15 Best CMMS Software for Manufacturing in 2025
The world of Computerised Maintenance Management Software (CMMS) has changed rapidly in the last year. In 2025, factories are under pressure to digitise, reduce downtime, and future-proof their asset maintenance strategies. CMMS tools have evolved from simple scheduling systems into intelligent, cloud-based platforms that integrate predictive analytics, digital twins, and AI-driven diagnostics.
So, which CMMS solutions are truly worth considering in 2025?
We reviewed 15 of the most talked-about platforms, focusing on their strengths, weaknesses, pricing, and suitability for factory operations. Below, you'll find detailed reviews of the top 10 CMMS tools used in manufacturing, followed by a summary of five notable contenders.
Quick Comparison Table
Note: Our top pick is our own product, Makula. We strive for transparency and aim to offer balanced, unbiased information. We're proud of what Makula has to offer and invite you to explore its features and capabilities. For more details, feel free to learn more or schedule a demo.
#1 Makula
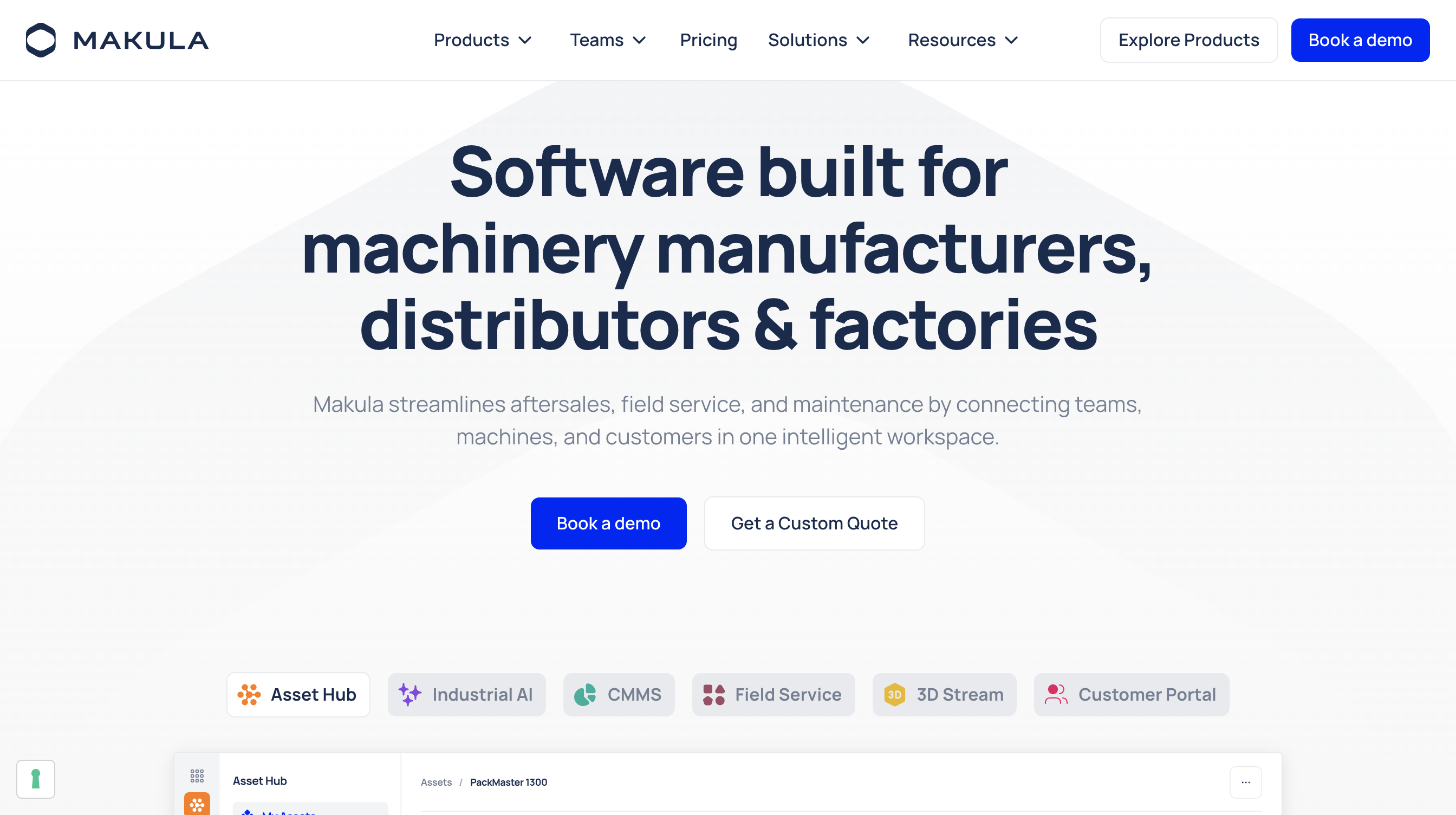
Best for: All-in-One Maintenance Solutions
How it works:
Makula is a comprehensive Computerised Maintenance Management System (CMMS) tailored for factories. It streamlines asset lifecycle management, automates preventive maintenance, and centralises work order coordination. Makula is particularly effective for mid-sized to large manufacturing environments.
What makes it unique:
Makula blends predictive maintenance, real-time analytics, and user-first design. It enhances uptime, improves asset reliability, and boosts team collaboration.
Here’s why Makula is a unique fit for factory operations:
- 3D Visualisation Tools: View machine parts in 3D directly on any device, speeding up issue resolution and improving supplier collaboration.
- User-Friendly Design: Makula is intuitive from day one, with a low learning curve across departments.
- Built for Scale: Designed for operations with 200+ employees, Makula scales effortlessly with your team and asset complexity.
Makula Key Features:
- Work Order Management: Create, assign, and track tasks with calendar, map, and Kanban views. Prioritise work based on urgency and assign accountability clearly.
- Automated Preventive Maintenance: Trigger tasks using meter data or time intervals. Reduce emergency repairs and extend asset lifespans.
- Comprehensive Asset Management: Monitor asset health, history, and status in real time — all accessible via mobile.
- Inventory Management: Never run out of parts. Automate alerts for low stock, track consumption, and optimise spare parts availability.
- Smooth Integrations: Supports API and CSV-based integration with ERP/CRM systems, enabling broader automation.
The Makula Ecosystem
Makula CMMS
Tailored specifically for factories, Makula CMMS is more than digital work orders. It connects maintenance actions to real-time machine data, enabling predictive and prescriptive interventions before breakdowns occur. With full mobility, maintenance teams can trigger alerts, scan assets, and assign tasks from the shop floor.
Asset Hub
Asset Hub is the single source of truth for all your factory assets — digital twin ready. From spare part hierarchies to inspection history, every data point is connected and searchable. Seamless with Makula CMMS, it gives maintenance teams the context they need to act faster and smarter.
Industrial AI
Industrial AI brings intelligent assistance to your maintenance workflows — no sensors or IoT required. It combines three AI-powered tools to supercharge factory productivity:
- AI Machinery Assistant trained on technical documents and manuals for on-the-spot answers
- AI Notetaker for automatic transcription and summary of meetings or field visits
- Enterprise AI Search that understands context across manuals, reports, and historical logs
This makes it easy to troubleshoot, document, and resolve issues without digging through spreadsheets or binders. It's real-world AI for real-world maintenance teams. It identifies patterns that suggest future failures, recommends actions, and even helps predict mean time to repair. Factories using it report fewer surprises and faster root cause analysis.
Pricing:
- CMMS: €55/user/month
- Industrial AI: €39/user/month
- 3D Stream: €49/user/month
- Asset Hub: Flat platform fee (contact us for pricing)
- Enterprise packages: Custom quotes available for bundled solutions
Reviews:
#2 UpKeep
Best for: Flexible Maintenance Management
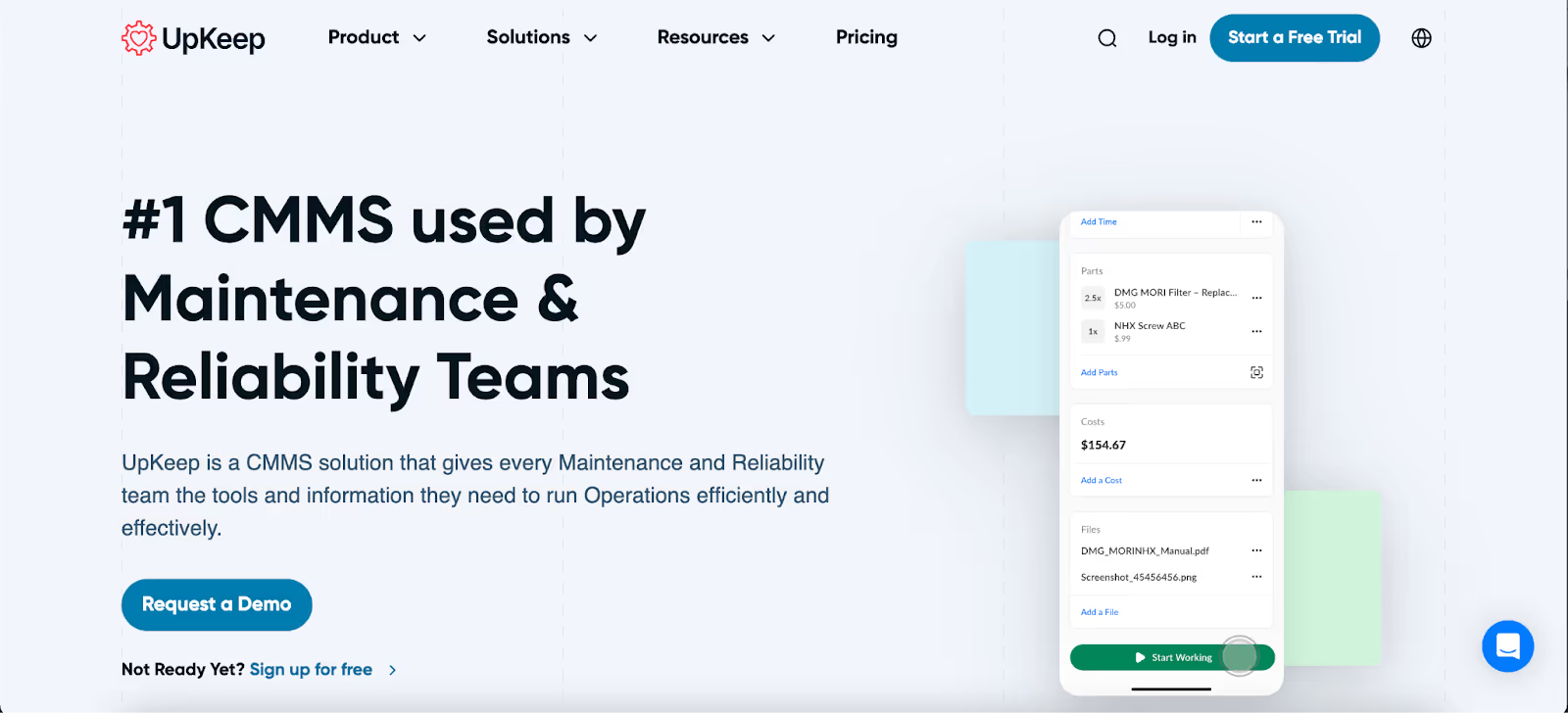
How it Works
UpKeep is a cloud-based CMMS designed for mobile use, making it ideal for maintenance management, reliability, and operations teams. It helps manage the entire maintenance life cycle, optimize asset utilization, and provide real-time performance insights. UpKeep is ideal for industries like manufacturing, construction, warehousing, utilities, and more.
Pros
- The tracking for work orders is convenient and thorough, making reporting easy which helps you identify problem areas and optimize spending.
- Mobile accessibility allows users to get updates, track work, and share progress across their organization directly from their phones.
- Proactive maintenance planning helps with predictive maintenance needs so that your machines are serviced during downtime.
Cons
- Some users have expressed the need for more filters like Conditional Selections to make location-specific selections easier.
- At times, the platform can be slow which can hinder your task completion.
Reviews
"UpKeep's Work Order Management and Asset Tracking platform is an excellent solution for anyone needing to streamline their maintenance operations. The layout of the platform is very user-friendly and easy to navigate." - Justin L.
Pricing
There are three pricing plans billed annually. These start from $45 per user every month, which goes up to $120 per user every month.
#3 Limble
Best for: Small to Medium-Sized Manufacturers
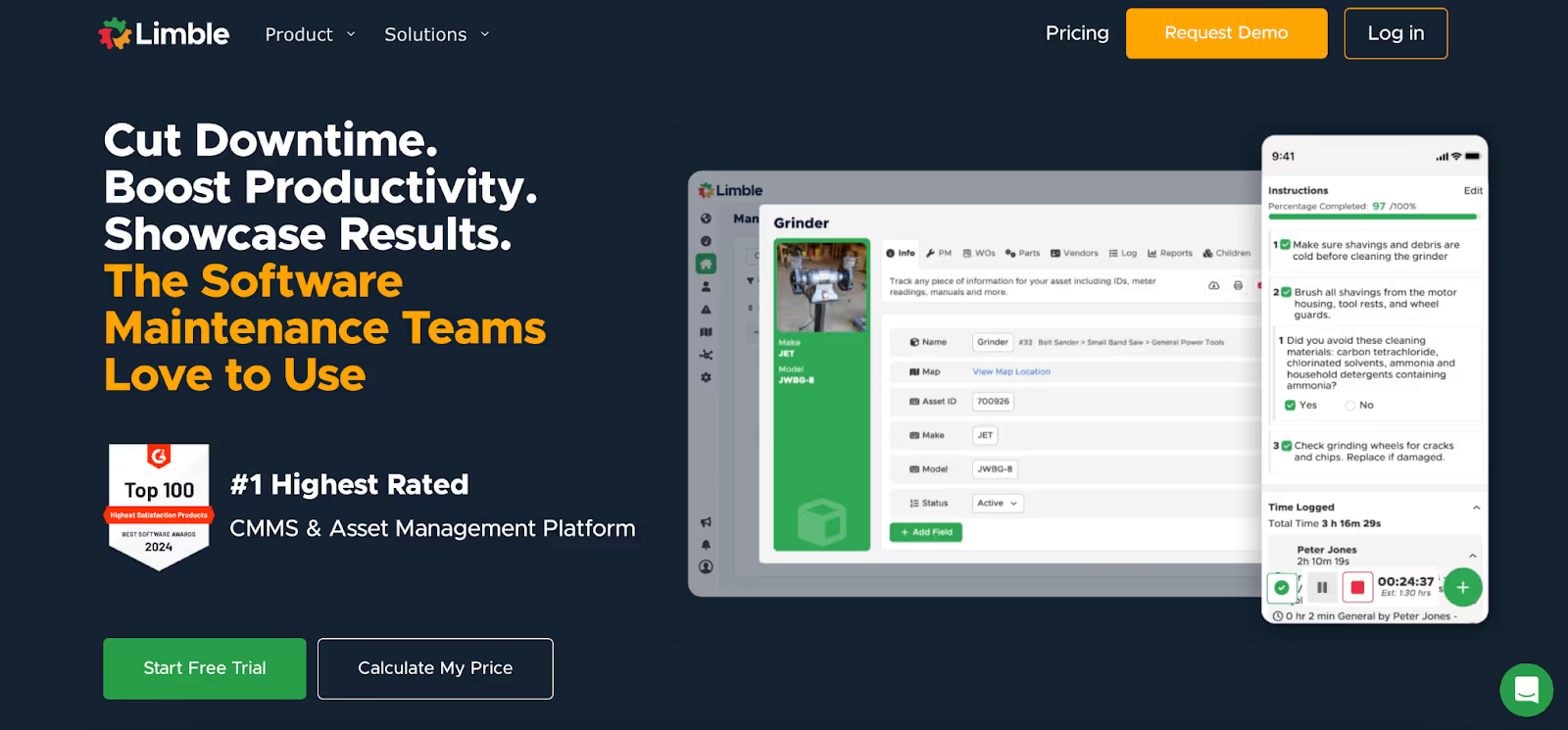
How it Works
Limble CMMS is a modern business software designed to automate preventive maintenance scheduling, improve team efficiency, and track key metrics like labor costs, MTTR (Mean Time to Repair), MTBF (Mean Time Between Failures), and downtime. It is particularly suited for small and medium-sized companies looking for a CMMS solution.
Pros
- Limble allows smooth task assignment to the correct department, breaking down data to provide a comprehensive view of machinery performance. This helps recognize trends and patterns, giving you a clear metric for better decision-making.
- The software is user-friendly and accessible on mobile devices without needing an app, making it easy for employees to request work.
- Limble is highly customizable and lets you modify features to fit your specific needs improving its adaptability.
Cons
- The software requires an internet connection to work, as there is no offline version, and it signs out frequently on mobile devices.
- Asset labeling could be improved, as finding an asset or PM can be challenging without knowing the exact name or number.
Reviews
"Limble allows me to streamline my assets with the work orders and purchase orders. Technicians can be alerted immediately about various situations, and inventory management has become ten times easier with this program." - David W.
Pricing
Limble offers four pricing editions, starting from $28 per month and going up to $69 per month. A free trial is also available.
#4 Maintainx
Best for Industrial and Frontline Teams
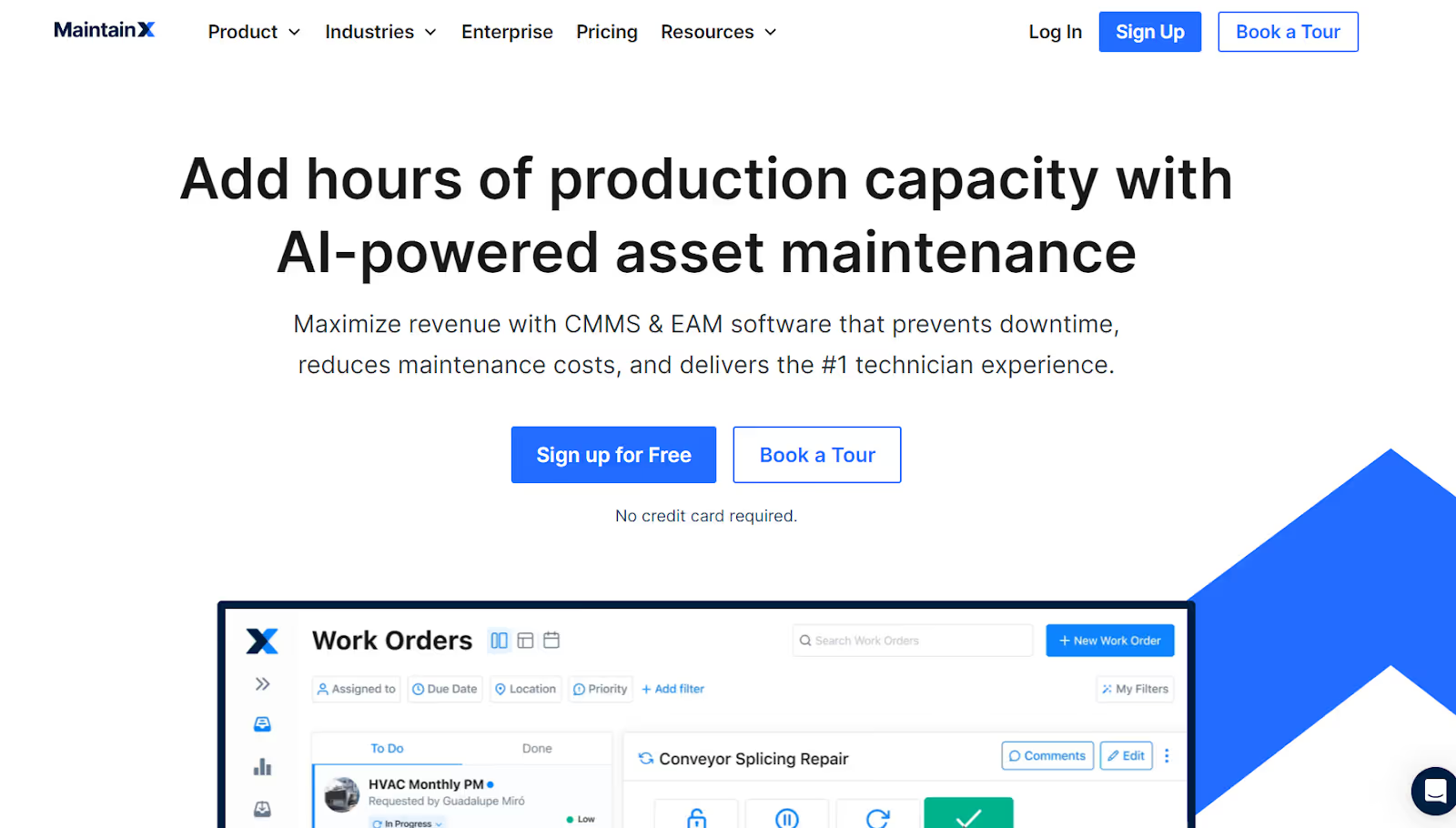
How it Works
MaintainX is a leading maintenance and work execution software designed for industrial and frontline teams. As a mobile-accessible platform, it delivers a modern, IoT-enabled solution for reliability-centered maintenance. Suitable for small to large businesses, MaintainX allows users to track unlimited assets and create countless work orders.
Pros
- The simplicity of MaintainX's interface makes it user-friendly and scalable, even for teams not well-versed in technology.
- MaintainX has great customer support helping users get up and running quickly.
- The software offers real-time access to field data allowing both your remote and in-office staff to create and manage work orders properly.
Cons
- Users report that MaintainX lacks customization options for work orders, such as modifying layouts and adding or removing fields.
- When a repair request is rejected, the submitting users have mentioned that they cannot see the reason for the rejection, which can be frustrating.
Reviews
"As soon as my staff saw how easy it was & the communication improvements from this software they jumped in and have not stopped using it." - Jason A
Pricing
There are four major plans for billing every month, starting from $16 per user and going up to $49 per user.
#5 Remberg
Best for: Complex Maintenance Tasks
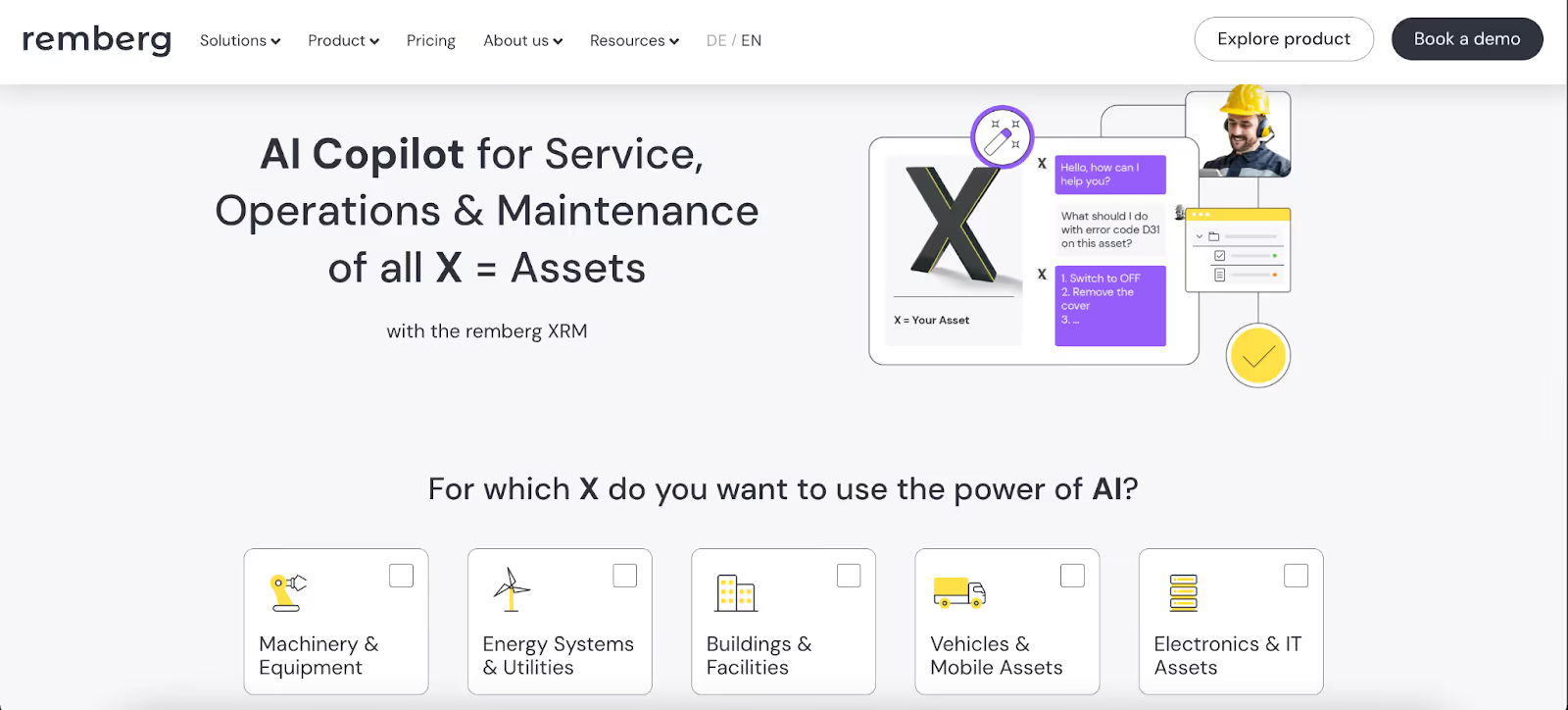
How it Works
Remberg XRM is a software solution for comprehensive asset maintenance, including ticket management, scheduling, and planning. It’s ideal for small and medium-sized organizations managing critical assets, particularly in industries like manufacturing, energy, and mobility.
Pros
- You can attach any type of file to maintenance records, easily update maintenance lists, and track open or completed work with a single click.
- The intuitive application is user-friendly, making it easy for new users to adopt. Regular updates incorporate user feedback, improving the system continuously.
- Provides a clear asset performance overview, simple documentation, and traceability of service requests, along with digital processing of orders.
Cons
- Lacks the ability to create different signatures or standard answers for standard processes, such as sending offers or acknowledging receipt.
- Limited options are available for evaluating Key Performance Indicators (KPIs), including costs for service calls, response times, spare parts sent, and their value.
Reviews
"User-friendly, easy to use all information in one system. Great customer support" - Christian
Pricing
Pricing is customized based on your business case or cost-benefit calculation for services, installation, maintenance, and repair processes. You can request a custom quote according to your requirements.
#6 Asset Panda
Best for: Customizable Asset Tracking
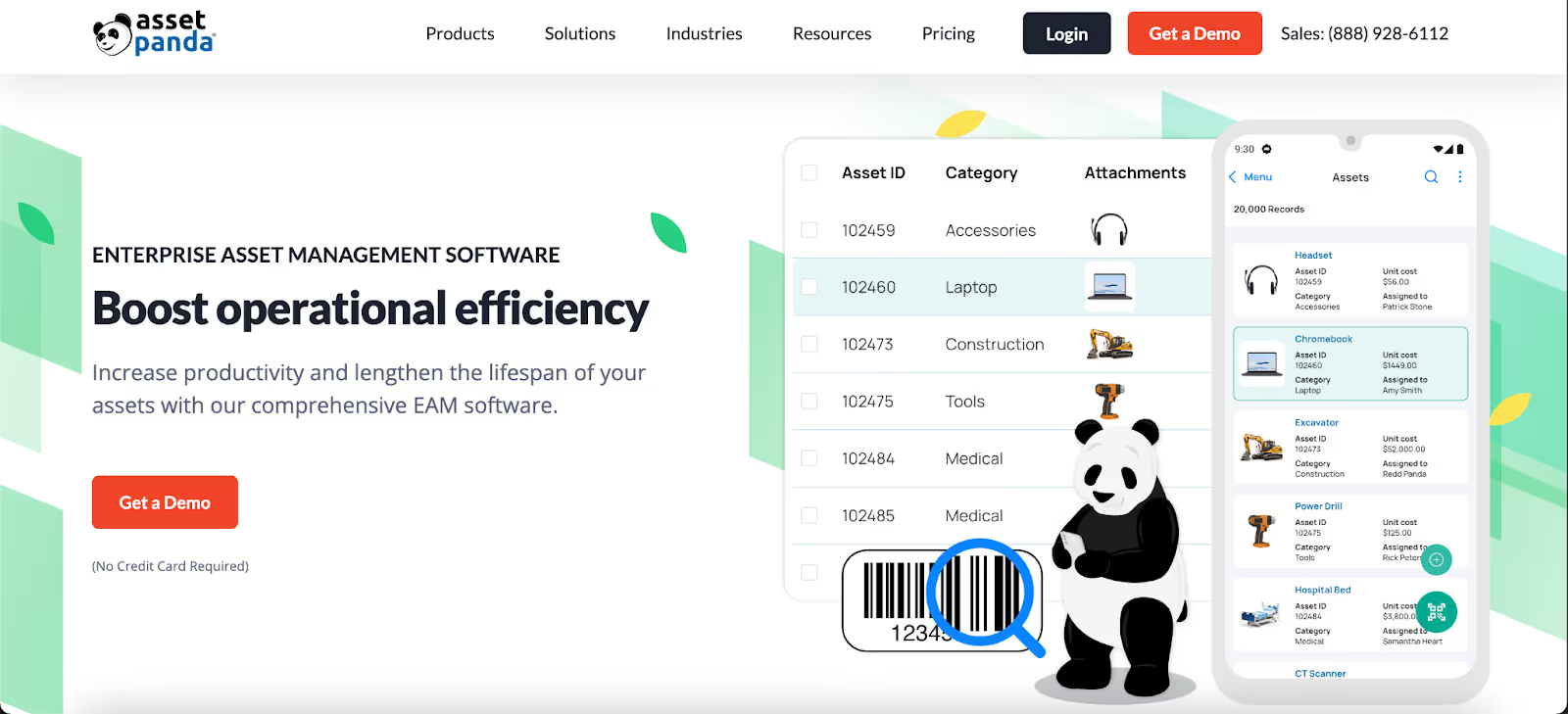
How it Works
Asset Panda is a cloud-based asset relationship management platform specializing in tracking. Whether you're tracking contracts or construction materials, the software adapts to your unique systems and conventions.
Pros
- Detailed reporting and interactive dashboards help you measure the entire lifecycle of your assets and optimize their usage.
- Great customization options allow you to adjust almost everything to fit your needs.
- The mobile app enables barcode scanning, asset searching, and updates on the go, creating flexibility for users.
Cons
- There is no direct option to download or export asset data. It can be done only through generating reports (PDF, CSV) sent via email which can be a hindrance.
- Lacks offline usability, which is a drawback for areas without cell or Wi-Fi signals.
Reviews
"Overall I do enjoy using Asset Panda. It has been a great help with organizing our assets."- Cherrelle
Pricing
Asset Panda offers custom pricing and a free 14-day trial.
#7 Fracttal
Best for: Remote Maintenance Processes
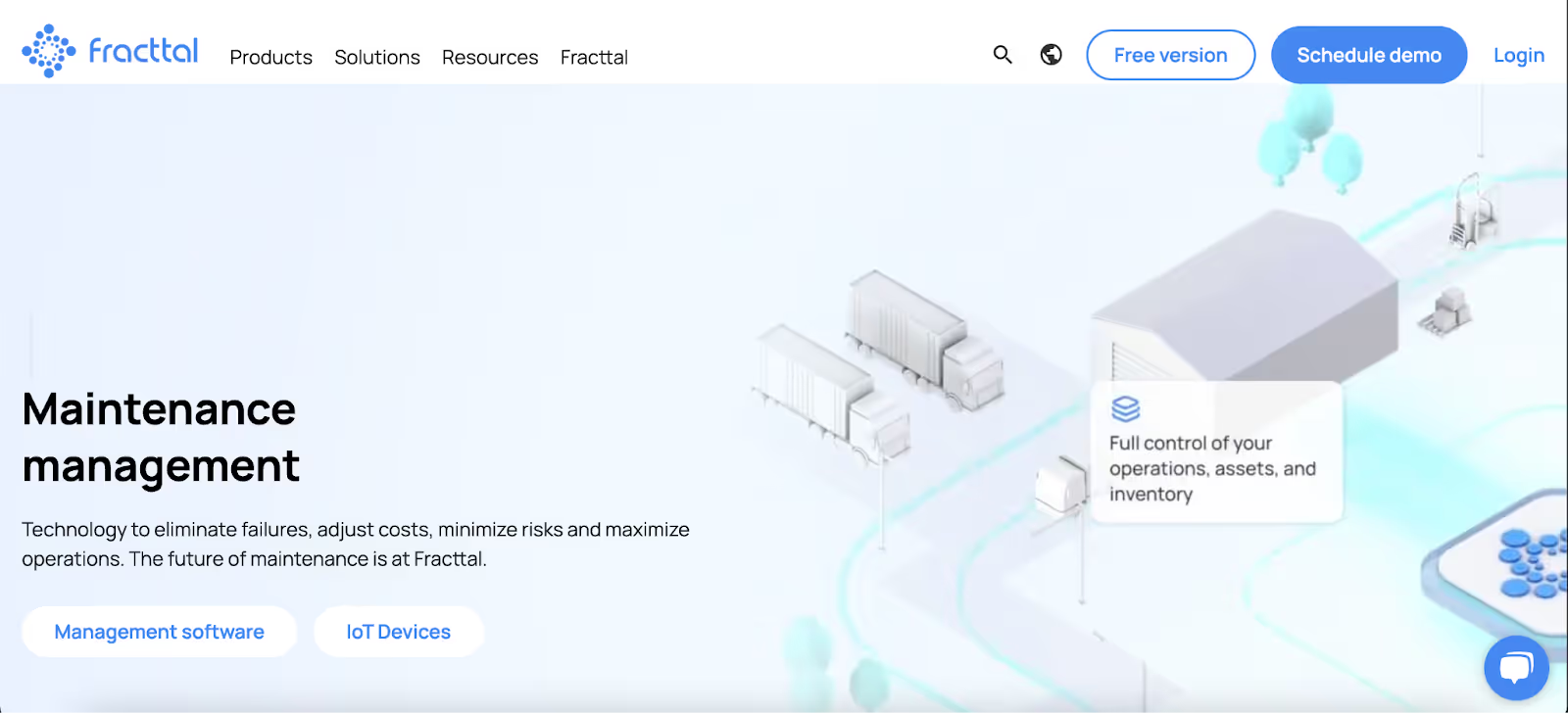
How it Works
Fracttal is a cloud-based CMMS software designed for businesses across various industrial sectors, including manufacturing, services, facility management, and energy. It provides features to plan and execute maintenance for different equipment and manage suppliers, human resources, spare parts, maintenance costs, and budgets.
Pros
- The application can be used on multiple platforms which provides mobility for work teams.
- Fracttal offers good asset management capabilities that allow you to compile, simplify, and easily present maintenance records directly from technicians.
- Numerous filters and custom fields support tailored configurations to suit specific business areas.
Cons
- Some users find the interface non-intuitive, with a less functional menu and small, non-representative icons.
- The number of native KPIs in the BI module could be improved, as some users express the need for natively integrated APIs.
Reviews
"It solved a very important issue for us.. which is keeping track of all tasks. Fracttal allows you to keep track of everything" - Deigo M.
Pricing
Fracttal pricing starts at $255.00 per month. It offers various pricing models and a free trial, allowing users to determine compatibility with the software.
#8 FMX
Best for: Facilities Management Integration
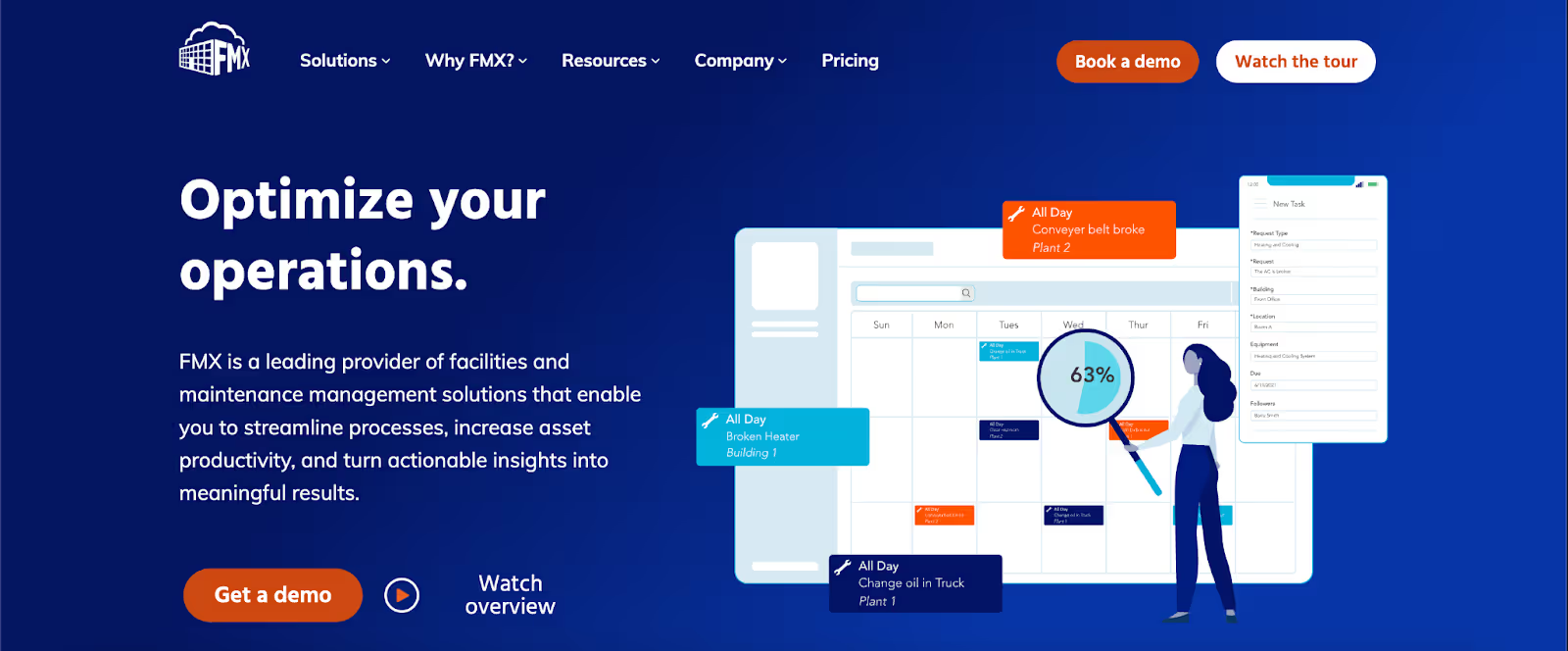
How it Works
FMX offers configurable maintenance and facilities management software that can help you maximize productivity, cut operating costs, and gain actionable insights about your equipment. The software reduces work order resolution time, organizes preventive maintenance tasks, and allows you to manage equipment and assets in one easy-to-use system.
Pros
- The solution is accessible from any web browser, including mobile devices, and supports unlimited requesting users at no additional cost.
- It is easy to set up and use without much training, with excellent customer support.
- The detailed reports provide valuable information for business decisions, such as workload, lifecycle maintenance, cost per repair, and identifying top problem equipment.
Cons
- Users express a desire for better interaction with asset management, specifically the ability to print maps with attached assets.
- The site can glitch, causing ticket information to disappear when submitted, which is frustrating for users handling multiple tickets at once.
Reviews
"We mainly use FMX as a facilities maintenance request and project request software. Overall, we love the ease of use and the customer service." - Jennifer
Pricing
FMX provides personalized quotes based on the number of users handling maintenance requests and the features most important to your organization. A 14-day free trial is also available.
#9 Hippo CMMS
Best for : Work Order Management
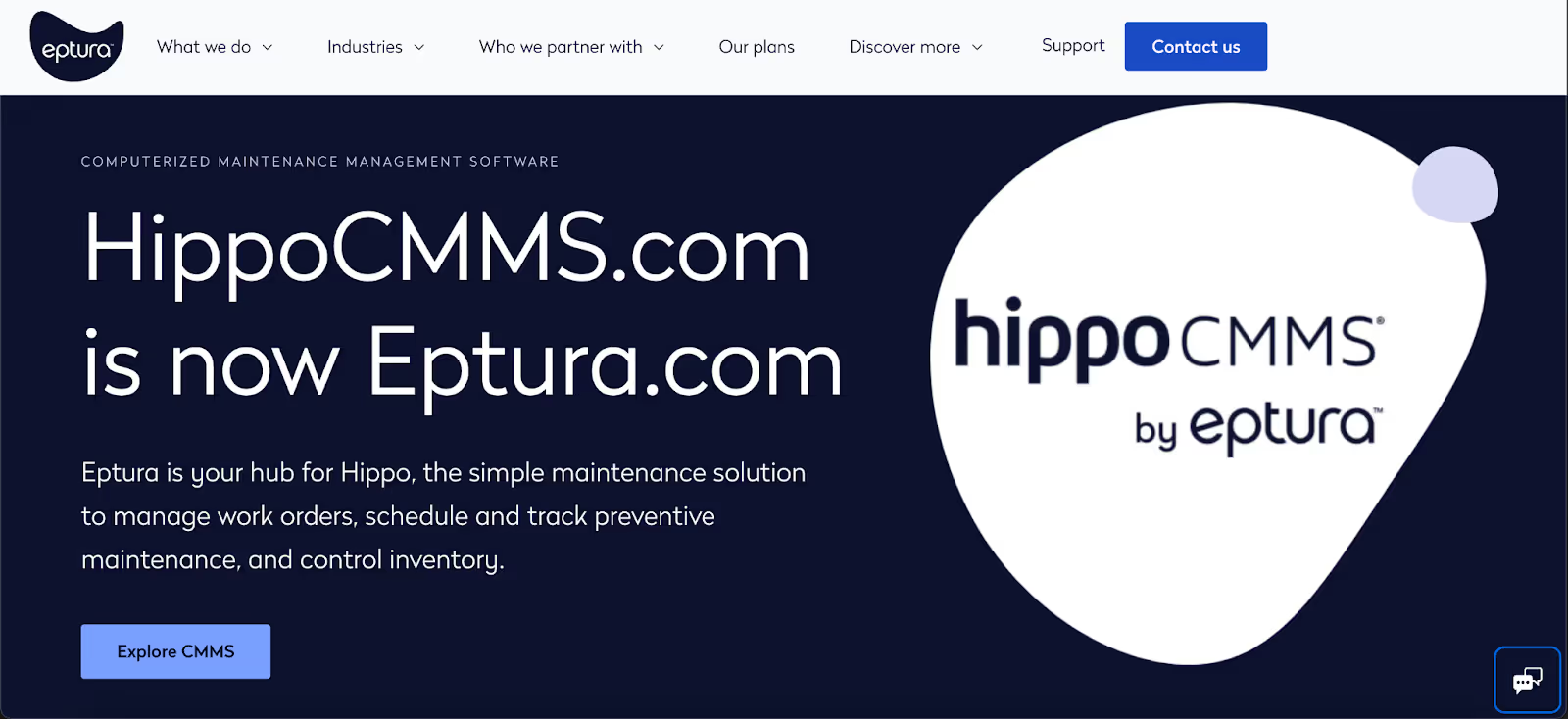
How it Works
Hippo CMMS has been providing maintenance services to a variety of sectors, including manufacturing, healthcare, education, and hospitality. The CMMS software facilitates work order processing, maintenance requests, preventive maintenance management, spare parts tracking, and report generation by employees at all levels.
Pros
- Enables systematic maintenance records for all senior facilities, organizing data and invoices for each department. This makes the entire process smooth and quick, from maintenance requests to vendor payments.
- Easy to use with minimal onboarding or technical knowledge required for requestors. Hippo’s support staff are highly responsive and quick to resolve issues you may face.
- The core of Hippo CMMS is its work order management module, allowing users to review tickets, prioritize, delegate, and track work orders.
Cons
- Users find that Hippo can be buggy. For instance, some ran into difficulty removing unnecessary fields or assigning multiple work order categories to a single device, complicating tracking and data mining.
- Some users have experienced trouble in rescheduling maintenance work dates.
Reviews
"Hippo is an excellent way to simply manage your maintenance program. It is very user-friendly and provides just what you need so you don’t have to pay for features you will never use. It also contains a module for inventory management so you can charge your spare parts to your WOs." - User
Pricing
Hippo CMMS comes in two major plans. Hippo Plus is priced at $55 per user per month, whereas Hippo Pro is $75 per user per month. You can also avail its free trial to get a sense of the system.
#10 AssetTiger
Best for: Cost-Effective Asset Management
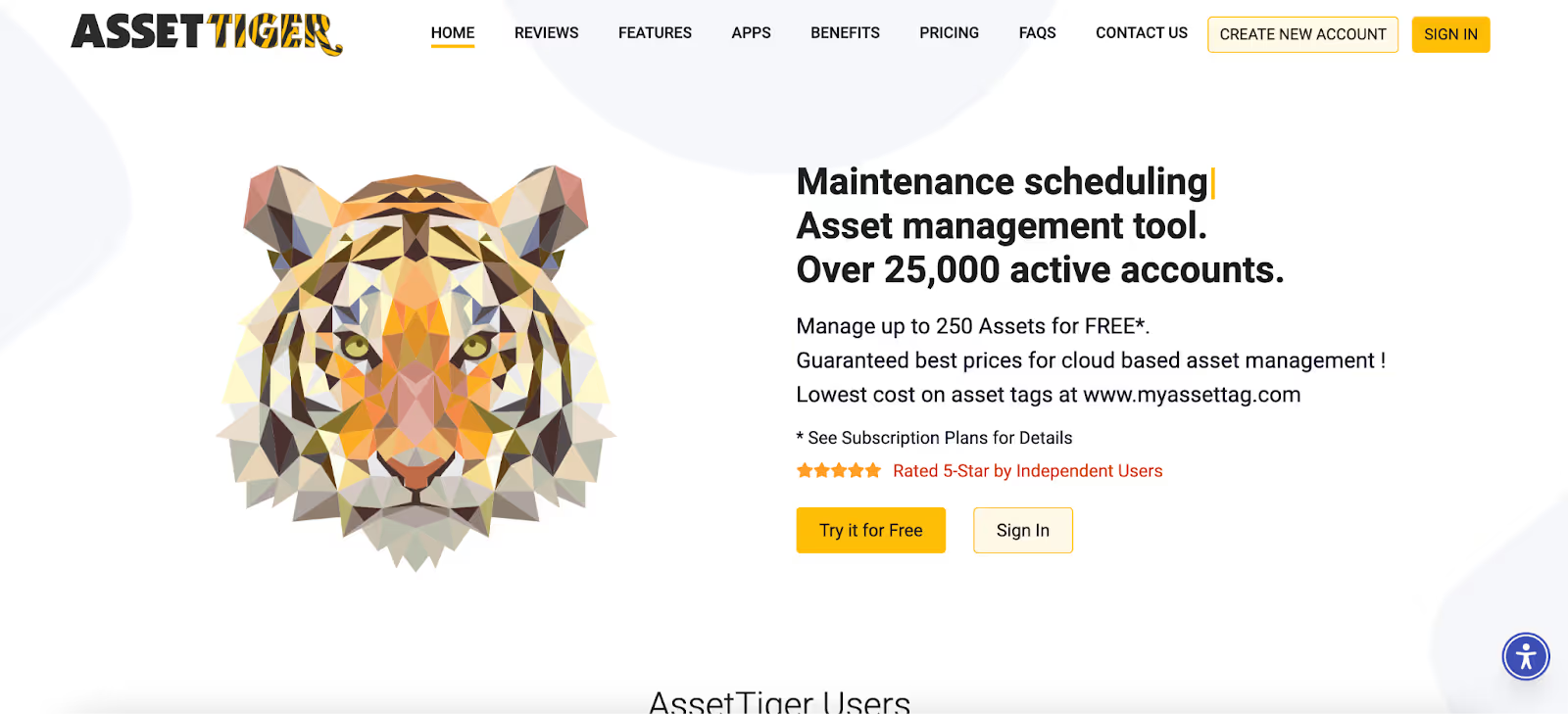
How it Works
AssetTiger is a cloud-based asset management software designed to help businesses streamline maintenance scheduling, barcode scanning, expiration tracking, and more. Managers can set up email alerts, reminders, or alarms to monitor contract due dates, license expirations, and deadlines for specific assets.
Pros
- Offers excellent customer service with timely fulfillment of any queries.
- Useful features like asset cloning allow you to stock up on large numbers of the same assets. Attaching asset photos and related documentation like quotes, purchase orders, and invoices is also very helpful.
- It is easy to add or update inventory from the mobile app, which enhances flexibility and convenience.
Cons
- Some users express that they would like to limit search criteria by more than one field at a time, beyond the standard site/location options.
- The platform signs you out when logging into another session, which can be inconvenient when switching between desktop and mobile platforms.
Reviews
"An awesome asset management tool. So versatile, user-friendly, easy to use, minimal learning curve." - User
Pricing
AssetTiger offers various pricing plans starting from $120.00 per year, with a free trial available.
Other CMMS Software for Manufacturing
11 - Best for Planned Preventive Schedules - Commusoft
12 - Best for Asset Management - Fixx
13 - Best for Material Management- eWorkOrders CMMS
14 - Best for Extending Asset Lifespan - Maintenance Connection
15 - Best for Managing Maintenance on The Go - Azzier
What Features Should You Look for in CMMS Software?
Choosing the right CMMS software involves understanding the key CMMS features that will best support your maintenance operations.
Here are some important features you should consider:
- Preventive Maintenance: A good CMMS software should automate and adhere to preventive maintenance schedules so it extends equipment lifespan and minimizes unexpected downtime. It should perform regular, systematic checks to catch issues before they escalate, keeping your equipment in top condition and reducing the risk of sudden failures.
- Asset Management: The software should maintain a comprehensive view of all asset data, including their condition, history, and performance details. Real-time monitoring and analytics are crucial to help you make informed decisions about maintenance and replacements, so they are replaced at the optimal time.
- Maintenance Analytics and Reports: CMMS software should generate detailed reports to support data-driven strategies for optimal equipment performance. It should analyze downtime incidents and their causes, helping you improve maintenance strategies and reduce future downtime.
- Work Order Management: Look for CMMS software that streamlines the creation, tracking, and completion of work orders. It should utilize tools like calendars, maps, and Kanban boards to manage maintenance schedules and improve operational performance by tracking progress and coordinating tasks.
- Digital Maintenance Forms: A good CMMS software should increase efficiency by replacing paper forms with digital maintenance forms. It should simplify after-sales processes and transform how you manage your machine park or installed base, making data entry and retrieval faster and more reliable.
- Inventory Management: The right CMMS solution should manage spare parts and inventory levels, alerting you when stocks are low. This makes sure that necessary parts are always available, avoiding delays in maintenance and production schedules.
How do I Choose a CMMS Software?
If you are planning to shift to a CMMS solution for the first time, selecting the right one can be tricky. To make the process easier, here's a step-by-step approach to guide you in opting for the best CMMS software for manufacturing:
- Determine Your Essential Features: Focusing on objectives such as increasing asset longevity, reducing costs, and improving operationality allows you to evaluate if the CMMS system aligns with your manufacturing operation goals. Additionally, you should make a note of your organization’s size, asset count, technical support, and maintenance processes as these factors will help in selecting a solution that fits your specific needs, scale, and working model.
- Ensure Preventive Maintenance Support: It's important to choose a CMMS software that supports your preventive maintenance (PM) methods, whether they are calendar-based, meter-based, or runtime-based. The right CMMS system should be able to handle inspections and create corrective maintenance work orders. This support can help you maintain equipment performance and prevent unexpected equipment downtime.
- Check for Integration Capabilities: Integration with existing systems like ERP or CRM is crucial for smooth workflows. This capability allows for easy data exchange and operational continuity. For instance, seek integrational compatibility with your accounting system so you can manage purchase orders, improving your financial tracking and budget management.
- Avail Demos and Trials Where Offered: Scheduling demos allow you to see the software in action and understand its functionalities better. This step is important because it provides a firsthand experience of the software’s user interface and ease of use. It’s advisable to demo at least two CMMS solutions to compare features and usability before selecting CMMS software.
If you would like to explore Makula and how it can help your organization, schedule a demo with us today.
5 Benefits of CMMS Software for Manufacturing
Maintaining manufacturing equipment is pivotal if you want to avoid costly and sudden breakdowns. CMMS solutions can help you transition from reactive to proactive maintenance, offering greater control and preventing equipment failures.
The top five benefits of CMMS software for manufacturing are:
- Proper Maintenance of Equipment: CMMS software keeps track of your manufacturing equipment by scheduling preventive maintenance, ensuring machinery remains in optimal condition. With quick access to equipment history, warranty information, and spare parts inventory, it reduces downtime and repair time, so that your manufacturing and maintenance operation runs smoothly even during breakdowns.
- Tackling Sudden Asset Breakdown: If you fear that sudden equipment failure can disrupt production and increase your maintenance costs, CMMS software can minimize the chance. By allowing you to schedule and plan maintenance, CMMS software helps keep track of all assets, preventing unexpected breakdowns and maintaining operational efficiency.
- Improved Labor Productivity: CMMS provides maintenance technicians with easy access to necessary data, such as spare parts and step-by-step repair procedures. This organized information enables technicians to perform their tasks properly, thereby improving overall labor productivity.
- Informed Maintenance Decisions: By collecting maintenance statistics, CMMS software helps you track key performance indicators (KPIs). As a maintenance manager, you can use this data to report to upper management, identify problems, and make informed decisions about staffing, equipment, and inventory.
- Easy Tracking of Work Orders: CMMS software allows you to track, organize, assign, prioritize, and review work orders. Technicians, operators, engineers, and other stakeholders can access real-time data, update job statuses, and submit repair requests via a centralized system.
Why Makula Is the Best CMMS in 2025
Makula CMMS is more than just maintenance software—it’s a connected maintenance intelligence platform designed for modern factories. Unlike traditional systems that simply manage work orders, Makula’s CMMS unites predictive insights, visual documentation, and asset intelligence in one modular suite.
- The AI Machinery Assistant powers predictive maintenance with real-time diagnostics and anomaly detection
- 3D Stream transforms how technicians access parts data, offering immersive 3D visualisation of machinery
- The Asset Hub ensures complete equipment visibility, tracking service history, manuals, and components from one source
- A dedicated Customer Portal enables seamless collaboration between OEMs, factories, and service teams
- All modules are powered by Industrial AI, enabling faster, data-driven decisions across the maintenance lifecycle
If you're looking to cut downtime, streamline asset care, and future-proof your maintenance strategy, Makula is the CMMS platform built for the job.
FAQs