What is Conditioned Based Maintanence?
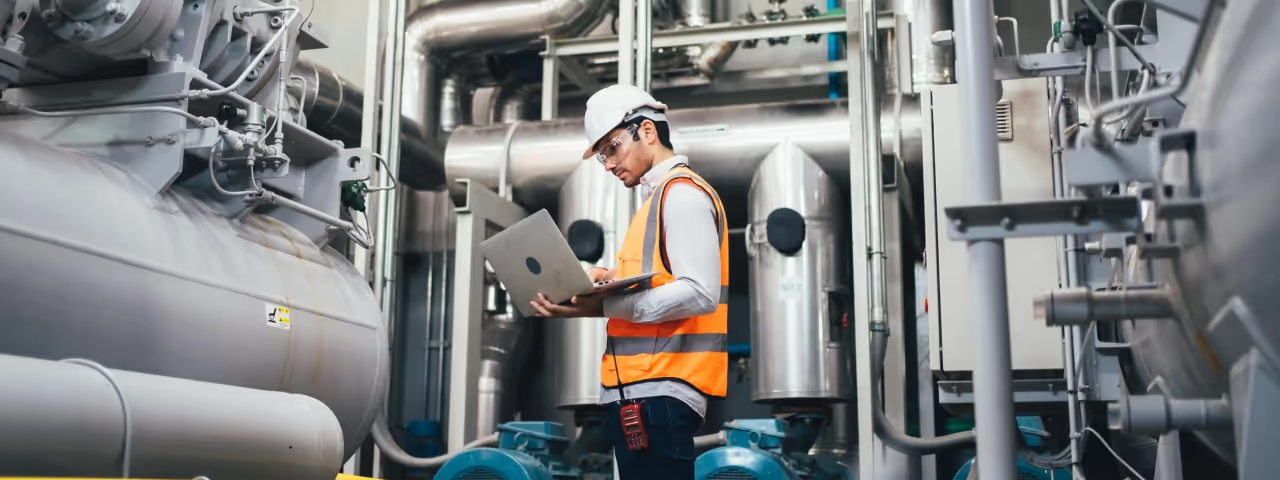
Condition-based monitoring (CBM)
Condition-based monitoring (CBM) is like giving your equipment a regular check-up. It's about using sensors and data analysis to keep a close eye on the real-time health of your machines, so you can spot potential problems before they turn into costly breakdowns. This allows you to move away from traditional, calendar-based maintenance and instead take a more proactive, data-driven approach.
Think of it this way: instead of just servicing your car every few months regardless of its condition, CBM is like having sensors that tell you exactly when something needs attention – maybe your brakes are wearing down, or your oil needs changing. This not only saves you money and hassle but also helps you avoid those unexpected breakdowns that can really throw a wrench in your plans.
How CBM Works
CBM relies on a few key components:
- Sensors: These are the eyes and ears of the system, collecting data on various parameters like vibration, temperature, pressure, and oil levels.
- Data Acquisition: This data is collected and transmitted wirelessly to a central system.
- Data Analysis: Software analyzes the data, looking for trends, anomalies, and patterns that might indicate a developing problem.
- Actionable Insights: The system alerts you when something needs attention, allowing you to take proactive steps to address the issue before it escalates.
Benefits of CBM for OEMs
- Reduced Downtime: Prevent unexpected failures and keep your equipment running smoothly.
- Optimized Maintenance: Perform maintenance only when needed, saving money and extending equipment lifespan.
- Improved Safety: Identify potential safety hazards and take proactive measures to prevent accidents.
- Enhanced Efficiency: Improve resource allocation and optimize maintenance planning.
- Reduced Maintenance Costs: Avoid unnecessary maintenance and extend the life of your equipment.
- Data-Driven Decisions: Gain insights into equipment performance and make informed decisions about maintenance and repairs.
CBM in Action: Real-World Examples
- Manufacturing: Monitor vibration levels in rotating equipment to detect bearing wear and prevent motor failures.
- Oil and Gas: Monitor pipeline pressure and temperature to detect leaks and prevent spills.
- Transportation: Monitor tire pressure and temperature to prevent blowouts and improve fuel efficiency.
- Wind Energy: Monitor turbine blade vibration and temperature to optimize performance and prevent failures.
Choosing a CBM Solution
When selecting a CBM solution, consider factors like:
- Sensor Technology: Choose sensors that are appropriate for your equipment and the parameters you need to monitor.
- Data Analysis Capabilities: Select a solution with powerful data analysis and diagnostic capabilities.
- Integration with Other Systems: Ensure the solution integrates seamlessly with your existing FSM and maintenance management systems.
- Alerting and Notification: Choose a solution with robust alerting and notification features to ensure timely action.
By embracing CBM, OEMs can take a proactive approach to maintenance, improve equipment reliability, and optimize their operations for greater efficiency and profitability.