As a machine manufacturer, you know that maintenance costs can consume a significant portion of your budget. Studies show that maintenance expenses can range from 15% t o 70% in the manufacturing industry, leading to an average of 800 hours of downtime annually. And when you add unexpected downtime, which 82% of companies experience, the financial strain can become overwhelming.
That's why it's time to start exploring how technology can help. By implementing cutting-edge tools and systems, you can streamline your maintenance processes, minimize downtime, and increase your bottom line. This blog post explores seven effective technology-driven strategies that small to medium-sized machine manufacturers can employ to decrease maintenance expenditures.
7 ways technology reduces maintenance costs
Here are seven innovative ways that technology is transforming maintenance management to be more cost-effective:
1. Predictive Maintenance technologies
Predictive maintenance is a transformative approach in maintenance management, fundamentally shifting strategies from reactive measures to proactive solutions. According to Deloitte research, companies that have adopted predictive maintenance strategies have seen a 40% cut in maintenance costs and a 70% reduction in machine downtime.
Implementation and tools
Predictive maintenance revolves around advanced tools and technology. By placing IoT sensors on important equipment, these sensors continuously track and gather data on critical factors like vibration, temperature, and pressure. AI algorithms then analyze this data in real-time, spotting patterns and irregularities that might indicate a future equipment failure. For instance, consider installing vibration sensors on a motor as part of maintenance management programs. These sensors detect unusual vibrations, indicating issues like misalignment or bearing wear well before the equipment breaks down. Similarly, temperature sensors can warn the maintenance team about overheating problems, helping prevent serious damage that could occur if these issues are not addressed promptly.
Case study
As a prominent tire manufacturer, Michelin embraced digital technology to enhance its operations and customer experience. Michelin improved efficiency and performance by implementing AI-powered data analytics and collaborative robots in its manufacturing processes. These technological advancements allowed the company to accelerate decision-making, optimize manufacturing processes, and reduce risks. Michelin's focus on innovation and technology integration has enabled the company to stay competitive in the age of smart manufacturing.
Impact on maintenance costs and efficiency
The strategic implementation of predictive maintenance directly impacts maintenance costs and operational efficiency. According to a McKinsey report, companies that have adopted predictive maintenance technologies have experienced up to a 30 to 50% reduction in downtime. This significant decrease boosts production and reduces abrupt and often extensive costs associated with unplanned downtime.Moreover, the report indicates that predictive maintenance can decrease maintenance costs by 10% to 40%. This targeted approach prevents over-maintenance, saves on labor, and reduces the use of spare parts.
2. Automated Maintenance scheduling
Automated maintenance scheduling revolutionizes how routine maintenance tasks are planned and executed, significantly boosting operational efficiency and precision. This technology-driven approach employs sophisticated software systems with maintenance management certification to automate the organization of maintenance activities. Below are some tasks that can be automated:
Inspections
Regular inspections are vital for ensuring the continuous operational integrity of complex machinery. These inspections can be meticulously scheduled through automation based on specific intervals or operational thresholds. For instance, sensors might trigger an inspection task in the system after machinery has operated for several hours, ensuring timely checks without manual tracking.
Cleaning
Maintaining machinery in pristine condition is essential for its performance and longevity. Automated scheduling can tailor cleaning tasks based on usage patterns or specific environmental conditions. In scenarios where equipment is exposed to high levels of particulates, the system might schedule more frequent cleanings to prevent build-up that could impair functionality.
Basic repairs
Efficiently managing everyday wear and tear prevents minor issues from escalating into major problems. Automated systems can generate work orders and proactively schedule repairs based on data from equipment sensors. This timely intervention keeps machinery in peak condition and reduces the risk of unexpected downtime.
3. Integrating CMMS systems
For small to medium-sized manufacturers, controlling maintenance costs while ensuring operational efficiency is a critical challenge. Computerized Maintenance Management Systems (CMMS) are crucial in overcoming this challenge. Below are some important points to consider in this regard:
Centralization of Maintenance Data
A digital maintenance management system centralizes all maintenance-related data, a fundamental shift from traditional, fragmented information systems that can lead to inefficiencies and increased costs. This centralization provides a comprehensive view of all maintenance activities, providing critical insights into asset utilization, maintenance schedules, and historical performance. A unified system eliminates discrepancies and duplication in maintenance records, ensuring data is consistent and easily accessible.
Enhanced decision-making
CMMS enhances decision-making by providing detailed analytics on asset performance facilities maintenance management.These insights enable maintenance managers to optimize the timing and scope of maintenance work, prioritize tasks based on criticality, and allocate resources more effectively. Additionally, the predictive analytics capabilities of many modern maintenance management programs can forecast potential equipment failures before they occur, allowing for preemptive action that minimizes downtime and operational disruptions.
Optimizing maintenance schedules
By integrating a CMMS, manufacturers can move from a reactive maintenance model to a proactive one. The system schedules maintenance tasks based on actual equipment conditions rather than predetermined intervals. This approach, known as condition-based maintenance, ensures that maintenance is performed only when necessary, thereby reducing unnecessary maintenance activities and extending the machinery's lifespan.
Improving Inventory Management
Inventory management is among the top advantages of maintenance management. The system precisely tracks spare parts and consumables, reducing the capital tied up in inventory. It ensures that the right parts are available at the right time, crucial for maintaining a smooth operational flow and avoiding costly last-minute purchases or expedited shipping costs.
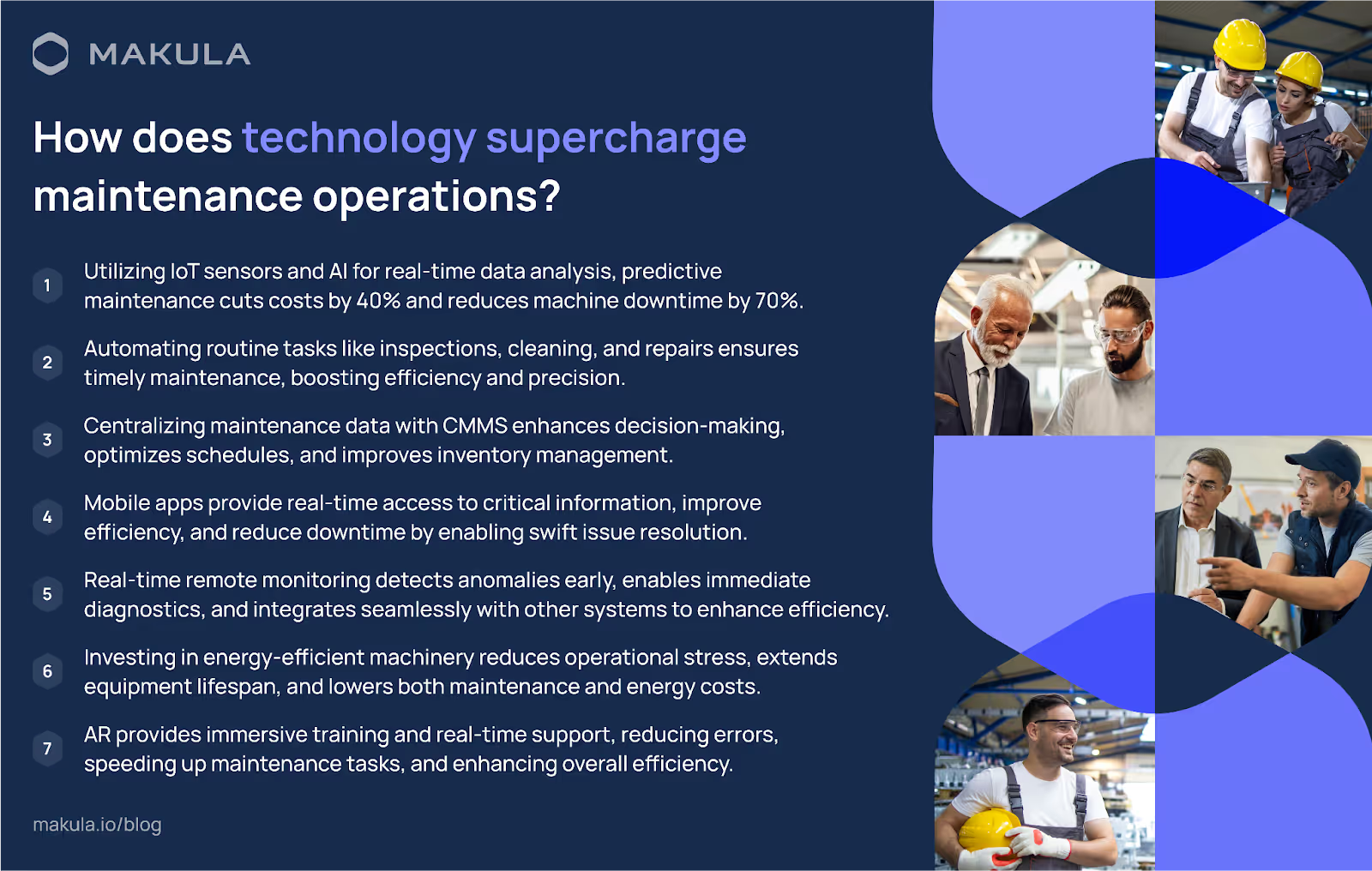
4. Use of mobile maintenance applications
Mobile maintenance applications are essential for manufacturers aiming to optimize maintenance operations and reduce costs. Here is how:
Real-time access to critical information
Mobile maintenance applications enable technicians to access real-time maintenance schedules, detailed equipment manuals, and inventory levels, anywhere on the factory floor. This instant access allows for quick diagnosis and decision-making directly at the point of issue, reducing the need to return to a central workstation or sift through paper manuals. Technicians can swiftly consult historical data, review maintenance procedures, and check parts availability, facilitating faster and more accurate troubleshooting.
Improved efficiency and reduced downtime
Mobile applications help minimize downtime by significantly cutting down response times to equipment issues, a critical factor in maintaining productivity in manufacturing environments. The streamlined communication and reporting capabilities allow maintenance issues to be addressed promptly before they escalate into costlier problems, ensuring that machinery operates at peak efficiency with minimal interruptions.
Enhanced team communication
These applications foster improved communication and collaboration within maintenance teams and across departments. Features like instant messaging, real-time updates on task status, and alerts about equipment conditions keep everyone informed and coordinated. This enhanced communication aids in effective maintenance planning and execution, preventing overlaps and ensuring efficient resource use.
5. Remote monitoring systems
Remote monitoring and diagnostics technology enables businesses to oversee their operations continuously and intervene promptly when issues arise, minimizing downtime and reducing maintenance costs.The capability to monitor equipment remotely and in real-time revolutionizes how maintenance is approached in several ways:
Early detection of anomalies
Remote monitoring systems analyze the data sent by IoT sensors to identify deviations from normal operating conditions. By detecting these anomalies early, maintenance teams can diagnose potential issues before they escalate into serious problems.
Immediate diagnostics
When a sensor detects an anomaly, the system can automatically run diagnostics to determine the likely cause of the problem. This immediate response is critical for addressing issues quickly and efficiently, reducing the need for on-site diagnostics checks and saving valuable time.
Scalability and integration
Modern remote monitoring solutions are highly scalable and can be integrated with existing enterprise resource planning (ERP) systems and other industrial automation tools. This integration allows for seamless data flow across various parts of the organization, enhancing overall operational efficiency and reducing costs.
Safety improvements
By monitoring equipment remotely, technicians are not required to inspect machines in potentially hazardous environments physically. This significantly reduces the risk of accidents and injuries associated with maintenance tasks.
6. Energy-efficient technologies
Investing in energy-efficient machinery is a strategic decision that benefits small to medium-sized manufacturers in multiple ways, particularly in reducing operational and maintenance costs. Energy-efficient machines are designed to use less power and operate more efficiently, which brings several significant advantages:
Smooth operation
Energy-efficient machines are often built with the latest technologies that ensure smoother operations. They tend to have better control systems and optimized performance parameters, minimizing mechanical stress during operation. This smooth functioning reduces wear and tear, leading to fewer mechanical breakdowns and maintenance issues.
Reduced maintenance needs
Machines that operate efficiently under less strain generally require less maintenance. Because energy-efficient equipment uses energy more judiciously, it doesn't overwork itself, which means components last longer and maintenance intervals can be extended. This saves on the direct costs associated with repairs and replacements and reduces the downtime that can interrupt production schedules.
Extended equipment lifespan
The cumulative effect of reduced wear and tear and lower operational stress is a longer operational lifespan for the machinery. This extended lifespan means manufacturers can defer the capital expenditures of replacing equipment, providing significant long-term financial benefits.
Operational cost savings
Beyond the savings on maintenance, energy-efficient machinery also costs less to operate. These machines consume less power, leading to lower energy bills. These savings can be substantial over time in industries where energy consumption is a major operational cost, such as packing and processing.
7. Training and support through augmented reality (AR)
Industry sectors with complex machinery, such as manufacturing and packaging, require skilled maintenance. Augmented Reality (AR) offers a compelling solution by transforming how training and support are conducted, reducing maintenance costs significantly.
Augmented reality in training
Traditional training methods often require physical access to equipment and can disrupt production schedules. AR changes this dynamic by superimposing digital information—like operational procedures and safety protocols—directly onto the equipment through AR glasses or mobile devices. This immersive approach speeds learning and enables hands-on practice without halting machine operation.
Real-time support and maintenance guidance
AR truly shines in providing maintenance personnel with real-time, on-the-spot support. With AR devices, workers can receive step-by-step instructions and essential information overlaid directly onto the equipment they are servicing. This instant access to crucial data helps minimize errors, accelerate maintenance tasks, and is invaluable during unplanned breakdowns.
Reducing costs and enhancing efficiency
AR significantly reduces labor costs and machine downtime by streamlining training and speeding up maintenance activities. More accurate maintenance work ensures more durable repairs and better equipment maintenance, prolonging the machinery's operational lifespan and decreasing the frequency of costly fixes.
Scalability and continuous learning
AR technology can be scaled across various organizational levels and updated with new information as machinery evolves or new systems are implemented. This flexibility facilitates ongoing learning and skill development, ensuring staff remains well-informed and proficient.
Empower your maintenance strategy with Makula
Staying ahead in today's competitive market requires embracing innovative solutions. These methods have shown significant potential in cutting costs and enhancing efficiency, from predictive maintenance to advanced training technologies.However, to truly harness the power of these technological advancements, it is crucial to partner with a reliable and forward-thinking company that can help you with maintenance management analysis.
Makula is at the forefront of maintenance technology, offering state-of-the-art solutions tailored to your business's unique needs. Whether you're looking to implement IoT-based predictive maintenance, streamline your maintenance schedules with automation, or upgrade to energy-efficient systems, Makula has the expertise and technology to make it happen.
Contact us today to see how we can help you reduce maintenance costs and improve efficiency.