What is remote diagnostics?
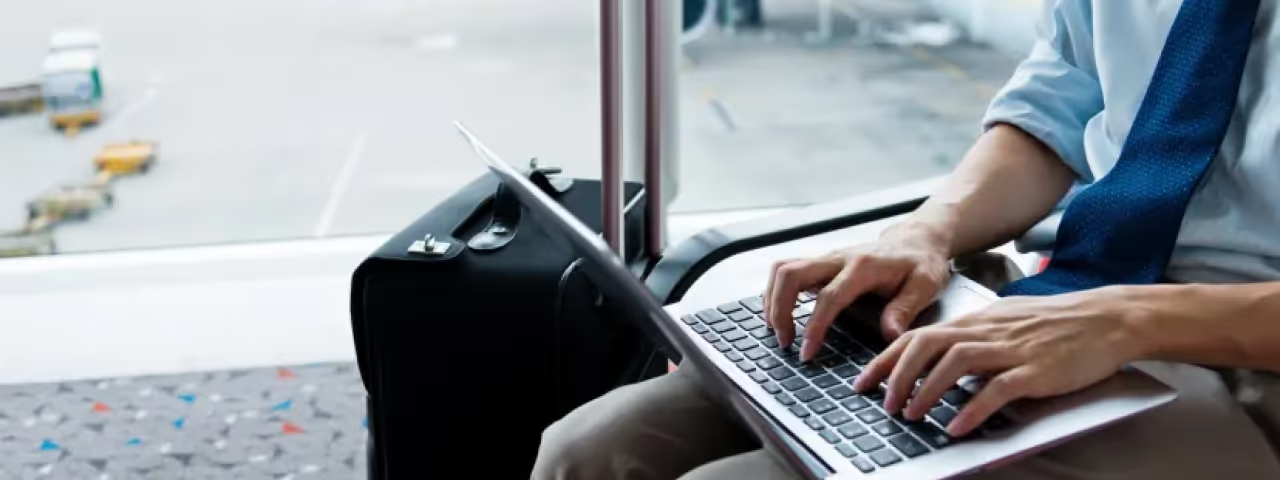
What is remote diagnostics?
Remote diagnostics is like having a virtual technician at your fingertips. It's the ability to diagnose equipment problems from afar, using technology like sensors, data analysis, and remote access tools. This allows you to troubleshoot faster, reduce downtime, and avoid unnecessary on-site visits, saving you time, money, and headaches.
Imagine this: a customer calls with an equipment issue. Instead of immediately dispatching a technician, you can remotely access the machine, analyze its data, and often pinpoint the problem right then and there. You might even be able to guide the customer through a simple fix or adjust settings remotely to resolve the issue. This not only minimizes downtime but also frees up your technicians to focus on more complex tasks.
Key Components of Remote Diagnostics
- Sensors and Data Acquisition: Sensors embedded in equipment collect real-time data on performance, temperature, pressure, and other vital parameters.
- Data Transmission: This data is transmitted wirelessly to a central system where it can be analyzed.
- Data Analysis and Diagnostics: Software analyzes the data to identify anomalies, patterns, and potential issues, often using AI and machine learning algorithms.
- Remote Access: Secure remote access tools allow technicians to connect to the equipment, view its status, and perform diagnostics from anywhere.
Benefits of Remote Diagnostics for OEMs
- Faster Issue Resolution: Quickly diagnose and resolve problems, minimizing downtime and disruption for customers.
- Reduced Costs: Minimize travel expenses, reduce technician time on-site, and optimize resource allocation.
- Improved Efficiency: Streamline service operations, improve technician productivity, and enable proactive maintenance.
- Enhanced Customer Satisfaction: Provide prompt support, minimize disruptions to customer operations, and increase customer satisfaction.
- Improved Safety: Diagnose potential safety hazards remotely, reducing the need for technicians to enter potentially hazardous environments.
- Data-Driven Insights: Gather valuable data on equipment performance, identify trends, and make data-driven decisions to improve product quality and reliability.
Real-World Applications of Remote Diagnostics
Remote diagnostics is transforming various industries, including:
- Manufacturing: Monitor production lines, diagnose machine failures, and optimize maintenance schedules.
- Transportation: Track vehicle performance, diagnose engine problems, and schedule preventative maintenance.
- Energy: Monitor power grids, diagnose equipment failures, and optimize energy distribution.
- Healthcare: Monitor patient vital signs, diagnose medical conditions, and provide remote consultations.
Choosing a Remote Diagnostics Solution
When selecting a remote diagnostics solution, consider factors such as:
- Equipment Compatibility: Ensure the solution is compatible with your equipment and can collect the necessary data.
- Connectivity: Choose a solution with reliable and secure connectivity options.
- Data Analysis Capabilities: Select a solution with powerful data analysis and diagnostic capabilities.
- Integration with Other Systems: Ensure the solution integrates seamlessly with your existing FSM, CRM, and other relevant systems.
- Security: Prioritize solutions with robust security measures to protect sensitive data.
By embracing remote diagnostics, OEMs can transform their service operations, improve customer satisfaction, and gain a competitive edge in today's increasingly connected world.