Poor asset management causes misplaced equipment, excessive administrative work, downtime, and compliance risks. You need real-time asset-tracking tools to access and monitor asset details from a single interface.
A QR code asset management system leverages QR codes to simplify this process. You can access an asset’s profile, manuals, repair status, and spare parts history with a single scan. This helps you keep track of your equipment and reduce downtime.
In this article, we’ll discuss QR code asset management and how it’s a scalable solution for OEMs and factories to reduce downtime.
Understanding QR Codes in Asset Management
QR codes are scannable codes used to store and retrieve asset-related information instantly. Unlike barcodes, which store limited information and require specialised scanners, QR codes can hold extensive asset data and can be scanned using any smartphone or tablet.
QR codes in asset management connect physical assets to a centralised database, streamlining asset tracking, maintenance schedules, and inventory management. It provides real-time access to asset details, improving visibility and organisation beyond basic data storage.
This allows factories to:
- Track asset history: Monitor repair logs, maintenance schedules, and usage records.
- Retrieve real-time data: Access up-to-date information about an asset’s status.
- Automate workflows: Link QR codes to work orders, inspections, and compliance reports (though this depends on the software you’re using and the internal integrations you’ve set up).
- Improve operations: Reduce manual record-keeping errors and streamline asset tracking.
How QR Codes Improve Factory Operations
Here’s how QR codes can improve factory operations:
Reduce Downtime
Unplanned downtime costs Fortune 500 facilities around $129 million annually. QR codes give factories instant access to critical asset data, reducing manual search.
With a single scan, technicians can pull up maintenance records and diagnose issues faster. This prevents costly delays and keeps operations running smoothly.
Simplify Preventive Maintenance
QR codes simplify preventive maintenance by providing real-time access to detailed service information. Technicians can scan a code to view maintenance schedules, service history, and manufacturer recommendations. This helps them complete inspections and upkeep on time.
QR codes also standardise maintenance procedures. They can link to custom checklists and servicing protocols so every technician follows the correct steps. This improves accuracy and keeps maintenance work consistent across teams.
Enable Faster Troubleshooting & Repairs
QR codes help technicians troubleshoot and repair equipment faster by providing real-time access to repair logs and diagnostic guides. Instead of searching through paper manuals or outdated spreadsheets, they can scan a machine’s QR code to view past repairs, common failure points, and recommended fixes.
QR codes can also link to video tutorials or interactive repair steps. This allows less experienced technicians to follow structured troubleshooting without direct supervision, reducing delays and improving repair accuracy.
Digitise Record-Keeping & Compliance
QR codes digitise maintenance logs, inspections, and compliance records, replacing manual paperwork in factories. Scanning a QR code instantly pulls up timestamped records, making it easier to retrieve data for audits, safety inspections, or warranty claims.
QR codes link assets to a centralised system, preventing lost records and reducing data entry errors. They also automate compliance workflows by connecting equipment to inspection checklists, certification records, and renewal reminders.
This helps teams stay on top of regulatory requirements without missing critical steps.
Streamline Spare Parts Orders
QR codes let customers request services and order spare parts from OEMs through a self-service portal.
For example, if you have Makula’s customer portal, your customer can scan the QR code on the equipment. They can request maintenance, check part availability, and place orders instantly.
This speeds up response times and helps customers get the right parts without delays.
Challenges of Implementing QR Code Asset Management in Factories (How to Overcome Them)
Here are some challenges that factories face when implementing QR code asset management and how you can overcome them:
QR Codes Aren’t Durable
QR codes printed on labels or stickers can fade, peel, or get damaged due to heat, moisture, chemicals, and heavy wear.
When a QR code becomes unreadable, technicians lose access to maintenance data, spare part requests, and compliance records. This causes delays and increases downtime.
To overcome this, you can:
- Use a QR code asset tag printer to generate durable QR tags.
- Use etched metal plates instead of stickers for machines in harsh conditions.
- Apply protective laminations or weatherproof coatings to prevent fading and wear.
- Print on high-durability materials like polyester labels built for industrial settings.
QR Codes Risk Unauthorised Access
QR codes are easily scannable, making them vulnerable to unauthorised access. Without security measures, anyone with a smartphone can retrieve asset details, maintenance logs, or ordering links.
When handling high-value equipment, proprietary maintenance data, or restricted spare parts, unprotected QR codes expose sensitive information to unauthorised personnel. This leads to data breaches, tampering, or unauthorised orders.
Here’s how you can overcome this:
- Require login credentials before viewing asset data.
- Set role-based permissions to control user access levels.
- Use encrypted QR links that expire after use.
- Place QR codes in restricted areas instead of public-facing surfaces.
QR Codes Must Integrate with Existing Systems
Many factories use legacy systems that don’t support QR codes, making integration difficult.
If the existing software can’t process QR code data, technicians may resort to manual workarounds. This creates data silos and prevents scanned information from syncing across departments, leading to incomplete or outdated records.
Here’s how you can overcome this:
- Use a computerised maintenance management system (CMMS) like Makula that supports QR codes for asset tracking.
- Link each QR code to a centralised database to keep asset details updated across departments.
- Allow real-time tracking of asset status, location, and usage patterns.
- If you’re an OEM, you can automate work orders by connecting QR codes to a Customer Portal. All you need to do is get access to Makula’s customer portal, and your customers can use the QR code for direct service requests/work orders.
4 Best Practices for Implementing QR Code Asset Management
Here are 4 best practices to implement QR code asset management:
Place in Easy-to-Access Location
Attach QR codes where workers can scan them easily without disrupting operations. Standardising placement across all assets helps teams locate and use them quickly, reducing search time.
Regularly Update QR Code Data
Outdated information leads to maintenance errors and poor asset tracking. Regularly review and update QR code-linked records to maintain accuracy.
Makula automates data logging and tracking to reduce manual input errors. This helps maintain consistency across maintenance logs, inventory, and service history.
Train Your Employees
If workers don’t know how to scan or retrieve asset data, QR codes won’t add value. Train your team on scanning procedures, troubleshooting, and data retrieval to avoid delays and mistakes.
Use a Centralised Asset System
Integrate QR codes with CMMS, ERP, or inventory software for real-time updates.
For example, Makula links each QR code to an asset profile with manuals, service logs, and spare parts data. When your customer scans a QR code via the Customer Portal, they instantly access the asset’s history in a structured format.
How Makula Uses QR Codes for Asset Management
Makula is an AI-powered software that integrates QR codes for asset management. Each asset has a unique QR code that links to documentation, maintenance records, and service histories.
Here’s a look into how QR code asset management works on Makula:
Asset Hub for Data Storage and Collection
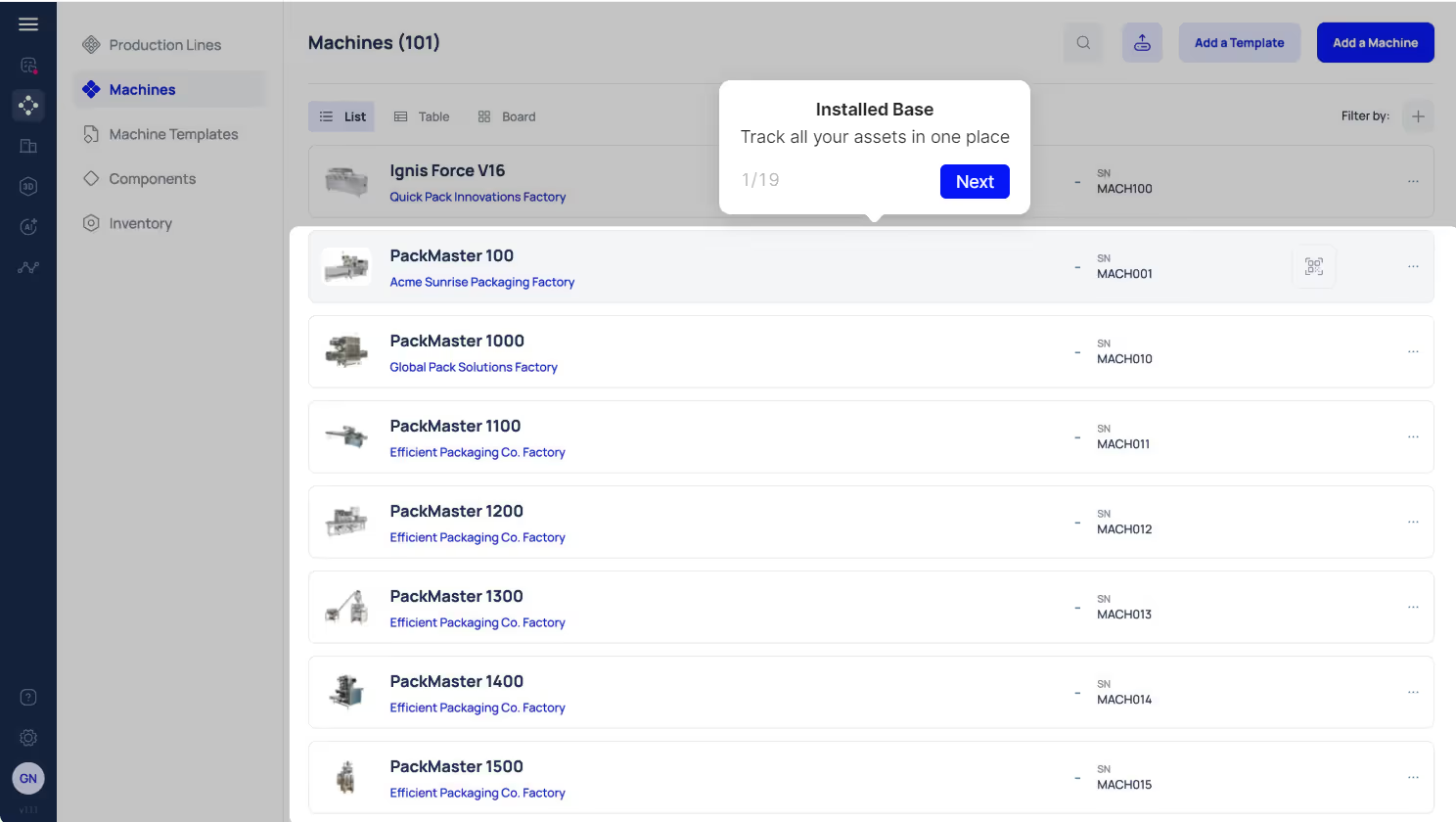
Makula’s Asset Hub acts as a centralised database, making sure that all asset-related information is structured, accessible, and up to date. Instead of dealing with scattered records or manually searching for past service logs, technicians and factories can instantly access asset details by scanning a QR code.
The QR code generator for asset management within Makula allows you to create unique QR codes for each machine, linking them directly to their digital asset profiles. These profiles store maintenance history, repair logs, and technical manuals, making all critical information instantly accessible. This simplifies asset performance tracking and service needs predictions.
With our Asset Hub, you can gain real-time insights into asset conditions and eliminate data silos that slow down operations.
QR Code Integration
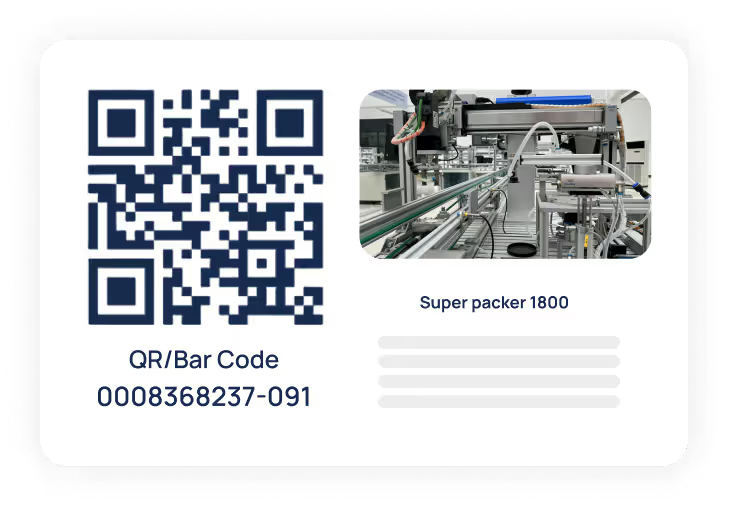
Makula simplifies asset management by linking QR codes to each machine. This allows your factories to retrieve critical information.
By scanning the QR code using a smartphone or tablet, customers can access step-by-step troubleshooting guides, past maintenance records, and technical specifications in a unified system.
This reduces the time spent searching for asset details and ensures that technicians have accurate, real-time information when diagnosing issues or performing maintenance.
Customer Portal for Access
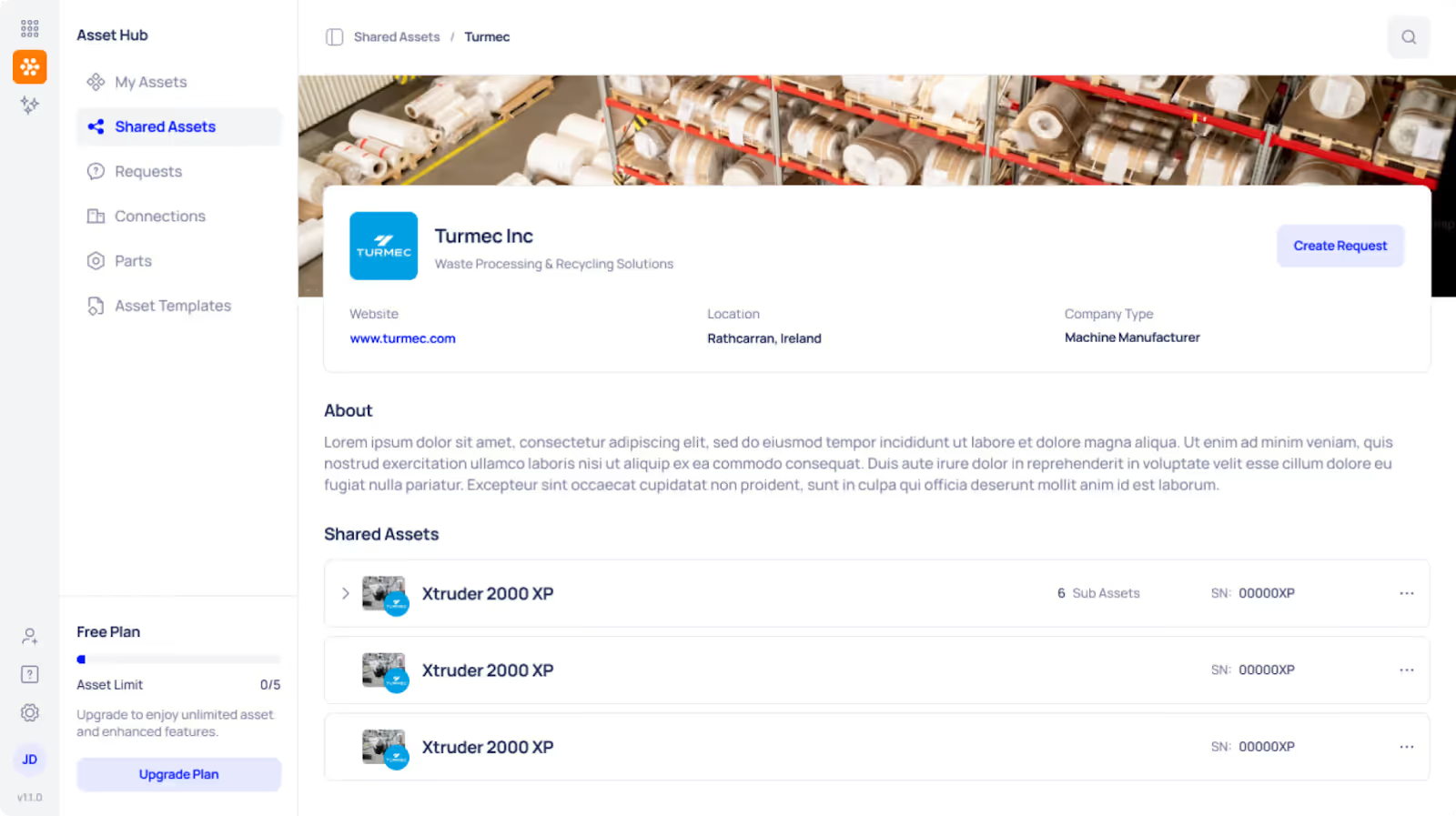
Makula’s Customer Portal is an add-on feature of Asset Hub, essential for QR code asset management. It gives your customers direct access to their assets.
Through a QR code, web browser, or mobile app, customers can:
- View maintenance logs, user manuals, technical documentation, videos, and 3D-CAD drawings.
- Submit work orders for repairs or spare parts directly from the portal.
- Track ongoing service requests and repair status without needing to contact support.
- Manage multiple assets under one account, making it easier for businesses with large inventories.
The portal is fully customisable. You can brand it and tailor it to your specific workflows. This helps you improve after-sales service and reduce support inquiries by allowing self-service access to asset information.
Work Order Ticket for Service & Parts Requests
When paired with the Asset Hub, the Customer Portal allows your customers to create and submit work order tickets via QR codes.
For example, if a machine requires a repair or spare parts replacement, the system automatically logs the request, categorises it by urgency, and forwards it to the support team for immediate processing.
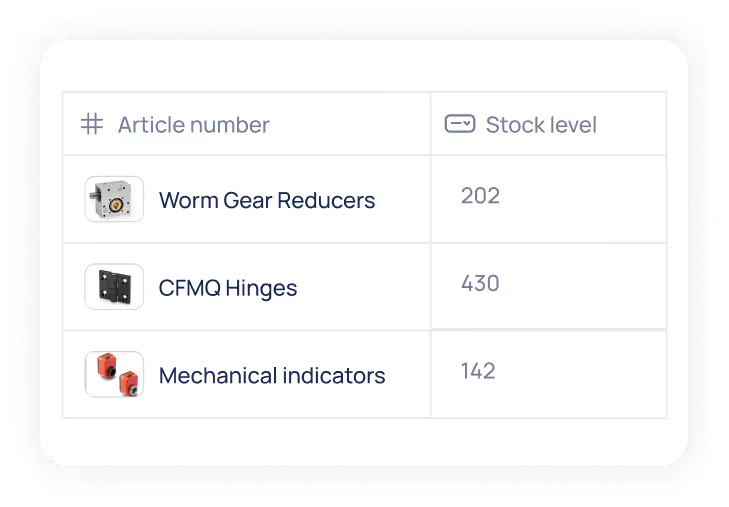
Learn more about how Makula simplifies QR code asset management. Book a free demo with us today.
FAQs
How to use QR codes to track assets?
You can generate unique QR codes for each asset, print them, and attach them to machines. When scanned, the QR code links to the asset’s profile, giving you access to maintenance history, track usage, and submit service requests instantly.
How do QR codes collect data?
A QR code doesn’t collect data, it simply links to a centralized database. That’s why you need a CMMS like Makula to connect QR codes to asset profiles, maintenance records, and service logs, ensuring real-time access and accurate tracking.