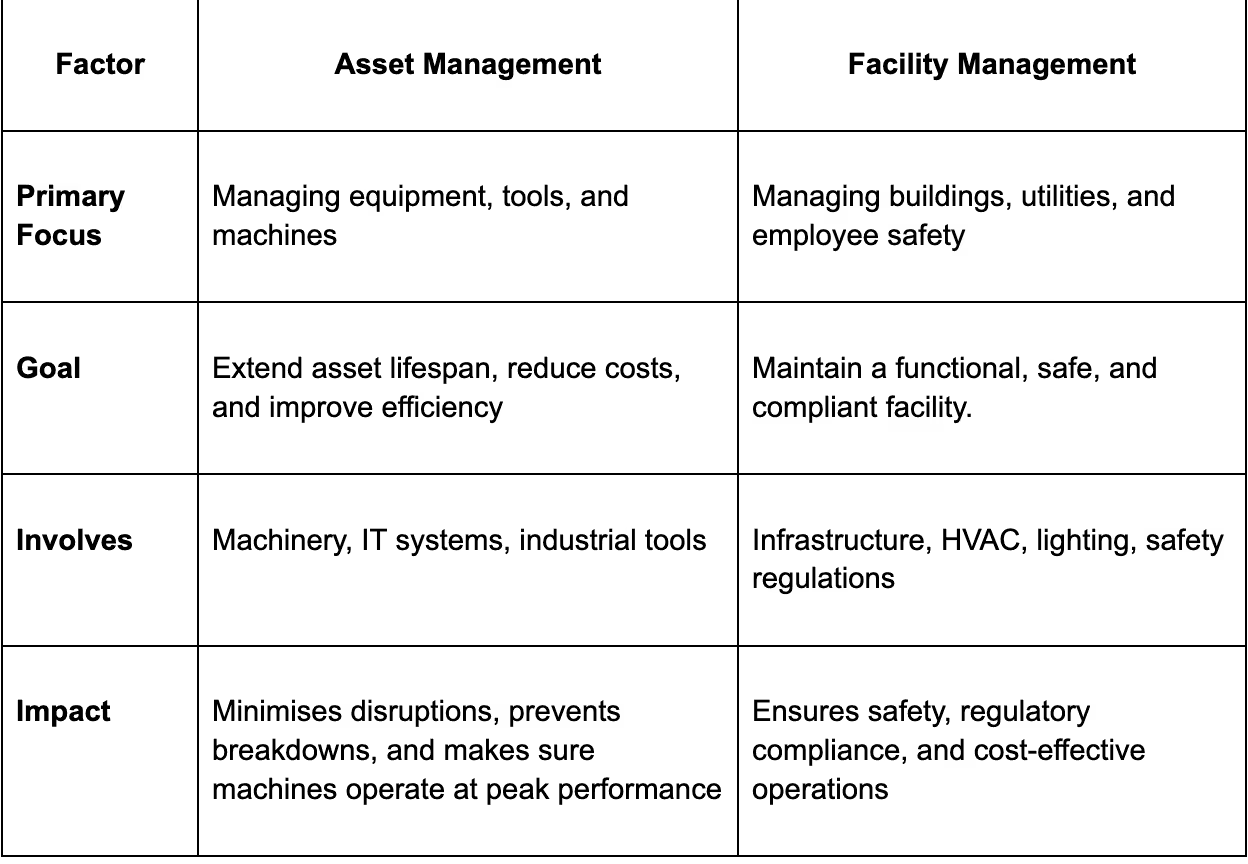
What’s Common Between Asset and Facility Management
Here are some commonalities between asset and facility management:
- Optimising Operations: Both aim to keep your facility running smoothly by maintaining critical assets, whether machinery or infrastructure.
- Preventive Maintenance: Both use scheduled maintenance to prevent breakdowns, extend asset lifespan, and reduce costly disruptions.
- Cost Management: Both help control expenses by reducing unplanned repairs, optimising resource use, and improving long-term operations.
- Technology Integration: Both rely on automated tools like asset management software, CMMS (computerised maintenance management system), IoT sensors, and data analytics for tracking, monitoring, and decision-making.
- Workplace Safety & Compliance: Both contribute to a safer work environment by minimising hazards, meeting regulatory standards, and reducing risks.
How Do Asset and Facility Management Work Together
Asset and facility management work together to optimise your operations and meet specific business goals.
Here are some ways they interact:
- Seamless Operations: Facility management maintains the facility environment (power, ventilation, workspace), while asset management keeps the machinery running for smooth workflows.
- Preventive Maintenance Synergy: Facility management schedules HVAC, lighting, and structural maintenance, while asset management keeps machines serviced. Together, they prevent costly disruptions.
- Optimised Resource Allocation: Both coordinate budgets to avoid overspending. For example, facility management reduces energy and space costs, while asset management prevents unnecessary repairs and replacements.
- Workplace Safety & Compliance: Facility management makes sure buildings and utilities meet safety codes while asset management maintains safe, functional equipment to reduce workplace hazards.
- Technology & Data Sharing: Both use CMMS, IoT sensors, and predictive analytics to track asset health, energy use, and maintenance needs, allowing better decision-making.
For example, asset managers oversee machinery performance and schedule preventive maintenance to prevent breakdowns. Facility managers coordinate these maintenance activities within the facility's operations to reduce disruption during production schedules.
How You Can Combine Asset and Facility Management
Here’s how you can implement asset and facility management to improve your facility operations:
1. Evaluate Your Assets and Create a Plan
Assess all machinery, infrastructure, and facility systems to identify maintenance priorities, repair needs, and potential risks that could disrupt operations.
After evaluation, develop a facility asset management plan. This plan should outline your asset inventory, maintenance schedules, budget allocation, and risk management strategies.
2. Implement an Automated Software
Use automated software like CMMS to track asset conditions, schedule repairs, and manage facility maintenance in one system. With real-time monitoring and automated alerts, automated systems can reduce manual errors, improve tracking accuracy, and help predict failures before they happen.
3. Assign Clear Roles and Responsibilities
Create a team with dedicated asset managers and facility managers to improve your facility workflows and prevent overlap in maintenance tasks. Clearly assigning roles avoids maintenance delays, prevents miscommunication, and establishes accountability across different teams.
Some of the important roles are:
- Asset managers focus on tracking and optimising machinery & equipment.
- Facility managers handle infrastructure, utilities, and safety regulations.
- Maintenance teams execute repairs, servicing, and preventive maintenance schedules.
4. Integrate Maintenance Schedules
Use automated systems to synchronise equipment maintenance with facility upkeep. For example, CMMS can help technicians view, track, and update asset details using their mobile devices to create daily maintenance checklists.
This coordinated approach prevents disruptions, maximises productivity, and extends the lifespan of both your assets and infrastructure.
Book a demo with Makula to see how our software helps factories and OEMs manage assets, schedule maintenance, and reduce downtime. With real-time tracking and automated workflows, you can keep equipment running smoothly and avoid costly failures.
FAQs
What is the difference between asset management and maintenance management?
Asset management is managing your overall asset performance over its lifecycle. Maintenance management specifically focuses on repairing, servicing, and preventing failures to keep assets operational.
What are the 4 pillars of facility management (FM)?
The four pillars of facility management are people, processes, technology, and infrastructure. Each pillar involves strategies to optimise your operations while maintaining safety and cost-effectiveness.