The global work order management systems market is expected to reach a value of USD 1176.80 million by 2029, with a CAGR of 10.42% by 2029. Key drivers for this growth include the increasing use of handheld devices, the adoption of cloud-based solutions, and the demand for improved field workforce utilization.
Imagine a scenario: a customer's critical production line grinds to a halt due to a machine malfunction. Your service team scrambles, but crucial details are missing. Unclear communication regarding the issue requires parts, or even the specific machine model delays the repair. This disjointed process not only frustrates your customer but also wastes valuable service resources. The culprit? Ineffective work orders.
For machine manufacturers, after-sales service is a cornerstone of customer retention. Yet, poorly written work orders can create a hidden bottleneck, hindering your team's efficiency and responsiveness.
This is not imagination but a reality. The past three years have seen at least one unplanned downtime incident for 82% of companies. According to statistics, downtime costs an average of $5,600 per minute.
This guide offers a simple yet powerful framework for crafting clear, concise work orders that empower your service team and keep your customers' production lines humming.
A. The role of work orders in Business Operations
Why are work orders pivotal for business operations, especially in machine manufacturing? They are the backbone for organizing and prioritizing tasks, managing resources effectively, and maintaining transparency across all departments. With clear work orders, manufacturers can:
- Boost Efficiency: By clearly outlining what needs to be done, when, and by whom, work orders cut through confusion and enable a streamlined workflow.
- Enhance Accountability: Detailed records of work orders help track performance and ensure everyone knows their responsibilities, significantly enhancing team accountability.
- Improve Resource Management: Work orders allow managers to allocate resources smartly, ensuring that the right tools and personnel are available where they are most needed.
Digital work order management modernizes traditional processes by leveraging technology to automate and streamline tasks. According to the latest McKinsey report, a technology-based cost-reduction approach can reduce indirect costs by up to 20% within 1.5 years.
B. Essential elements of a Work Order
The elements of a work order can vary depending on the specific requirements and standards of the industry or organization, but typically, it includes the following key components:
- Work Order Number: A unique identifier for tracking and reference purposes.
- Date Issued: The date the work order was created and issued.
- Requestor Information: Details about the individual or department requesting the work, including contact information.
- Priority Level: Indicates the task's urgency, such as normal, urgent, or emergency.
- Job Description: A detailed description of the work to be performed, including the scope and specifications of the task.
- Location: The specific location where the work is to be carried out.
- Assigned To: Information about the person, team, or contractor responsible for completing the work.
- Estimated Start and End Dates: The expected timeframe for beginning and completing the work.
- Materials and Equipment: A list of all materials and equipment required to complete the job, including quantities.
- Safety Instructions: Any necessary safety instructions or precautions that need to be followed during the execution of the work.
- Approvals: Signatures or approvals from relevant authorities or managers to validate and authorize the work.
- Cost Estimates: Estimating labor, materials, and other resources.
- Instructions and Notes: Additional instructions, notes, or comments that can assist in completing the task.
- Status: Current status of the work order (e.g., open, in progress, completed, on hold).
- Attachments: Any related documents, diagrams, or photos that support the work order.
C. Step-by-step guide to writing a Work Order
Writing a work order involves clearly outlining the task or job to be completed, including all necessary details for execution. Here's a step-by-step guide:
Step 1: Collecting necessary information
It is crucial to gather all the relevant information before you start drafting your work order. This involves understanding the specific requirements of the task at hand, including any technical specifications, desired outcomes, and the project's ultimate goal.
Think of this step as laying the foundation for a successful project. It’s the part where you ask questions, gather documents, and make sure you have a clear picture of what needs to be done.
Step 2: Defining the scope of work
Now that you have your information, it's time to precisely define the scope of work. This includes a clear, concise statement of work (SOW) that outlines what the project will entail, what deliverables are expected, and what criteria define the project's success. By setting clear expectations from the start, you can avoid misunderstandings later on.
Step 3: Specifying task details
With the scope of work in place, the next step involves breaking down the project into specific tasks or milestones. This is where you detail the work, how it should be executed, and what materials or tools are required. Be detailed to provide clear directions and minimize questions or confusion during the execution phase.
Step 4: Assigning roles and responsibilities
Every project runs smoother when team members know exactly what they're responsible for. In this step, assign roles and responsibilities to the individuals or teams involved in the project. Ensure everyone understands their tasks, their level of authority, and whom they report to. This clarity promotes accountability and efficiency throughout the project.
Step 5: Setting deadlines and priorities
Deadlines and priorities keep the project on track. Establish realistic timelines for each task or milestone, considering any dependencies between tasks. Also, prioritize tasks based on their importance and urgency to ensure that critical milestones are met on time. Remember, setting achievable deadlines motivates the team and maintains project momentum.
Step 6: Reviewing for completeness
Before sending out your work order, take a moment to review it for completeness and clarity. Ensure all necessary information and details are included and the document is easily understood. This final review is your safety net, ensuring that nothing has been overlooked and all project parts are correctly outlined.
D. Common mistakes to avoid
When crafting work orders for machine manufacturers, precision and clarity are paramount. Avoiding common pitfalls can significantly enhance the efficiency and effectiveness of your operations. Here's how to sidestep frequent errors and create impeccable work orders.
1. Avoid vague descriptions of tasks
The Mistake: Many work orders fail because they do not specify what needs to be done. Vague task descriptions like "fix the machine" or "check the equipment" leave too much room for interpretation, leading to potential errors and inefficiencies.
The Solution: Specify precisely what needs to be done. For instance, "Replace the conveyor belt on the packaging machine with a new, high-tensile belt." Detailed descriptions ensure the executing team knows precisely what is expected, reducing back-and-forth communication.
2. Don't omit important details
The Mistake: Leaving out critical information such as location, necessary tools, and materials can delay task execution. Technicians might arrive at the wrong site without the required tools, wasting time and resources.
The Solution: Always include comprehensive details in your work orders. Specify the exact location of the machine needing maintenance, list all required tools and materials, and estimate the time needed for completion.
For example "Service required on CNC Router in Hall B, Section 5. Bring calipers and a set of Allen wrenches. Expect the task to take approximately 3 hours."
3. Prioritize your tasks
The Mistake: Failing to prioritize tasks can lead to critical maintenance issues being overlooked until they cause significant disruptions.
The Solution: Use a transparent labeling system in your work orders to indicate the priority of each task. For instance, label tasks as 'Urgent,' 'High,' 'Medium,' or 'Low.' This helps your team tackle the most critical issues and plan their workflow effectively.
4. Define clear roles and responsibilities
The Mistake: When work orders do not specify who is responsible for each task, it can lead to confusion and tasks falling through the cracks.
The Solution: Assign specific roles and responsibilities within the work order. Clearly state who is responsible for what, and ensure each team member understands their duties.
For example: "John Doe will replace the motor, and Jane Smith will perform the final testing."

E. Work Order templates
Creating effective Work Orders for machine manufacturers involves organizing all the necessary details that facilitate machinery manufacturing, maintenance, or repair. Below are two templates: one for manufacturing new machinery and another for maintenance/repair work.
Work Order template 1: Manufacturing new machinery Work Order
Work Order Number: [Unique Identifier]
Date: [MM/DD/YYYY]
Requested By: [Name/Department]
Priority: [Standard/Urgent]
Client information:
- Name: [Client's Name]
- Contact: [Phone, Email]
- Address: [Physical Address]
Machine specifications:
- Model Name/Number: [Specify Model]
- Type of Machine: [Type Description]
- Dimensions: [Length x Width x Height]
- Materials Required: [List of Materials]
- Blueprints/Documents Attached: [Yes/No]
Production details:
- Estimated Production Time: [Duration]
- Production Start Date: [MM/DD/YYYY]
- Completion Date: [MM/DD/YYYY]
- Production Supervisor: [Name]
Special instructions:
- [Any specific requirements or standards]
Quality Assurance:
- Inspections Required: [Yes/No]
- Quality Standards: [e.g., ISO 9001]
Estimated cost:
- Materials: [$ Amount]
- Labor: [$ Amount]
- Total Estimate: [$ Amount]
Approval:
- Manager: [Name/Signature]
- Date: [MM/DD/YYYY]
Work Order template 2: Machinery Maintenance/Repair Work Order
Work Order Number: [Unique Identifier]
Date: [MM/DD/YYYY]
Requested By: [Name/Department]
Machine Model/ID: [Model/ID]
Priority: [Standard/Urgent]
Machine Location:
- Site: [Location Address]
- Department/Area: [Department/Area Name]
Issue Description:
- Problem Reported: [Detailed Description of the Issue]
- Date Problem Identified: [MM/DD/YYYY]
Service Details:
- Type of Service: [Maintenance/Repair/Overhaul]
- Service Provider: [Company/Technician Name]
- Scheduled Service Date: [MM/DD/YYYY]
- Estimated Time of Completion: [Duration]
Parts Needed:
- [List of Parts and Part Numbers]
Safety Measures:
- Lockout/Tagout Required: [Yes/No]
- Safety Protocols: [List Protocols]
Estimated Cost:
- Parts: [$ Amount]
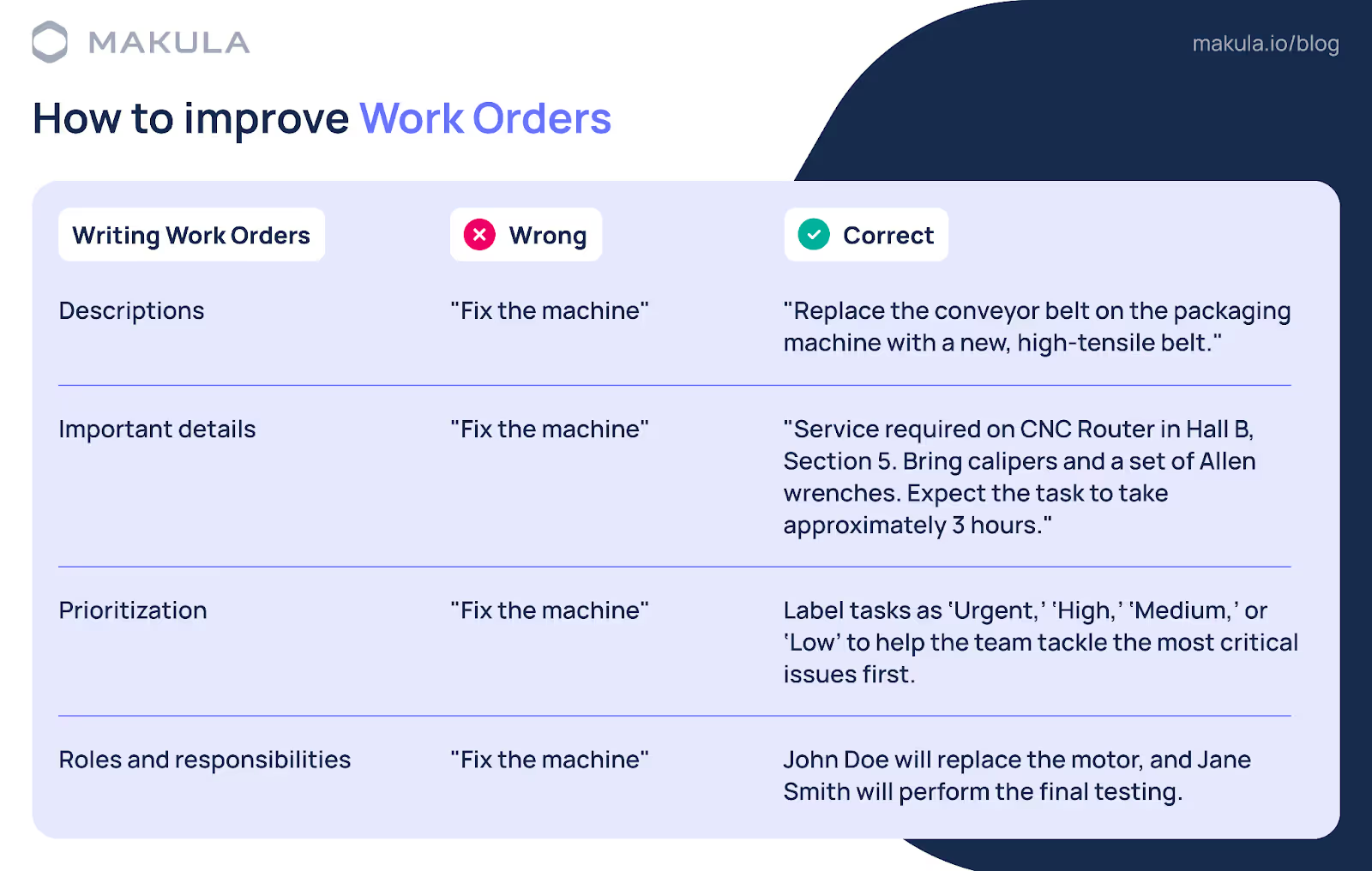
F. Transform your Work Orders with Makula
According to a recent study, 86% of manufacturers believe that smart factory solutions will transform the way products are made in five years. Makula's Work Order system empowers you to streamline operations and maintain transparency. Here is how:
Service Request
This is the most common type of work order, initiated by your customer to report a machine issue. It allows them to easily describe the problem, upload relevant photos or videos, and track the progress of the repair.
Spare Parts Order
When a customer identifies a need for spare parts, they can create a dedicated work order specifically for parts procurement. This ensures proper tracking and prioritization of parts fulfillment.
Customized Work Orders
Makula understands that your needs may extend beyond standard service requests. The system allows you to create custom work order types to cater to unique situations. Here are a few examples:
General Inquiry
This type can be used for customer inquiries that don't necessarily require a service technician visit. Examples include requesting machine manuals, seeking clarification on functionalities, or troubleshooting basic issues.
Mechanical Problem
This customized work order allows for capturing specific details related to mechanical malfunctions, potentially including symptom descriptions, error codes, or machine component identification.
Internal Work Orders
For tasks related to internal maintenance or upgrades on your machines, Makula allows you to create work orders that are not visible to your customers. These work orders can be linked to specific machines or assets within your facility, ensuring a comprehensive service history for each piece of equipment.