Optimizing Spare Parts Inventory Management
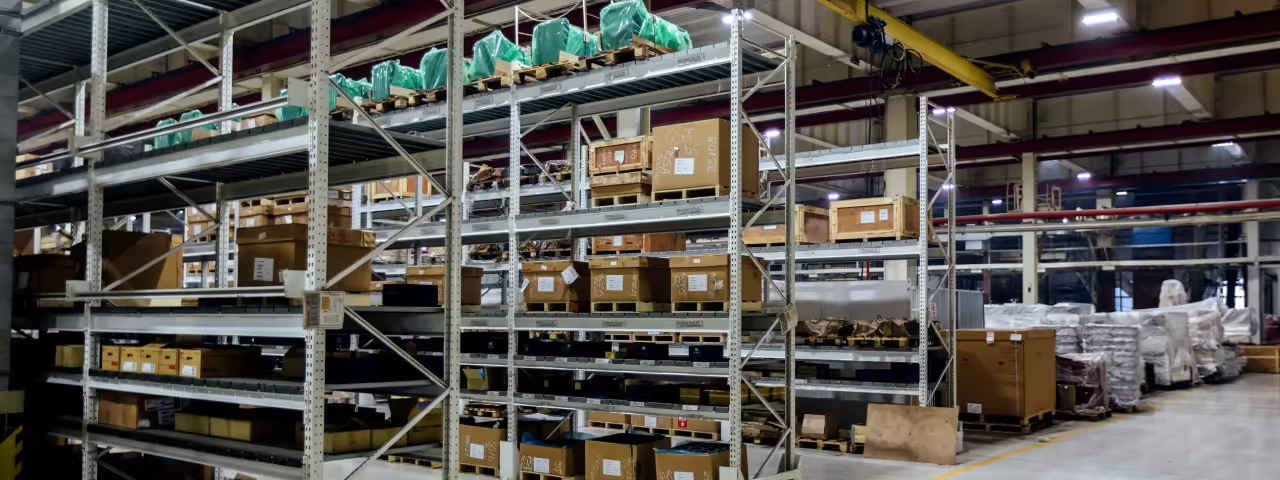
Optimizing Spare Parts Inventory Management
Spare parts inventory management is a delicate balancing act. Too little inventory, and you risk costly downtime when critical equipment fails. Too much, and you're burdened with excessive carrying costs, storage space issues, and the potential for obsolescence.
Here's how to strike the right balance and optimize your spare parts inventory:
1. Categorize Your Inventory:
Not all spare parts are created equal. Implement a categorization system (often called ABC analysis) to classify parts based on their criticality and value:
- Category A (Critical): These are essential parts for high-value assets where downtime is extremely costly. Maintain higher stock levels for these items.
- Category B (Essential): These parts are important but less critical than Category A. Maintain moderate stock levels.
- Category C (General): These are low-cost, readily available parts. Minimal stock levels are sufficient.
2. Demand Forecasting:
- Historical Data: Analyze past usage patterns to identify trends and predict future demand for different spare parts.
- Maintenance Schedules: Use planned maintenance schedules to anticipate upcoming needs for specific parts.
- AI-Powered Tools: Consider implementing AI-powered forecasting tools that can analyze multiple data sources (sensor data, maintenance logs, etc.) to predict demand with greater accuracy.
3. Optimize Stock Levels:
- Reorder Points: Establish reorder points for each spare part based on lead times, consumption rates, and desired service levels.
- Safety Stock: Maintain safety stock levels to buffer against unexpected demand or supply chain disruptions.
- Regular Reviews: Conduct regular reviews of your inventory levels to ensure they align with current demand and adjust reorder points as needed.
4. Improve Inventory Control:
- Centralized System: Implement a centralized inventory management system (often integrated with your CMMS) to track stock levels, locations, and movements of spare parts across your facility.
- Barcode or RFID Tracking: Utilize barcode or RFID technology to improve accuracy and efficiency in tracking spare parts.
- Regular Audits: Conduct regular physical inventory audits to verify accuracy and identify any discrepancies.
5. Supplier Collaboration:
- Strategic Partnerships: Build strong relationships with key suppliers to ensure reliable supply and potentially negotiate favorable pricing or consignment stock arrangements.
- Vendor-Managed Inventory (VMI): Explore VMI arrangements where suppliers take responsibility for managing inventory levels of certain parts at your facility.
6. Obsolescence Management:
- Regular Reviews: Periodically review your inventory for obsolete or slow-moving items.
- Disposal Strategies: Develop strategies for disposing of obsolete parts, such as selling them, returning them to the supplier, or recycling them responsibly.
7. Continuous Improvement:
- Key Performance Indicators (KPIs): Track key inventory management KPIs, such as inventory turnover, carrying costs, stockout rates, and order fulfillment times.
- Data Analysis: Analyze inventory data to identify trends, optimize stock levels, and improve overall efficiency.
By implementing these strategies, you can optimize your spare parts inventory, minimize costs, reduce downtime, and ensure the right parts are available when you need them.