In the last three years, 82% of businesses across all industries have had at least one unscheduled downtime disruption, with an average of two outages (Business Wire, 2017). Downtime in manufacturing can grind production to a halt, costing facilities more than just revenue—think lost opportunities and increased stress.
If you've ever pondered the real cost of these interruptions and how to minimize their impact, you're in the right place. We're about to dive into the essence of downtime, dissecting its impact, exploring its causes, and sharing strategies to keep your operations running smoothly.
This article will explore:
- The significant impact of manufacturing downtime.
- Causes of downtime with tailored mitigation strategies.
- The role of CMMS software in reducing downtime.
Makula enters the scene here as a straightforward, powerful tool designed to streamline your operations. It's about enhancing what works, fixing what doesn't, and doing so in a way that seamlessly integrates into your daily workflow. Makula offers clear, effective solutions to keep your production lines moving.According to a recent report, unplanned downtime now costs Fortune Global 500 firms almost $1.5 trillion, or 11% of their yearly revenue (Siemens, 2023). Downtime in manufacturing can throw a wrench in the most finely-tuned operations, leading to significant losses.
1. Planned downtime vs unplanned downtime
Planned downtime is a strategic pause in operations, meticulously scheduled for maintenance, upgrades, or system improvements. It's a deliberate, calculated break, designed to enhance long-term efficiency, reliability, and performance of machinery and systems. This period allows for the careful inspection, repair, and optimization of equipment, ensuring that operations run smoothly and efficiently when back online.
Unplanned downtime, conversely, strikes without warning, disrupting production schedules and causing operational chaos. It occurs when equipment fails unexpectedly, halting production processes and leading to significant financial losses, stress, and pressure to swiftly rectify issues. These unscheduled breaks can stem from various factors such as equipment failure, supply chain issues, or external disruptions, often occurring at the most inopportune times necessitating immediate, reactive measures to minimize impact.
While planned downtime is a controlled strategy for improvement, unplanned downtime is a wildcard that tests your resilience and adaptability.
2. The impact of downtime in manufacturing
Downtime slows things down and sends ripples across every facet of manufacturing. From ballooning costs to stressed-out teams, the effects are far-reaching.
Financial impacts
Equipment outages lasting one hour usually cost $260,000 (Aberdeen Group, 2016). Downtime's financial bite is twofold: immediate loss in production and the longer-term impact on customer trust and market position. Every moment your line isn't running, you're not just losing product; you're losing ground. It's a silent drain on resources that can bleed a company dry if not managed.
Operational repercussions
The operational effects of downtime go beyond halted production lines. 44% of facilities require maintenance for more than 40 hours each week (Plant Engineering, 2021). They create a domino effect that disrupts schedules, delivery timelines, and inventory management. When one piece of the puzzle goes missing, the whole picture can fall apart. It's about more than just lost time; it's about the scramble to recover, which can strain even the most robust systems. Recovering from such disruptions requires significant effort and resources, often straining systems to their limits and impacting the overall efficiency and productivity of the operation.
Effects on employees and safety
Beyond the balance sheet and operational logistics, downtime takes a toll on your most valuable asset—your people. Stress, overtime, and safety concerns can escalate quickly, affecting morale and overall workplace culture. The rush to resume production often leads to the neglect of standard safety protocols, increasing the risk of accidents and injuries. This environment not only puts employees at risk but also challenges the integrity and safety culture of the entire operation.
Customer relationships and market position
The ripple effects of downtime extend to customer relationships and market position as well. Delays in production and delivery can erode customer trust and satisfaction, potentially leading to lost clients and diminished market share. Customers rely on timely and reliable service; when manufacturers fail to meet these expectations due to downtime, it can damage long-standing relationships and reputations. The inability to deliver as promised can also open the door for competitors, further impacting a company’s standing in the market.
3. Diagnosing causes of downtime in manufacturing
Within the facilities of the respondents, aging equipment continues to be the primary source of unscheduled downtime (44%), with human error (16%) and lack of time (15%) following closely behind (Plant Engineering, 2018). Digging into the root causes of downtime uncovers a mix of predictable and unforeseen challenges. It's a detective's job, requiring keen observation and swift action.
Equipment failure
Equipment failure is often the most visible culprit behind downtime. Whether it's a critical machine going kaput or a minor component wearing out, the result is the same—production grinds to a halt. These incidents not only disrupt the workflow but also lead to significant financial losses due to the unexpected pause in operations. The frequency and unpredictability of equipment failures pose a constant threat to maintaining seamless production processes.
Maintenance activities and changeovers
Maintenance activities and changeovers represent a balancing act between necessary pauses and keeping the production line moving. Scheduled downtime for maintenance or swapping production to a new line is essential for long-term efficiency but can be a significant source of lost production time if not managed effectively. Schedule and cost improvements of up to 30% can be achieved through better shutdown and turnaround management (McKinsey, 2016).
However, the process of halting production to carry out maintenance or to switch to a new production line can lead to substantial production time loss. These necessary pauses, if not managed with precision, can significantly impact productivity and operational flow.
Supply Chain issues
Supply chain issues can throw a wrench in the works unexpectedly, causing downtime that ripples through your manufacturing process. From delayed raw material deliveries to disruptions in logistics, these challenges require a nimble response. These problems are often beyond the control of a single facility, stemming from external factors that can range from global supply chain breakdowns to local delivery challenges, making them particularly difficult to predict and manage.
External factors
External factors, such as weather disruptions, power outages, or market fluctuations, can introduce unexpected downtime, challenging even the best-prepared facilities. These factors are external to the manufacturing process but can have a significant impact on operational continuity. For example, severe weather can disrupt power supplies or logistics, power outages can halt production machinery, and market fluctuations can lead to sudden changes in demand.
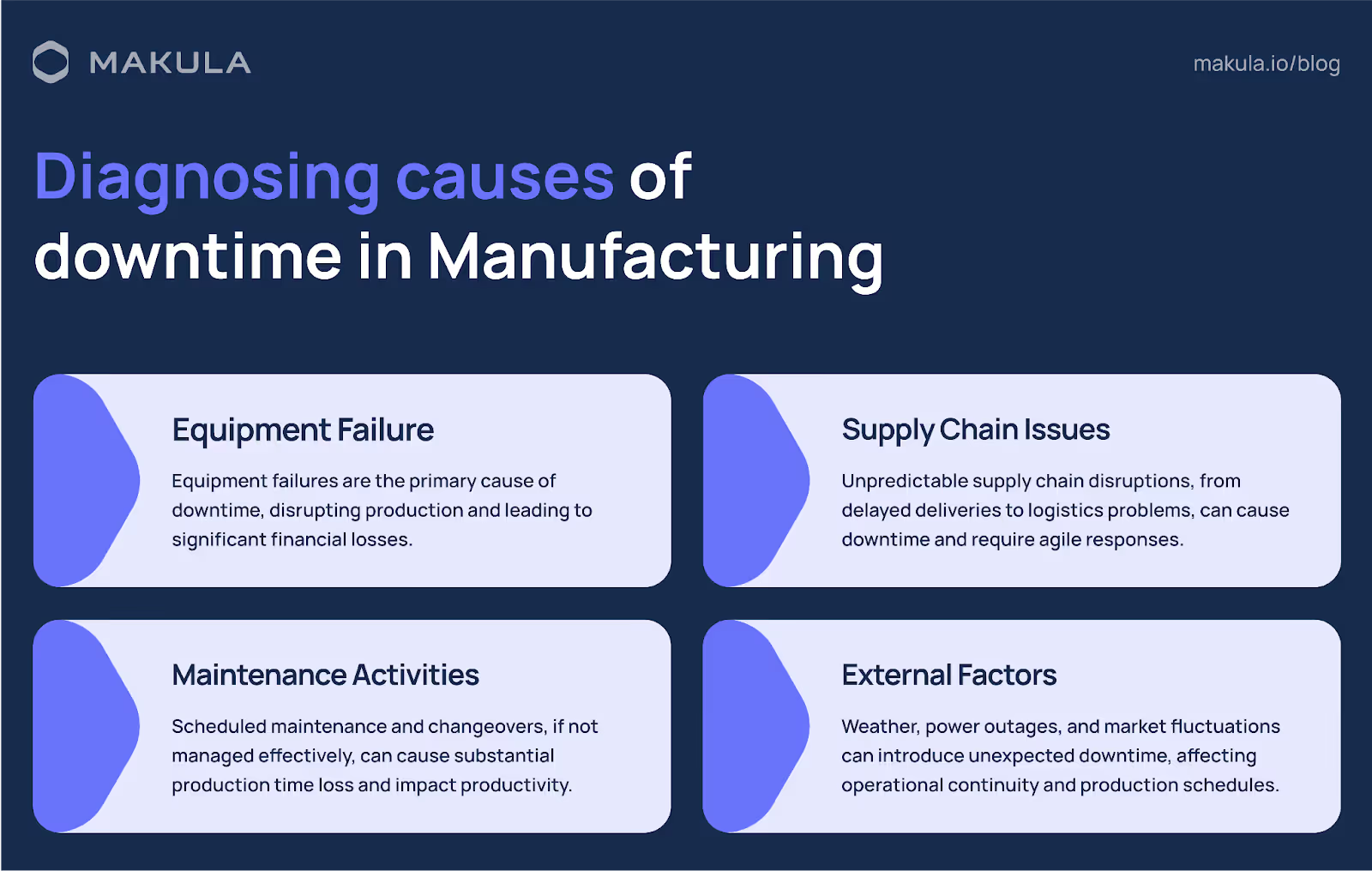
4. Strategies for downtime mitigation and measurement in manufacturing
Poor maintenance practices today can cut a plant's total productivity by 5 - 20% (PTC, n.d.). Mitigating downtime isn't just a quick fix; it's about laying a foundation for resilience and efficiency. It’s where foresight meets action.
Preventive measures and maintenance
76% of manufacturing facilities use preventive maintenance today (Plant Engineering, 2016). Preventive maintenance isn't the most glamorous part of manufacturing, but it's arguably the most crucial. By regularly checking and servicing equipment, you can catch small issues before they escalate into major problems. Think of it as keeping your machinery in tip-top shape, so it's always ready to perform. This strategy focuses on maintaining all machinery and systems in optimal condition to prevent unexpected breakdowns and ensure they operate at peak efficiency.
Optimizing Supply Chain Management
A streamlined supply chain is your safety net against the unpredictable. By optimizing inventory levels and establishing strong relationships with suppliers, you can cushion the blow when external factors threaten to disrupt your operations. It's about having the right parts at the right time and the flexibility to adapt when those plans change. With Makula, you can better anticipate supply needs and manage relationships with suppliers, keeping your production line moving no matter what comes your way.
Analyzing and measuring downtime with a CMMS
Utilizing a CMMS software like Makula for analyzing and measuring downtime brings a data-driven approach to identifying and addressing production inefficiencies. By tracking downtime incidents and their causes, CMMS software enables you to pinpoint areas for improvement, assess the effectiveness of maintenance strategies, and make informed decisions to minimize future downtime. Leveraging the insights provided by a CMMS can significantly enhance operational transparency, allowing for more targeted and effective downtime mitigation efforts.
5. Role of CMMS software in improving downtime in manufacturing
80% of businesses believe that a CMMS increases productivity in industrial maintenance (Advanced Technology, 2020). A Computerized Maintenance Management System (CMMS) software can transform how you tackle downtime in manufacturing, making processes more efficient and less frequent. By digitizing maintenance operations, a Maintenance Management System empowers you to preempt problems and streamline workflows.
Preventive Maintenance
With CMMS software like Makula, setting up and adhering to a preventive maintenance schedule becomes straightforward and automated. This system enables you to track maintenance activities and predict future needs based on equipment usage and historical data. Regular, systematic checks and maintenance work can prevent the sudden breakdowns that lead to costly downtime, ensuring your machinery operates reliably and at full capacity.
Work Order and Inventory Management
A Maintenance Management System simplifies the creation, tracking, and completion of work orders, making it easier for you to manage maintenance tasks efficiently. It also keeps your inventory of parts and supplies in check, alerting you when stocks are low and need replenishment. This dual functionality ensures that necessary maintenance is performed without delay, and the right parts are always available, reducing the downtime associated with waiting for repairs or parts.
Asset Management and monitoring
Effective asset management and monitoring are at the heart of a Maintenance Management System. This feature provides a comprehensive view of all your assets, including their condition, history, and performance data. With real-time monitoring and analytics, you can make informed decisions about maintenance, replacements, and investments, minimizing unplanned downtime and extending the lifespan of your equipment. Makula’s proactive approach keeps your operations running smoothly and efficiently.
6. Key takeaways
- Unplanned downtime in manufacturing costs Fortune Global 500 companies nearly $1.5 trillion annually, highlighting the critical need for efficient downtime management and mitigation strategies.
- Preventive maintenance, optimizing supply chain management, and the strategic use of CMMS software like Makula are essential in minimizing manufacturing downtime and ensuring operational efficiency.
- The financial and operational impact of downtime extends beyond immediate production losses, affecting customer trust, employee stress, and safety, underscoring the importance of proactive measures.
- Analyzing and measuring downtime with CMMS software provides data-driven insights for targeted improvement, making maintenance more predictive and less reactive, thereby enhancing productivity.