Asset productivity is a top concern for all organizations with 99 percent of participants reporting that their companies had implemented a maintenance transformation within the previous five years (McKinsey, 2023). Are you looking to optimize your machine maintenance efforts but facing hurdles even when using advanced equipment? You're not alone in facing these challenges. This article will guide you through the essential steps of developing and implementing an effective machinery maintenance plan, helping to prevent common pitfalls.
Here’s what we'll cover:
- Machine Maintenance: Key practices for maintaining machinery efficiency.
- Machinery Maintenance Plan: Comprehensive strategies to ensure equipment longevity.
- Maintenance Scheduling: Timing maintenance activities to minimize operational disruptions.
- Critical Asset Management: Identifying and prioritizing the maintenance of crucial machinery components.
Machine maintenance is important to ensure your equipment operates efficiently and lasts as long as possible. This process involves regular checks, repairs, and replacements of parts to keep machines running smoothly and prevent unexpected breakdowns. By familiarizing yourself with different types of maintenance—preventive, predictive, and corrective—you can tailor a maintenance strategy that fits the unique demands of your operation and minimizes equipment downtime.
Preventative maintenance is essential for optimizing the performance and lifespan of your machinery. By implementing a routine where you regularly inspect and maintain equipment before problems occur, you can significantly reduce the likelihood of unexpected failures that disrupt production and incur high repair costs. Compared to reactive maintenance, the preventative approach extends the operational life of your machines and enhances safety in the workplace. Through consistent preventative maintenance, you can ensure that your equipment operates within safe parameters, protecting both your workforce and your investment.
1. Planning: The foundation of reliability
29% of plants allocate between 5 and 10% of their yearly budget to maintenance (Plant Engineering, 2021). A machinery maintenance plan is the cornerstone of effective machine maintenance. It involves setting clear, strategic objectives for maintaining your equipment, and ensuring that every action taken is aimed at enhancing reliability and preventing downtime.
Identifying critical assets
When identifying critical machinery, focus on the operational importance and potential impact of failure. Start by evaluating which machines are integral to your core operations—those without which your production would stall or output quality would significantly decrease. Also, assess the failure impact: consider both the direct costs of repairs and the broader consequences like production delays, safety risks, and potential loss of business.This dual focus helps you prioritize maintenance efforts where they are most crucial, ensuring stability and efficiency in your operations. Makula’s asset tracking features can help you precisely identify and prioritize critical machinery for maintenance with advanced analytical features.
Documenting Asset Inventory
Creating a comprehensive list of your machinery and equipment is a foundational step in your machinery maintenance plan. Begin by documenting all assets, including their make, model, serial number, and purchase date. For each piece of equipment, record its location, current condition, and performance metrics. This inventory aids in tracking and scheduling maintenance to quickly identify which assets may require upgrades or replacements. Keep this inventory updated to reflect changes such as new acquisitions, disposals, or major repairs.
Determining maintenance frequencies
44% of plants require maintenance for more than 40 hours each week (Plant Engineering, 2021). Utilizing manufacturer recommendations is crucial for establishing initial maintenance intervals for your machinery. These guidelines provide valuable insights into the expected operational lifespan of components and the optimal frequency of maintenance tasks. Adhering to these recommendations can help prevent premature wear and tear and maintain the warranty conditions of your equipment. Additionally, aligning your maintenance schedule with manufacturer guidelines ensures that you are using best practices tailored specifically to each piece of equipment’s design and intended use.
Historical Data Analysis
Analyzing past maintenance records plays a critical role in shaping effective maintenance frequencies. Review the logs of repairs, replacements, and routine checks to identify patterns or recurring issues with each asset. This historical data allows you to adjust maintenance intervals based on actual equipment performance rather than solely on theoretical models or averages. By understanding the specific maintenance needs and failure rates of your machinery, you can more accurately predict future needs and prevent breakdowns, optimizing both maintenance costs and equipment uptime.
Risk-based maintenance scheduling
93% of businesses believe their maintenance procedures are inefficient (CXP Group, 2018). Risk-based maintenance scheduling tailors the machinery maintenance plan to the unique risk profile of each asset. Evaluate the likelihood and potential impact of failure for each machine, then prioritize maintenance tasks based on this assessment. This method ensures that resources are focused where they are most needed, enhancing overall equipment effectiveness and safety. By adopting a risk-based approach, you prevent critical failures and optimize your maintenance resources for maximum efficiency.
Streamline your maintenance scheduling with Makula's automated scheduling tools, designed to minimize operational disruptions by planning maintenance tasks during optimal times.
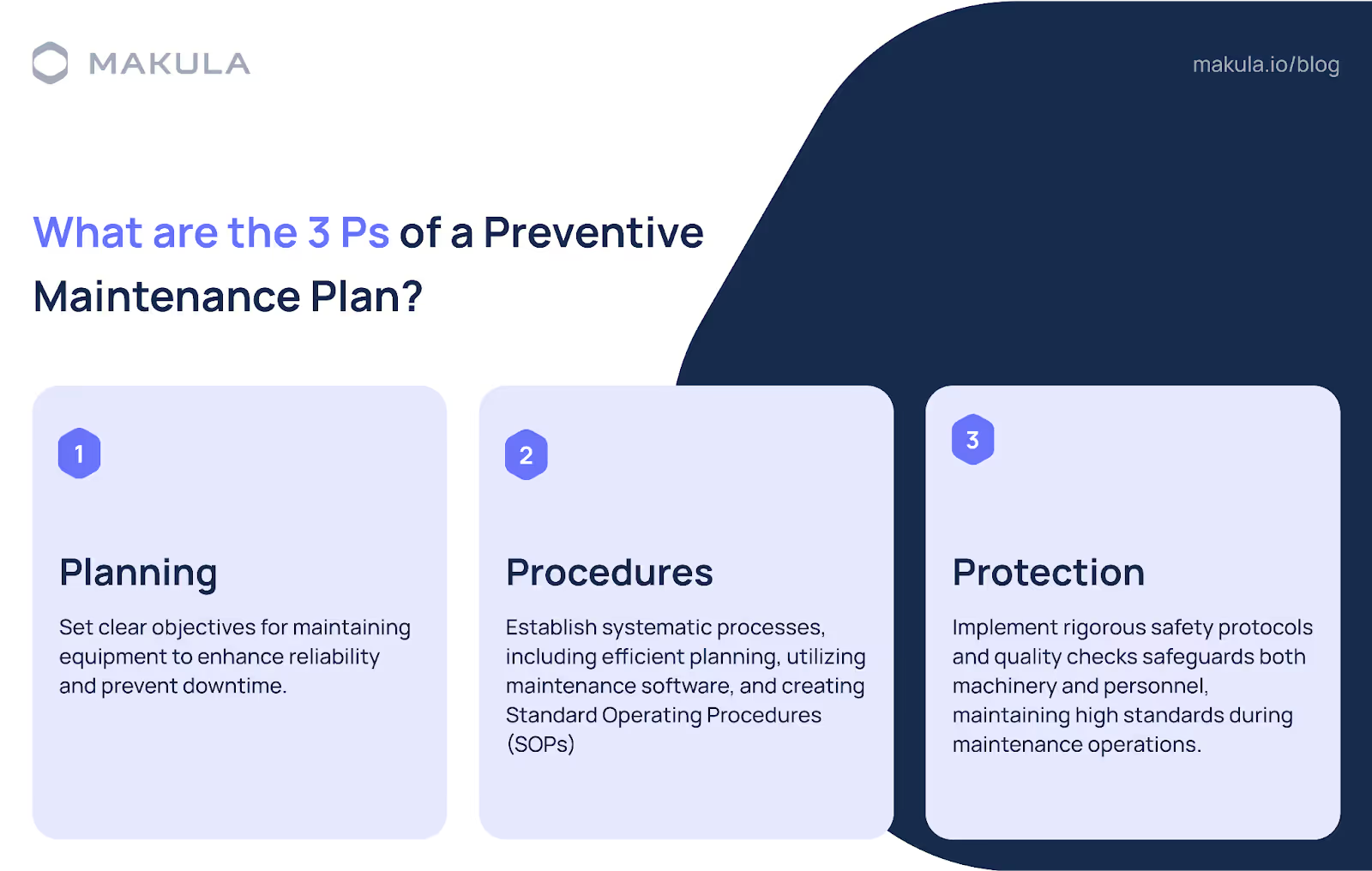
2. Procedures: The blueprint for success
Procedures form the backbone of your maintenance strategy, transforming plans into actionable steps. This stage focuses on establishing systematic processes to ensure that maintenance tasks are performed effectively and efficiently.
Efficient planning strategies
Of the firms, 46% want to develop or modify their maintenance policy to reduce downtime (Advanced Technology, 2020). To minimize operational disruptions, efficient planning of maintenance activities is crucial. Schedule maintenance during low-production periods or when machine usage is at its minimum to reduce the impact on operations. Use downtime effectively by preparing all necessary tools, parts, and personnel in advance. This proactive scheduling enhances productivity and reduces the time machines are out of service, thereby maintaining a steady workflow.
Maintenance software utilization
80% of businesses believe that industrial maintenance productivity is increased by a CMMS (Advanced Technology, 2020). Using specialized maintenance management software can significantly streamline your maintenance processes. These systems offer features like automated scheduling, real-time alerts, and comprehensive tracking of maintenance activities. By integrating such software, you can ensure a more organized approach where maintenance tasks are systematically managed and nothing gets overlooked. This boosts your maintenance team’s efficiency and enhances data accuracy, which is critical for making informed maintenance decisions.
Creating Standard Operating Procedures (SOPs)
The importance of creating Standard Operating Procedures (SOPs) for each maintenance task cannot be overstated. Detailed SOPs ensure that every maintenance activity is performed consistently and correctly, reducing the likelihood of errors and accidents. These documents should include step-by-step instructions that are easy to follow, ensuring that all team members, regardless of their experience level, can execute tasks accurately and safely. This standardization helps maintain high-quality maintenance work across the board.
Maintenance record keeping
Keeping detailed maintenance logs is essential for successful operational audits and maintaining regulatory compliance. These logs should document every repair, inspection, and routine maintenance task, including dates, details of the work performed, and the names of the personnel involved. Accurate and comprehensive maintenance logs facilitate audits and provide valuable data for improving maintenance planning and strategy. Regularly reviewing these logs can help you identify trends and areas for improvement in your maintenance processes.
Benefit from Makula’s digital maintenance forms to easily create and manage standardized operating procedures and maintain detailed maintenance logs, ensuring regulatory compliance.
3. Protection: The safety and quality guard
Protection ensures that your maintenance strategies safeguard both the machinery and the personnel involved. It emphasizes the importance of maintaining high-quality standards and enforcing rigorous safety protocols during maintenance operations.
Conducting quality checks
The largest difficulty, according to 39.9% of maintenance managers, is equipment reliability (ABL Group, 2022). Quality checks are integral to maintaining the reliability and performance of your equipment. Implement regular inspections and testing protocols to verify that all machinery meets your critical asset management standards following maintenance. These checks help catch any discrepancies or issues before the equipment is returned to full operation, ensuring that repairs and maintenance have effectively addressed any problems. Prioritize thoroughness and accuracy in these checks to prevent future breakdowns and maintain operational excellence.
Implementing safety measures
It is estimated that maintenance expenses will account for 15% to 40% of overall production costs (Shahin, 2000). Safety measures are critical to protect both your team and your machinery during maintenance operations. Always ensure that all personnel are trained on the latest safety protocols and that they use appropriate safety gear. Regularly review and update your safety procedures to accommodate new regulations, equipment, or maintenance practices. This proactive approach to safety helps prevent accidents and injuries, creating a safer workplace and maintaining high morale among your staff.
Continuous improvement and monitoring
Continuous improvement and monitoring are essential for adapting and refining your maintenance strategy over time. Use data from maintenance logs, quality checks, and machine performance metrics to identify areas for improvement. Implement regular reviews of your maintenance processes and integrate feedback from the maintenance team to ensure that your approach remains effective and efficient. This ongoing process of evaluation and adaptation helps in achieving higher reliability and performance from your equipment, aligning your maintenance practices with the best industry standards.
Utilize Makula's analytics and monitoring tools to facilitate continuous improvement by providing actionable insights from maintenance logs and equipment performance data.
Key takeaways
- Comprehensive planning is crucial: Effective maintenance begins with thorough planning, including asset identification and scheduling based on risk assessments.
- Routine maintenance extends equipment life: Regular preventative maintenance reduces breakdowns and extends the lifespan of machinery.
- Documentation and standardization enhance consistency: Keeping detailed records and standardizing procedures ensure consistency and facilitate audits.
- Leverage technology for efficiency: Maintenance management software streamlines operations and improves scheduling and tracking efficiency.
- Safety and quality are paramount: Rigorous safety protocols and quality checks are essential for protecting staff and ensuring machinery operates correctly.
- Continuous improvement drives success: Regularly updating maintenance strategies based on performance data ensures ongoing effectiveness and alignment with industry best practices.