In the world of machine manufacturing, smooth operations are crucial to success. Yet many companies face a hidden challenge: inefficiencies that can eat away up to 30% of their revenue yearly. What's more concerning is that these inefficiencies can also affect after-market services, which provide 40-50% of the net profit. This is where the power of effective work order management comes into play.
It's not just about fixing problems; it's about preventing them, ensuring machines work well and businesses thrive. With such a large portion of revenue and profit at stake, implementing digital work order management is not just beneficial—it's essential for any machine manufacturer aiming for success and sustainability.This article emphasizes the significance of work order management and its role in enhancing business efficiency and success.
1. Understanding Work Order Management
Work order management is a systematic approach to organizing and tracking service requests related to your manufactured machines. It encompasses the entire lifecycle of a service call, from the initial customer request to completion and final invoicing. According to a research report, the work order management systems market, valued at USD 532.50 million in 2021, is projected to reach USD 1176.80 million by 2029, growing at a CAGR of 10.42%. Effectively managing work orders involves:
- Creating work orders: Capturing key details like customer information, machine type, problem description, and desired resolution.
- Assigning technicians: Matching the right technician with the required skills and experience for the specific job.
- Scheduling appointments: Optimizing technician schedules to minimize travel time and maximize service calls.
- Tracking progress: Providing real-time updates on the status of each work order, allowing for proactive communication with customers.
- Managing inventory: Ensuring technicians have the necessary parts readily available to complete repairs efficiently.
Components of a typical Work Order
Effective work orders include several essential components. Some of the most common among them are:
- Work Order Number: A unique ID for tracking and referencing.
- Description of the Task: A detailed description of the required work, including specific issues to address.
- Location: Where the maintenance work will take place.
- Asset Details: Information on the equipment or facility, including model, serial number, and historical maintenance data.
- Priority Level: The urgency of the work order to help prioritize tasks.
- Assigned Personnel: Names or roles of those responsible for the work order.
- Estimated Time and Resources: A projection of the time and resources needed to complete the task.
- Completion Date: When the work order should be finished.
- Instructions and Safety Precautions: Step-by-step instructions and safety measures for the task.
- Feedback and Notes Section: Space for workers to provide feedback, note any issues, and document any changes from the initial plan.
2. What happens when digital work order management isn't utilized?
Without a centralized system for tracking work orders, tasks can become easily lost or forgotten. This can lead to confusion and delays as technicians struggle to determine priorities and next steps. Missed deadlines become a real possibility, potentially impacting customer satisfaction and loyalty.
Inefficient resource allocation
Effective work order management allows for a clear picture of available resources, including technicians, parts, and tools. When such a system is absent, resource allocation becomes haphazard. Technicians might be assigned tasks beyond their skill set, leading to rework and wasted time. Additionally, urgent repairs might be delayed due to a lack of readily available parts.
Difficulty in tracking progress and identifying bottlenecks
Without a centralized system, tracking the progress of individual work orders and overall repair processes becomes a major challenge. Identifying bottlenecks in the service workflow becomes near impossible, hindering efforts to optimize efficiency and improve service times.
Increased risk of errors and safety issues
When work orders lack clear documentation and proper tracking, the risk of errors increases significantly. Incorrect parts might be ordered, leading to delays and additional costs. Moreover, the absence of clear work instructions could potentially compromise safety protocols during repairs.
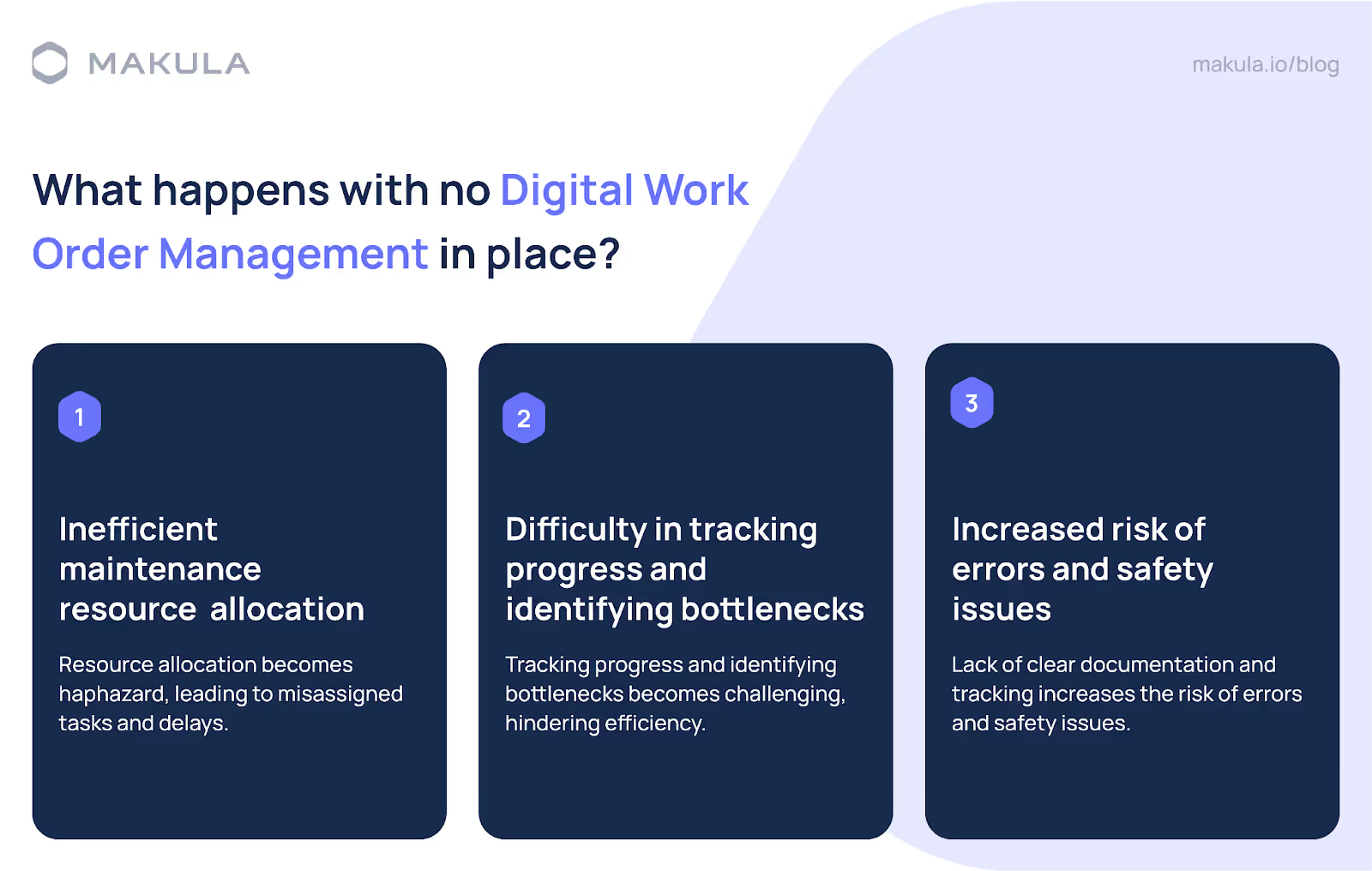
3. The Importance of Work Order Management for machine manufacturers
By providing a structured approach to managing maintenance tasks, work order management offers several key benefits that directly impact the bottom line and operational success.
Improved efficiency
- Streamlining operations: Automating the creation, assigning, and tracking of work orders eliminates the need for cumbersome paper-based systems, reducing the time and effort required to manage maintenance tasks.
- Reduce manual errors: Digital work order management system minimizes the risk of human error, ensuring that maintenance tasks are executed accurately and efficiently.
Enhanced communication
- Centralizes information: All information related to maintenance tasks, including schedules, task details, and asset information, is stored in a central location, easily accessible by all relevant parties.
- Facilitates updates and notifications: Automated alerts keep everyone informed about task progress, schedule changes, and urgent maintenance needs, ensuring no critical information is missed.
- Improves team collaboration: By providing a shared platform for communication, work order management systems enhance collaboration among team members, leading to more efficient problem-solving and task completion.
Better planning and scheduling
- Optimizes resource allocation: The system's ability to track and analyze maintenance data enables manufacturers to allocate resources more effectively, ensuring that the right personnel and materials are available when needed.
- Allows for Preventive Maintenance: 82% of companies have experienced unplanned downtime in the last three years, which costs manufacturers $50 billion each year. Scheduling preventive maintenance tasks based on equipment usage and historical data helps prevent unexpected breakdowns and extend machinery's lifespan.
- Improves project timeline: With clearer visibility into maintenance schedules, manufacturers can plan projects more accurately, ensuring that deadlines are met without compromising quality.
Employee satisfaction
- Empowerment through transparency: Work order management systems offer employees clear visibility into their tasks, expectations, and deadlines, empowering them with the information they need to perform their jobs effectively. This encourages employees to feel autonomous and engaged. Considering the growing issue of skilled labor shortages, this can be critical.
- Skill development: By systematically assigning tasks based on skill level and tracking performance, these systems facilitate skill development. This not only boosts morale but also encourages continuous professional growth.
- Recognition of efforts: Work order management helps you appreciate efforts that go unseen. By having this traceability, you can not only appreciate employees for their work but also properly charge your customers for the work that has been performed for them.
Customer trust
- Timeliness and reliability: Prompt and efficient handling of work orders ensures that customer requests are addressed professionally, significantly boosting customer trust and satisfaction. This reliability in service delivery can transform first-time clients into loyal customers.
- Quality of service: Standardized procedures and adherence to best practices ensure that customers receive consistent, high-quality service. This enhances the business’s reputation and fosters trust among its clientele.
- Proactive problem-solving: Tracking and analyzing trends in maintenance requests allows businesses to proactively address potential issues before they escalate, demonstrating commitment and building trust with customers.
Facilitating onboarding of young technicians
- Structured framework for learning: Work order management systems offer new technicians a clear understanding of their roles through access to historical data and standard procedures, accelerating the learning curve.
- Digital engagement: Leveraging technology in work order management appeals to young, tech-savvy technicians and fosters a sense of belonging and engagement.
- Role clarity and expectation setting: These systems help clearly define the responsibilities and quality standards expected of new hires, setting a solid foundation for them.
Increased accountability
- Tracks task progress: Real-time tracking of maintenance tasks allows managers to monitor progress and address any delays promptly.
- Monitors worker performance: The system provides insights into individual performance, helping to identify training needs and recognize outstanding contributions.
- Ensures task completion: Automated follow-ups and notifications help ensure that all maintenance tasks are completed as scheduled, maintaining operational continuity.
Cost savings
- Reduces operational costs: Efficient management of maintenance tasks leads to fewer breakdowns and less downtime, significantly reducing operational costs. For example, predictive maintenance can decrease maintenance expenses by 25%.
- Optimizes asset usage: By maximizing machinery efficiency and lifespan, manufacturers can get the most out of their assets, reducing the need for premature replacements.
- Prevents unnecessary expenditures: Preventive maintenance and efficient resource allocation help avoid costly emergency repairs and wasteful spending.
Improved compliance
- Ensures regulatory compliance: Work order management systems help ensure that all maintenance activities comply with industry standards and regulations, reducing the risk of fines and legal issues.
- Enhances safety measures: By scheduling regular maintenance and safety checks, the system helps maintain a safe working environment. This protects technicians and prevents equipment failure.
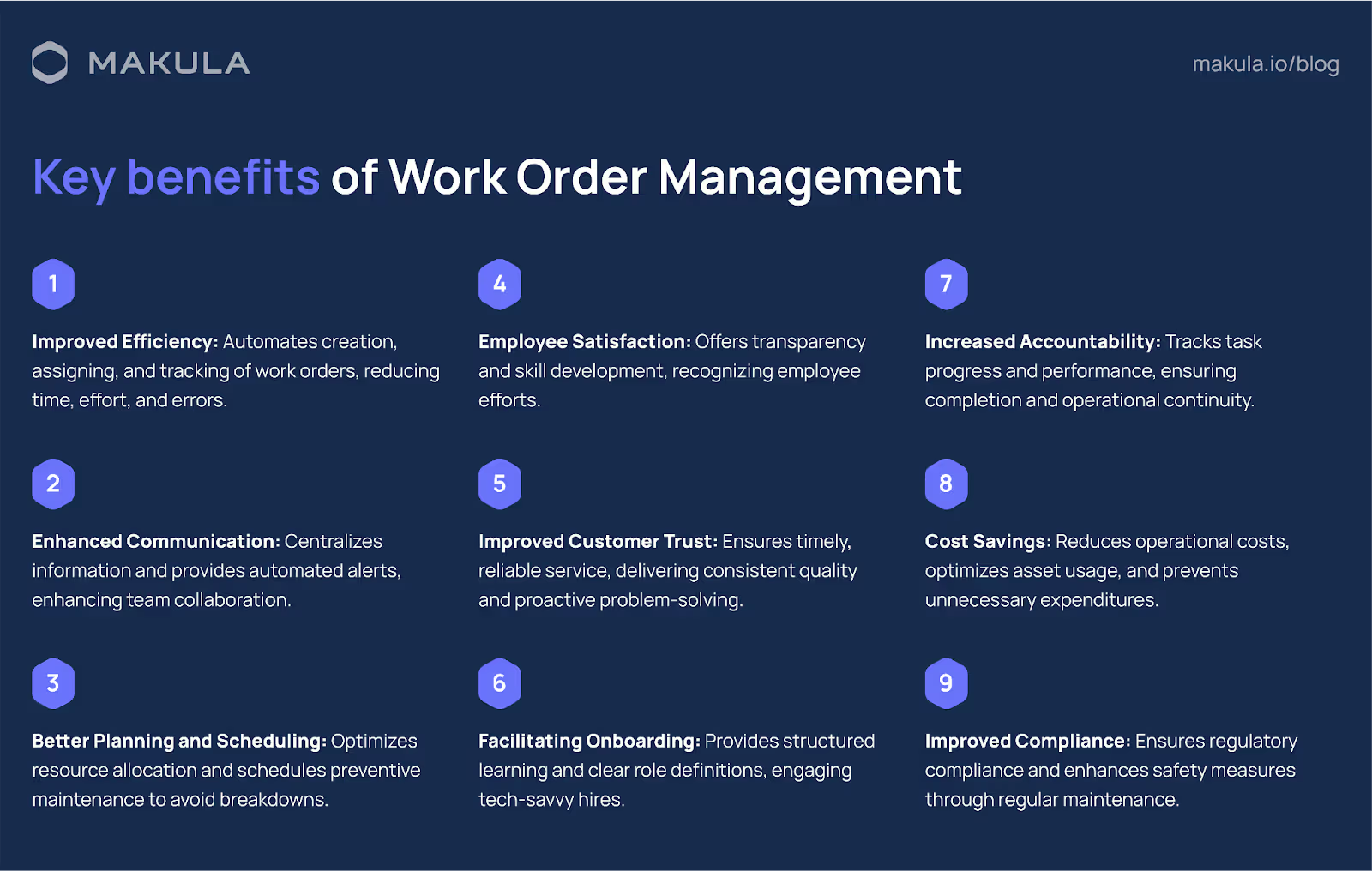
4. Work Order Management best practices
Implementing best practices in work order management can significantly enhance the efficiency and effectiveness of handling tasks across various industries. Here are some key strategies:
Implementing a standardized process
Establishing standard procedures for issuing, executing, and closing work orders ensures consistency and efficiency. A standardized work order management process reduces confusion, sets clear expectations, and provides a framework for measuring performance and making improvements.
Leveraging analytics and technology
Utilizing work order management software can dramatically improve the accuracy and speed of creating, tracking, and closing work orders. Technology solutions offer real-time updates, inventory management, scheduling tools, and analytics, facilitating informed decision-making and resource allocation.
Continuous training and improvement
Regular staff training sessions on the latest technologies, best practices, and safety protocols ensure that all team members can execute their duties effectively. Additionally, adopting a culture of continuous improvement, where feedback is actively sought and implemented, can significantly enhance work order management processes.
Real-world examples of effective work order management
Schneider Electric
Schneider Electric, a leader in energy management and automation solutions, employs a digital work order management system. These algorithms analyze data to optimize work order scheduling and resource allocation. This allows Schneider Electric to streamline service operations, reduce overall turnaround times, and ultimately enhance customer satisfaction.
General Electric (GE)
General Electric empowers its service teams with work order management systems that utilize advanced data analytics. This allows GE to optimize technician schedules and ensure the right people with the right skills are assigned to specific jobs. This data-driven approach fosters efficient resource allocation and minimizes wasted time.
Honeywell
Honeywell is a diversified technology company that leverages a cloud-based work order management system. This solution offers several advantages. Firstly, it ensures all data is readily accessible from any location. Additionally, cloud-based systems offer scalability, allowing Honeywell to easily adapt the system to their evolving needs. This empowers them to manage service operations effectively as their business grows.
Airbus
Airbus, a giant in aerospace manufacturing, leverages digital systems for predictive maintenance. These systems analyze aircraft sensor data to anticipate potential issues before they escalate. Proactive work orders are then generated, allowing Airbus to address minor concerns before they become major problems. This not only reduces downtime for airlines but also enhances overall flight safety.
Wrapping up
The importance of work order management in today’s rapidly evolving business landscape cannot be overstated. This systematic approach streamlines maintenance tasks and critically enhances overall operational efficiency, accountability, and proactive maintenance strategies. Businesses that have switched from traditional, manual methods to modern, technology-driven work order maintenance systems report significant improvements in productivity, cost savings, and customer satisfaction.
With Makula, you can streamline operations, optimize resource allocation, and prioritize preventive maintenance – all through a user-friendly, digital platform. Request a free demo today and discover how our digital work order management solution can transform your service operations.