Best Practices for Managing Maintenance Across Multiple Facilities
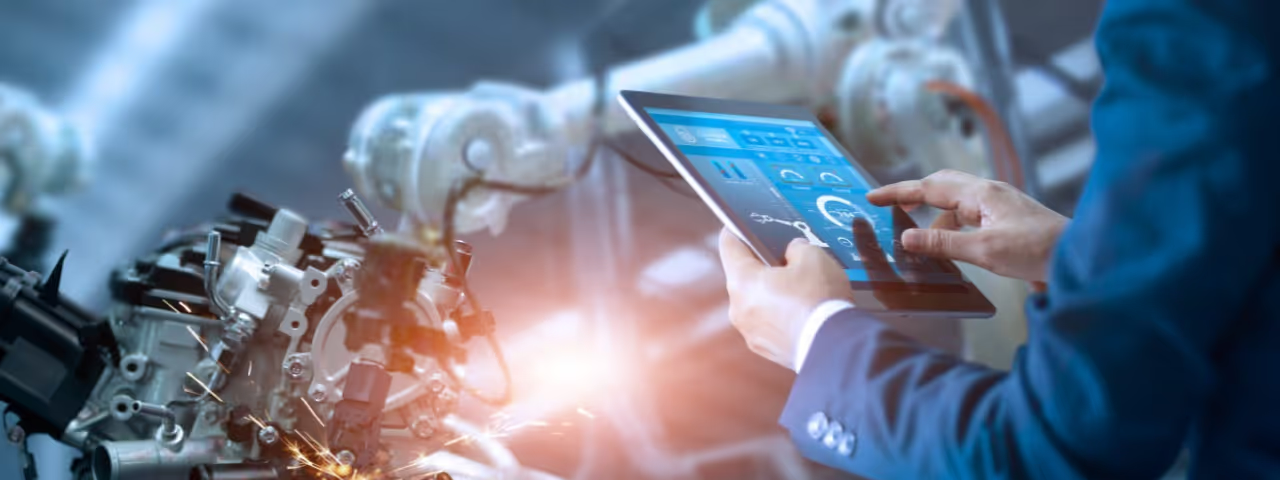
Best Practices for Managing Maintenance Across Multiple Facilities
Managing maintenance for a single facility can be complex, but when you're responsible for multiple sites, the challenges multiply. Keeping equipment running smoothly, optimizing resources, and ensuring consistency across locations requires a strategic approach and the right tools.
Here are some best practices to help you effectively manage maintenance across multiple facilities:
1. Standardize Processes:
Consistency is key. Implement standardized maintenance procedures, workflows, and documentation across all your facilities. This ensures everyone is following the same best practices, simplifies training, and makes it easier to track performance and identify areas for improvement.
2. Centralize Data:
Avoid data silos. Implement a centralized maintenance management system (CMMS) that allows you to track assets, manage work orders, and access data from all your facilities in one central location. This provides a comprehensive view of your operations, facilitates data analysis, and supports better decision-making.
3. Optimize Resource Allocation:
Effectively allocate resources based on the needs of each facility. Track technician availability, skillsets, and workload across locations to ensure you have the right people in the right place at the right time. Consider implementing a mobile workforce management system to optimize scheduling and routing.
4. Leverage Technology:
Embrace technology that streamlines communication, collaboration, and data sharing across multiple sites. Mobile CMMS apps, remote diagnostics tools, and online portals can empower technicians, improve efficiency, and reduce downtime.
5. Implement Predictive Maintenance:
Utilize data and analytics to predict potential equipment failures and perform preventive maintenance across all your facilities. This minimizes costly downtime, extends asset lifespan, and improves overall operational efficiency.
6. Foster Collaboration:
Encourage communication and collaboration between maintenance teams at different locations. Share best practices, conduct cross-site training, and facilitate knowledge sharing to improve performance and drive consistency.
7. Regular Audits and Inspections:
Conduct regular audits and inspections to ensure compliance with safety regulations, identify potential hazards, and assess the condition of equipment across all your facilities. This helps maintain a safe working environment and proactively address maintenance needs.
8. Performance Monitoring and Reporting:
Track key performance indicators (KPIs) across all your facilities, such as downtime, maintenance costs, and equipment reliability. Generate reports that provide insights into performance trends, identify areas for improvement, and support data-driven decision-making.
By implementing these best practices, you can effectively manage maintenance across multiple facilities, optimize resources, improve equipment reliability, and enhance overall operational efficiency.