A recent survey identified the top three obstacles to adapting strategy for Industry 4.0 (move towards digitalization) as a lack of vision, too many technological options, and organizational silos (Deloitte, 2019). In industrial settings, digital asset management is important for ensuring machinery and equipment run at peak performance.
This practice extends the lifespan of assets prevents costly downtimes, and ensures safety standards are met. By prioritizing strategic maintenance, facilities can avoid unexpected breakdowns, maintain steady production levels, and protect their bottom line.
Key Performance Indicators (KPIs) are key in measuring the success of maintenance efforts. These include equipment uptime, which tracks how often machinery is operational, and maintenance costs which monitor spending on repairs and upkeep.
Similarly, these include asset reliability assessing how dependable equipment performs, and overall operational efficiency which evaluates how well resources are utilized. Together, these maintenance KPIs provide a comprehensive view of the health and efficiency of machinery maintenance operations, guiding decisions that impact the entire organization.
Understanding Digital Asset Management and KPIs
Digital asset management involves the processes and strategies used to keep your company's equipment and assets running smoothly and efficiently. The main goals of maintenance management are to reduce equipment downtime, ensure safety, and prolong the life of assets, all while keeping costs manageable. This process includes several types of maintenance: preventive, predictive, and corrective.
Key Performance Indicators (KPIs) are important measurements used to check how well your maintenance strategies are working. Keeping track of these KPIs helps you understand the impact of your maintenance efforts and guides you in making improvements to increase efficiency and reduce costs in your operations.
KPI # 1 - Improving equipment uptime
The average cost per hour of downtime is $260,000 (Aberdeen Group, 2019). In improving equipment uptime, the goal is to reduce the frequency and duration of equipment downtime, which can be costly and disruptive. By enhancing equipment uptime, you ensure that your operations run more smoothly and efficiently, contributing to better productivity and profitability.
Preventive Maintenance scheduling
In order to manage preventative maintenance and minimize downtime, 94% of businesses view maintenance, repairs, and operations (MRO) as either extremely or fairly vital (Peerless Research Group, 2018). Establishing a routine preventive maintenance schedule is crucial in preventing equipment failures before they occur. The key metric here is Preventive Maintenance Compliance (PMC), which measures how well your maintenance team adheres to the preventive maintenance schedule. A high PMC score indicates that maintenance tasks are completed on time, which contributes to overall equipment reliability and uptime.
Real-Time monitoring systems
IoT and other real-time monitoring technologies provide continuous surveillance of equipment performance, alerting maintenance teams to any anomalies before they cause downtime. Maintenance KPIs such as Downtime Reduction and Equipment Health Monitoring help you gauge the effectiveness of these systems. By staying informed about the real-time status of your machinery management, you can preemptively address issues, and maintain a steady flow of operations.
Rapid response and repair protocols
Utilizing machinery management that features alert and notification systems can improve your maintenance response times. These systems ensure that when issues are detected, maintenance teams are promptly alerted, enabling quicker repairs. The key metric here is the Mean Time to Repair (MTTR), which measures the average time it takes to repair a piece of equipment after a failure occurs (IBM, n.d.). Reducing MTTR is essential for enhancing equipment uptime, as it minimizes the impact of breakdowns on production.
KPI 2 - Reducing maintenance costs
93% of businesses believe their maintenance procedures are inefficient (CXP Group, 2018). Reducing maintenance costs is a critical performance indicator that focuses on lowering the expenses associated with keeping machinery and equipment in good working order. By effectively managing these costs, you can improve your organization’s profitability and operational efficiency.
Adoption of Predictive Maintenance
By using advanced analytics to predict breakdowns, equipment uptime can be increased by up to 20% (Deloitte, 2017). Predictive maintenance technologies are key to anticipating equipment failures and minimizing unnecessary maintenance actions. By using sensors and data analytics, predictive maintenance allows you to perform maintenance only when it is truly needed, rather than on a fixed schedule. The main metric to track here is the Percentage Reduction in Unplanned Downtime, which helps quantify the effectiveness of predictive maintenance in maintaining continuous operations.
Efficient resource management
Optimizing the use of resources, such as managing your spare parts inventory and allocating labor effectively, is essential in reducing maintenance costs. Proper resource management ensures that you have the right parts and the right people at the right time, without overstocking or understaffing. The metric to watch is Maintenance Cost Per Unit, which provides insight into how much you are spending per unit of production, helping you identify areas for cost reduction and efficiency improvements.
Using machine maintenance software
CMMS, internally developed spreadsheets and schedules, and automated maintenance schedules are the most often used technology in facilities for maintenance monitoring and/or management (Plant Engineering, 2021). These systems automate many aspects of digital asset management, such as issuing work orders, scheduling inspections, and tracking maintenance history. Maintenance KPIs like Automated Work Order Completion Rate and Software Utilization Rate are important to track. They measure how effectively the software is being used and the extent to which it automates maintenance tasks, respectively.
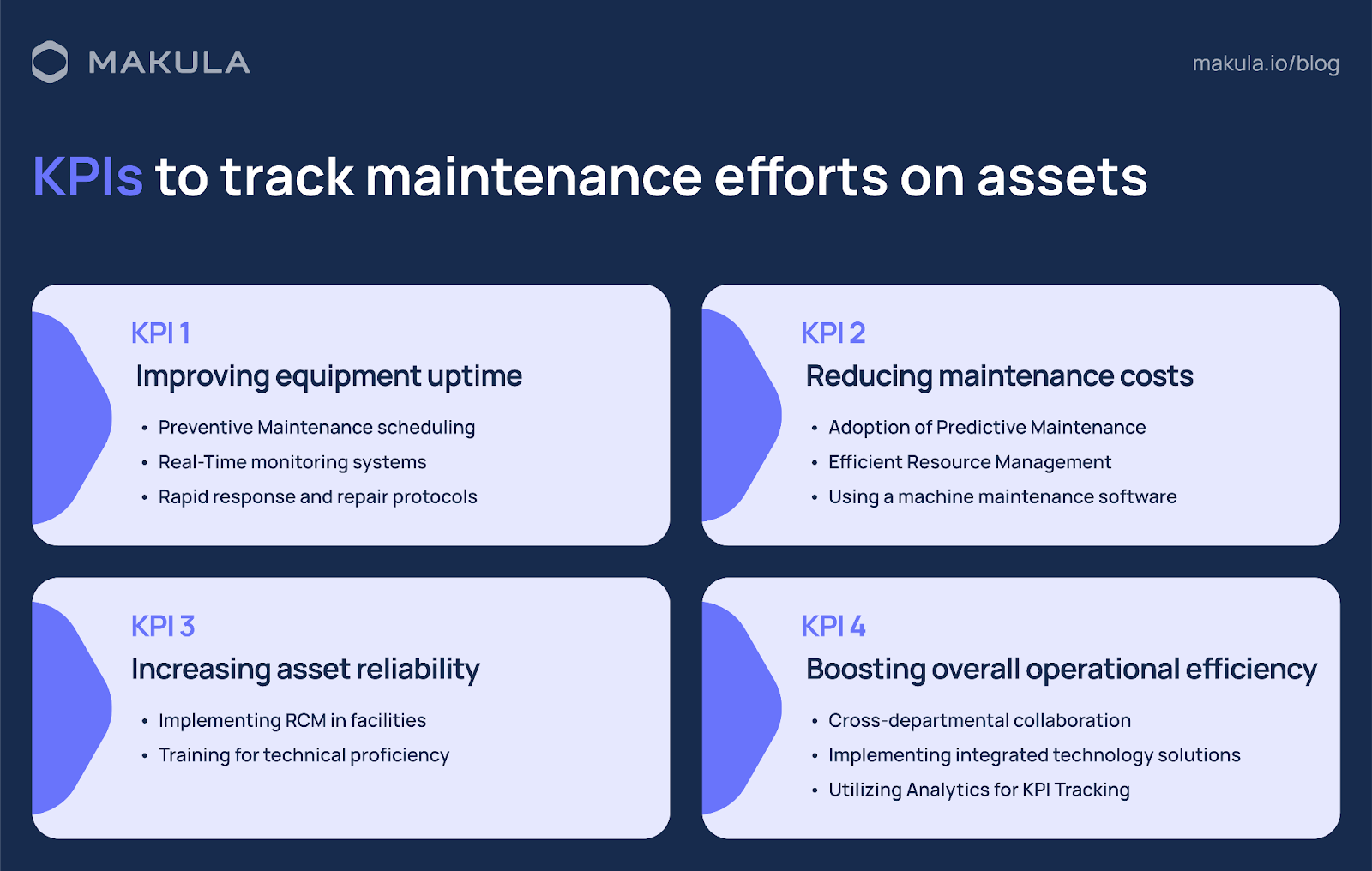
KPI 3 - Increasing Asset reliability
The largest difficulty, according to 39.9% of respondents, is equipment reliability (Add Energy, 2022). Increasing asset reliability is an important performance indicator that focuses on enhancing the dependability and performance of your facilities' equipment. This KPI involves implementing strategies that extend asset life and reduce the frequency of failures, ensuring that your operations remain efficient and uninterrupted.
Implementing RCM in Facilities
Reliability-centered maintenance (RCM) focuses on understanding which equipment functions are critical and devising maintenance strategies based on those priorities. By concentrating on critical systems, you minimize the likelihood of asset failure and ensure that your operations continue smoothly without unexpected interruptions. The key metric to monitor here is the Asset Failure Rate, which helps track the frequency of failures and demonstrates the effectiveness of your RCM approach in reducing these incidents.
Training for technical proficiency
Only 55% of respondents in a McKinsey survey have formal systems for sharing information among technicians, which could hinder skill retention when staff retire or leave. Additionally, 73% find it challenging to hire new maintenance technicians (McKinsey, 2023). Well-trained personnel are more capable of diagnosing and resolving issues efficiently and accurately, which directly impacts the reliability of your assets. By investing in regular and advanced training programs, you ensure that your team's skills remain up-to-date with the latest maintenance technologies and practices. The Training Completion Rate is an important metric here, indicating the percentage of training programs completed by staff, serving as a measure of your commitment to enhancing staff expertise.
KPI 4 - Boosting overall operational efficiency
Roughly 85% of all components are prone to random failure, which indicates that equipment malfunctions happen periodically (Limble, 2023). Boosting overall operational efficiency ensures that every part of your facility works together smoothly, reducing waste and improving output. Strategies to enhance operational efficiency often involve improving communication across departments, integrating technology solutions, and utilizing advanced analytics.
Cross-departmental collaboration
By providing shared access to maintenance data and schedules, machinery management enhances communication, ensuring that everyone is on the same page. The metric to track here is the Communication Efficiency Index, which measures the effectiveness of interdepartmental communications and their impact on maintenance operations. This index helps you understand how well different departments work together and identify areas where communication can be improved to boost efficiency. Enhance team collaboration with Makula's 3D Live Collaboration tool, enabling real-time interaction and problem-solving on 3D models to streamline maintenance processes.
Implementing Integrated Technology Solutions
Digital work management encompasses a wide range of systems that enhance maintenance work leading to cost reductions of 15 to 30 percent (McKinsey, 2021). Digital asset management combines various maintenance tasks into a single, user-friendly platform, making it easier to manage and analyze data. This integration helps reduce errors and inefficiencies, allowing for smoother operations across your facilities. Maintenance KPIs such as the Technology Adoption Rate and System Integration Score are important for assessing how well these technologies are being implemented and how effectively they integrate with existing systems.
Utilizing analytics for KPI tracking
Utilizing the analytics features in digital asset management, enables maintenance managers to develop, monitor, and refine specific performance indicators, aligning maintenance operations with the broader goals of the facility. This approach provides actionable insights that help in making informed decisions. Key Maintenance KPIs to monitor include Overall Equipment Effectiveness (OEE) and Planned Maintenance Percentage (PMP). OEE measures how well your equipment is utilized during planned operating times, while PMP indicates the proportion of maintenance that is planned versus unplanned. Improve your operations with Makula's Maintenance Analytics and Reporting, which simplifies tracking and analyzing key performance indicators to help you make smart, data-driven decisions effortlessly.
Aligning maintenance goals with Facility objectives
When aligning maintenance goals with broader facility objectives, it's essential to integrate strategies that enhance overall performance, competitiveness, and safety. Using machinery management can be a key factor in achieving these alignments:
- Strategic Asset Management: Align maintenance strategies with the entire asset lifecycle to enhance performance and maximize return on investment.
- Maintenance as a competitive advantage: Improve equipment reliability and reduce downtime to elevate product quality and heighten customer satisfaction.
- Enhancing safety protocols with Risk Management Tools: Advance beyond compliance by proactively managing risks to optimize safety protocols and protect facility operations.
- Data-driven decision-making: Utilize robust data analytics for precise maintenance planning, ensuring alignment with your facility's strategic objectives.
- Sustainability and energy efficiency: Implement strategies focused on energy efficiency and sustainability to reduce environmental impact and operational costs.
Effective machinery management is key to improving efficiency, reliability, and cost-effectiveness in your operations. By integrating Makula's advanced maintenance solutions, you can achieve these goals more smoothly and with greater precision.