Manufacturers lose millions to unplanned downtime, with an hour costing up to $260,000 and 15 hours lost per week on average. Yet, 39% of facilities still rely on paper-based documentation, making it difficult for workers to find past repairs or troubleshooting steps when needed.
Conversational Artificial Intelligence (AI) in modern manufacturing solves this by capturing and retrieving machine-specific data, past service records, or step-by-step repair instructions through context-based answers.
This article explores how conversational AI is transforming manufacturing, its benefits, key challenges, and use cases.
What is Conversational AI?
Conversational AI uses natural language processing (NLP), machine learning, and knowledge retrieval to recognize, interpret, process, and simulate human-like conversations through voice or text.
For example, a technician on the shop floor notices Press Machine #7 is overheating. They can ask AI, "When was the last coolant system check on Press Machine #7?"
Within seconds, AI pulls up the latest maintenance records, temperature trends, and repair history, showing that the coolant system was serviced two weeks ago but flagged for follow-up.
The technician will instantly know what to inspect next and ensure a quick fix.
These intelligent systems unify and organize data, such as:
- Machine performance logs are instantly accessible.
- Manuals and SOPs are digitized for quick retrieval.
- Schedule maintenance for regular servicing and checks.
- Technicians and operators can log issues hands-free.
- Managers get real-time insights to reduce machine downtime.
Conversational AI in manufacturing takes three key forms:
- Question-answering (QA) agents: Instantly pull answers from technical manuals, maintenance logs, and production data to speed up machine troubleshooting.
- Task-oriented dialogue systems: Assist with scheduling, quality control, and predictive maintenance, reducing machine downtime and delays.
- Social chatbots: Help onboard new employees, provide hands-free assistance, and improve team communication in factory settings.
Why is Conversational AI Important in Manufacturing?
In manufacturing, data storage and accessibility are a big challenge. Manufacturers need to manage massive amounts of data, from machine performance logs, maintenance records, and production workflows to supplier data, inventory levels, and customer requests.
When done manually, retrieving relevant information is time-consuming, prone to errors, and slows down decision-making.
Conversational AI centralizes this scattered data and provides real-time, context-aware responses to help manufacturers, technicians, and operators make faster, smarter decisions.
AI models leverage deep learning to analyze patterns, learn from past interactions, and refine responses over time.
Hierarchy of AI in Conversational AI Systems
- Artificial Intelligence (AI): The broad field of technology that enables machines to perform tasks requiring human-like intelligence, such as learning, reasoning, and automation.
- Natural Language Processing (NLP): A subset of AI that allows computers to understand, interpret, and generate human language, making AI-driven communication possible.
- Conversational AI: A specialized application of AI and NLP that enables machines to engage in human-like interactions via text or voice, understanding context, tone, and user intent.
- Applications of Conversational AI Examples:
- AI Copilot: Assists in real-time decision-making, troubleshooting, and knowledge retrieval for technicians, service teams, and professionals.
- AI Notetaker: Transcribes, summarizes, and organizes conversations, service notes, and meetings to improve documentation and workflows.
Challenges Manufacturers Face and How Conversational AI Solves Them
Here are some challenges manufacturers face and how conversational AI helps solve them:
Skilled Labor Shortages
According to the National Association of Manufacturers, nearly 77% of manufacturing managers cite a skilled labor shortage as their biggest challenge, with 2.1 million jobs expected to remain unfilled due to the growing skills gap.
OEMs need skilled labor to identify and repair machine parts accurately, which only comes from years of experience or industry-specific expertise.
How conversational AI can overcome this:
- Conversational AI assistants collect maintenance logs and expert knowledge from existing workers accurately.
- It provides real-time guidance from the existing knowledge base, documentation, and history logs for new workers.
- AI copilots make knowledge retrieval easy, saving employees from straining themselves by searching through manuals and documents.
Equipment Downtime
Manufacturers face around 800 hours of equipment downtime annually, causing substantial production losses and costs. Most factories rely on reactive maintenance (only repair when the machine breaks) due to a lack of real-time visibility, stranded data, manual data collection, and skill gaps in machine troubleshooting.
Here’s how conversational AI helps:
- You can train the model by uploading external and internal machine documentation for real-time equipment insights, reducing machine downtime and enabling proactive maintenance.
- Conversational AI unifies maintenance histories, performance metrics, and predictive analytics for instant access.
- It acts as a virtual assistant to guide less experienced technicians through complex troubleshooting processes with step-by-step instructions.
Siloed Knowledge
Most manufacturing companies use Excel sheets and paper-based systems to store critical information or rely on experienced workers’ knowledge. When these workers retire or leave, their expertise goes with them because their knowledge isn’t documented. New technicians are left to figure things out the hard way.
How conversational AI overcomes this:
- AI provides a single source of truth by gathering large machine databases, documentation, manuals, and maintenance logs.
- Tools like AI notetakers allow existing employees to quickly input or record critical information, maintenance reports, and processes. These integrate with the existing machine knowledge for quick and easy retrieval through tools like AI copilots, saving new employees’ time.
- AI assistants leverage advanced machine learning models to perform predictive analysis, minimizing downtime.
For example, Makula’s AI Notetaker allows workers to record or type notes on daily operations, which are transcribed and stored in a centralized system. The AI Copilot retrieves this data to provide instant, context-based answers.
Expert Input
Experienced technicians, operators, and managers often spend valuable time manually logging maintenance details and updating records after servicing a machine.
This extra workload slows them down and increases the risk of missing critical details. Over time, this manual process leads to delays, errors, and inefficiencies in equipment maintenance and troubleshooting.
How conversational AI helps:
- AI Notetaker can record voice notes, and text, saving time for technicians.
- AI can simplify complex documentation by summarizing diagnostics, repairs, and key observations.
Top 3 Use Cases of Conversational AI in Manufacturing
Here are some use cases of conversational AI in manufacturing:
1. Factory Floor Assistance & Equipment Maintenance
Conversational AI like AI copilots give technicians instant access to critical machine data while reducing reliance on manual searches. Manufacturers can train AI models on machine manuals, maintenance logs, sensor data, and service histories. This allows technicians to quickly retrieve diagnostics and maintenance recommendations.
For example, if a machine shows unusual vibration levels, conversational AI can instantly provide technicians with recommended troubleshooting steps and preventive maintenance actions.
2. Customer Support & Self-Service
AI-powered co-pilots help OEMs (original equipment manufacturers) provide real-time troubleshooting and support for their clients. Beyond documentation, conversational AI improves service management and response times by assisting with real-time technician dispatching and customer support to end-customers.
By integrating AI with detailed machine data and technical manuals, OEMs can provide branded self-service AI assistants to diagnose issues, guide users through fixes, and recommend maintenance steps. This reduces workflow delays and reliance on expert labor.
3. Employee Support & Training
In manual settings, field service workers need to return to their facility before documenting their notes, which results in errors or forgotten information. This delay-based documentation process often leads to decreased accuracy and completeness in reporting.
With AI Notetakers, technicians can record maintenance processes hands-free in real time, ensuring no detail is lost. The AI automatically transcribes and categorizes notes by machine type, issue, and repair method, creating a searchable database of past fixes.
New employees can use the AI Copilot to retrieve step-by-step repair instructions based on past maintenance logs and supplier guidelines.
For example, if a machine malfunctions, the AI Copilot can cross-reference similar breakdowns, suggest the most effective fixes, and provide guided repair steps.
Makula’s Industrial AI Products
AI Copilot
Makula’s AI Copilot is an advanced conversational AI assistant for original equipment manufacturers and factories to access machine-specific insights quickly. Instead of searching through manuals or documentation, users can ask questions in natural language, and AI Copilot retrieves the most relevant answers from indexed machine data.
The following are the key features of Makula’s AI Copilot:
Instant Retrieval of Machine Data
You can view and upload machine manuals, past repairs, and troubleshooting guides on a unified dashboard. The AI Copilot has an easy interface with beginner-friendly navigation to access relevant documentation quickly.
OEMs can train the AI Copilot by uploading their proprietary databases here and providing a branded self-service to their customers.
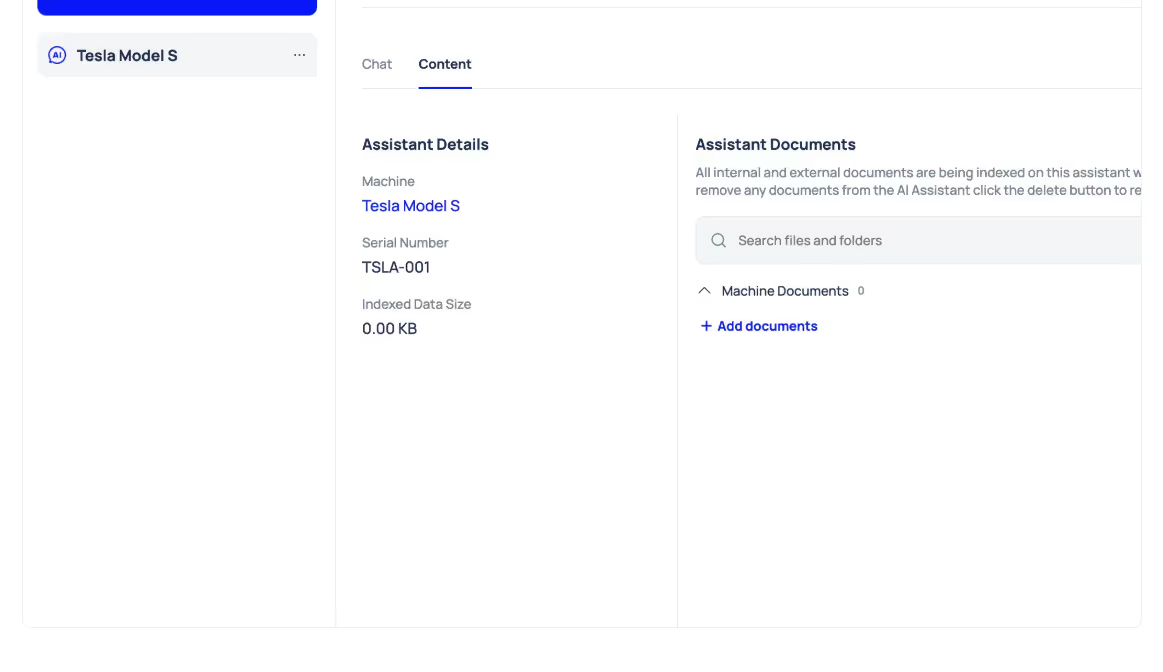
Context-Aware Troubleshooting
When you prompt AI Copilot with a complex query on specific machine data, the AI will search the knowledge base to answer your question in an easy-to-read, conversational format.
Our AI Copilot retrieves accurate machine specs, past maintenance logs, and troubleshooting guides along with document links for reference.
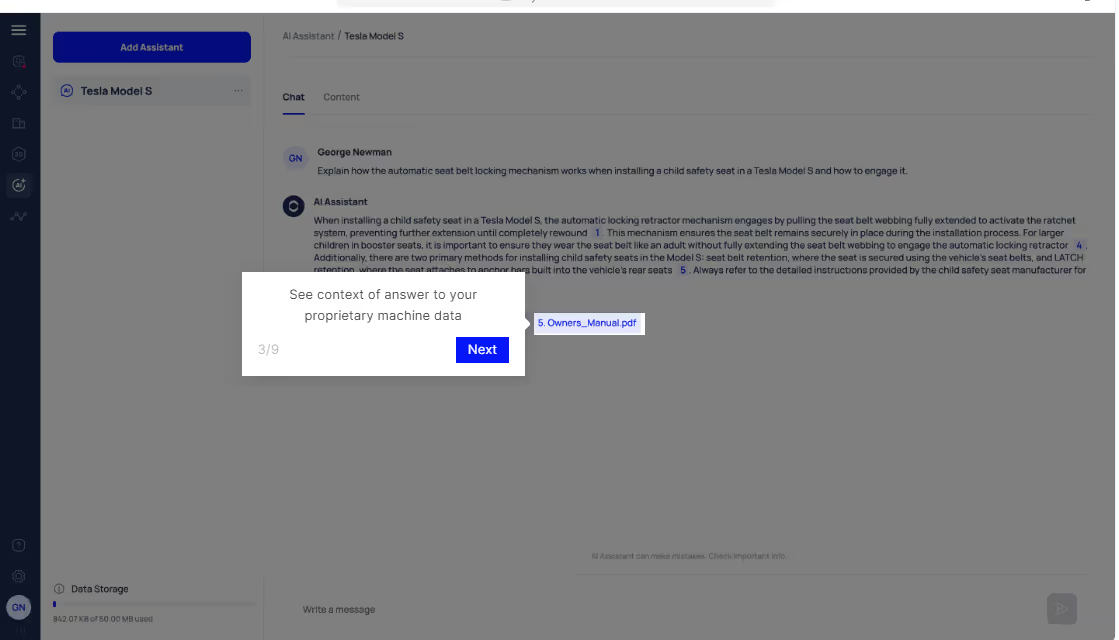
Multilingual Support
Makula’s AI Copilot provides multilingual support for your diverse workforce. You can ask questions in any language and receive responses without communication barriers. This helps your employees understand instructions in the language they’re comfortable with.
Makula’s AI Notetaker
Makula’s AI Notetaker automates the process of logging maintenance tasks. It records, organizes, and summarizes maintenance notes as technicians work, ensuring every step is captured accurately.
Its key features include:
Real-Time Voice Capture
You can record notes via voice, and AI Notetaker will instantly transcribe and generate structured maintenance logs with key action points.
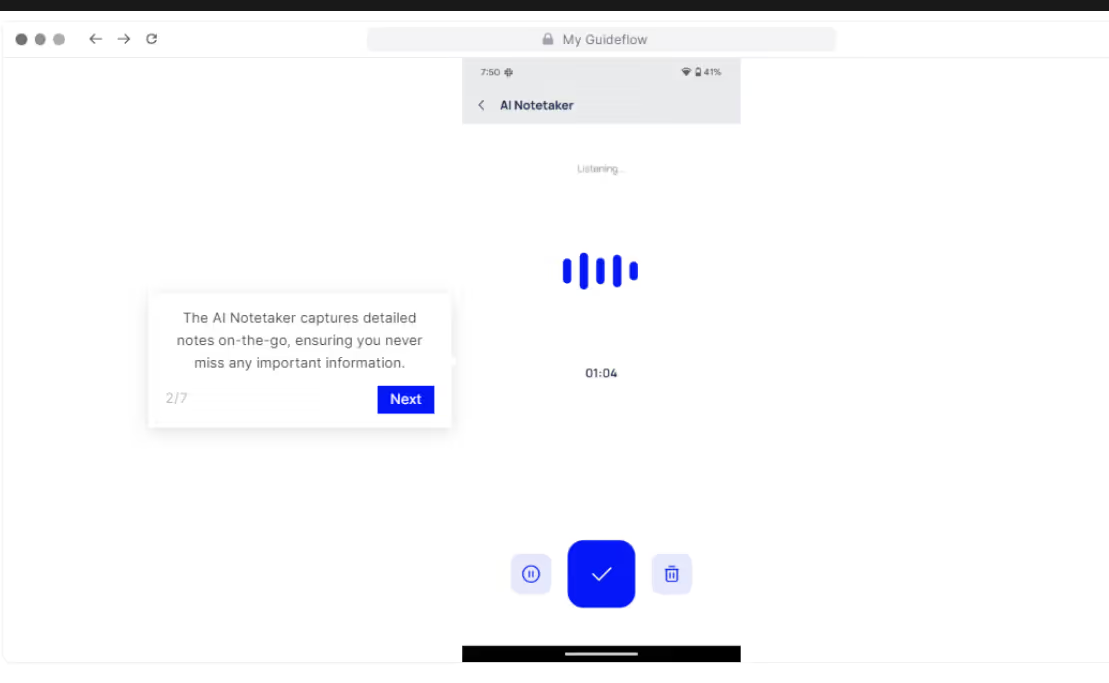
Centralized Recordkeeping
You can save and publish notes for multiple machines with unique spec details. The AI Notetaker automatically uploads these notes to a centralized database that the AI Copilot can access during relevant queries.
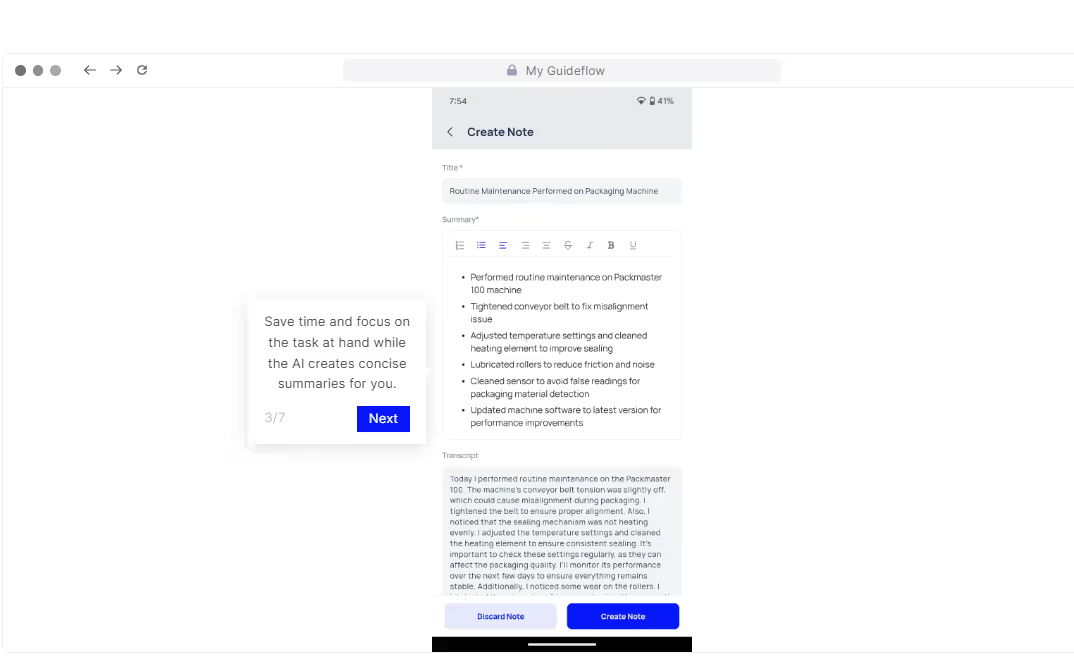
Historical Reference & Searchability
The AI Notetaker links maintenance logs to each machine’s history for quick access. This allows new employees to reference recorded notes for relevant information without requiring a senior supervisor.
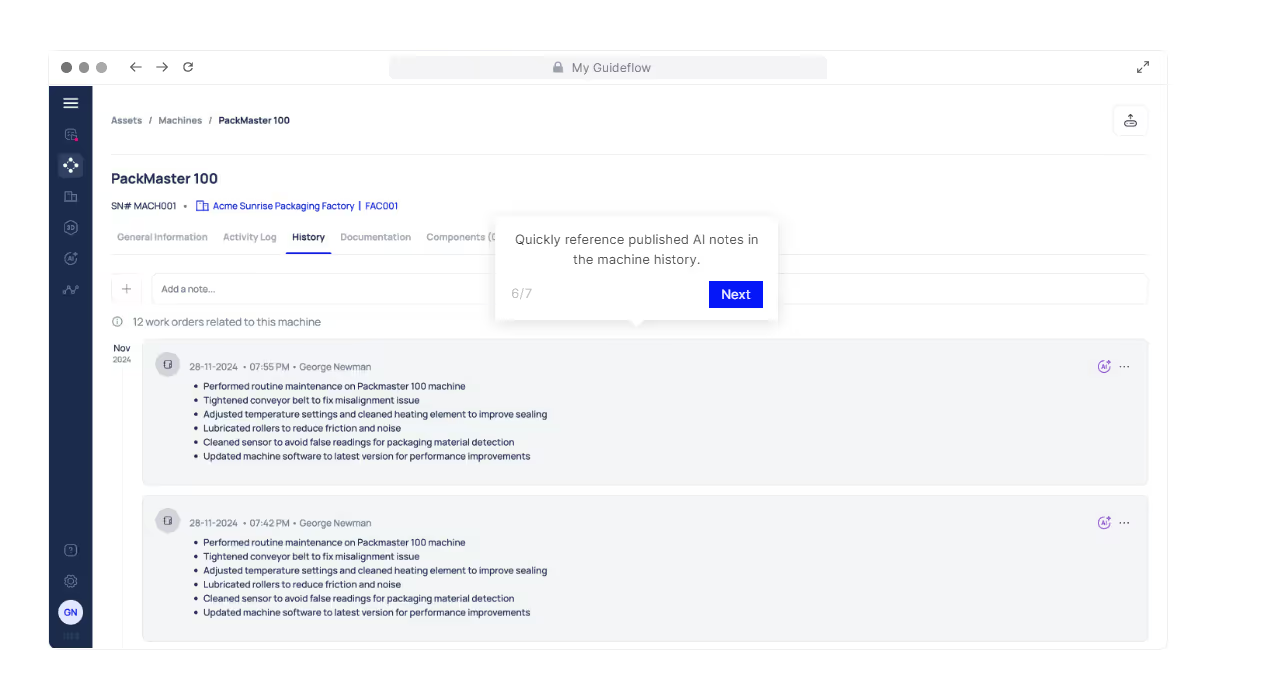
The Future of Conversational AI in Manufacturing
Conversational AI is still a growing implementation that requires future developments and deep learning inputs to fully augment workers’ experience. Studies show that 52% of organizations have already invested in conversational AI technologies while its market is expected to be worth $49.9 billion by 2030.
Here are key conversational AI trends shaping the future of manufacturing:
- Integration with IoT (Internet of Things) for Real-Time Insights: AI copilots will integrate with IoT-enabled sensors and cameras to monitor machine performance, detect anomalies, and alert technicians before failures occur. Conversational AI can help workers with live equipment diagnostics, receive predictive maintenance alerts, and access real-time performance data hands-free.
- AI-Powered Augmented Reality (AR) Support: Augmented reality will influence how technicians interact with complex machinery. AI-driven AR overlays will provide visual step-by-step repair instructions, highlight faulty components, and even connect workers with remote experts for real-time guidance. According to a McKinsey report, the AR manufacturing segment will be worth around $100 billion by 2030.
- Self-Learning AI Assistants: AI assistants are becoming more adaptive and context-aware. Instead of just retrieving information, future AI copilots will learn from past interactions, recognize user preferences, and offer proactive recommendations. This means more personalized troubleshooting, faster onboarding for new employees, and AI that continuously improves based on real-world usage.
As manufacturers adopt AI while keeping human workers at the core, conversational AI can act as a knowledge retrieval assistant to reduce the skill gap in the industry.
Learn more about how manufacturers can leverage Makula’s Industrial AI to make machine-specific data more accessible and practical. Request a free implementation worth $2,000 today.