What is Field Service Management?
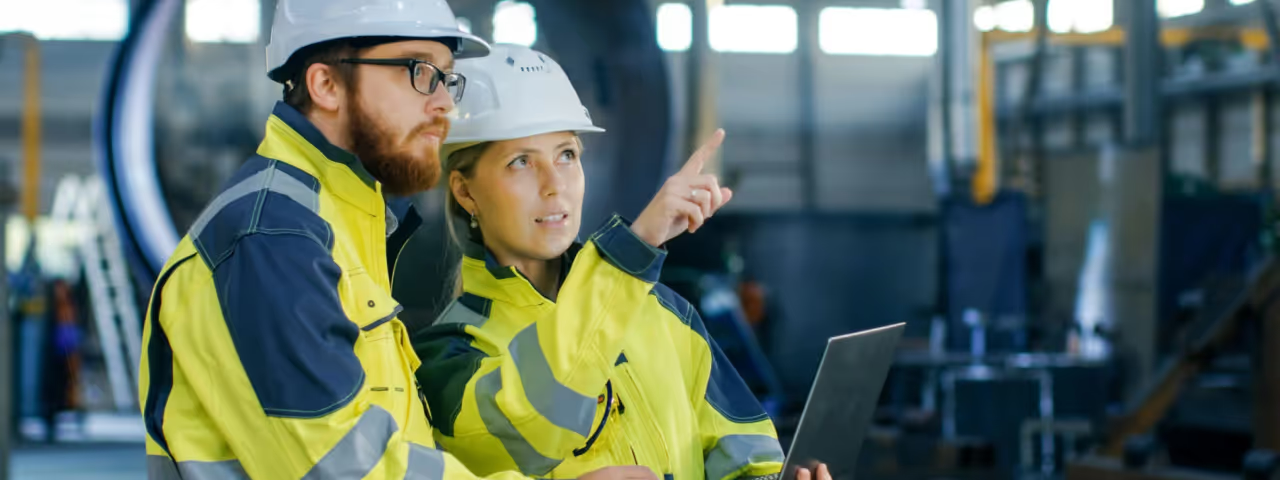
What is Field Service Management?
Field service management (FSM) is the art and science of getting your technicians where they need to be, when they need to be there, equipped with everything they need to do the job right. It's a comprehensive approach to managing every aspect of your field operations, from scheduling and dispatching to tracking inventory and ensuring customer satisfaction. FSM software provides the tools and technology to streamline these processes, making your field service team more efficient, productive, and customer-focused.
Think of it this way: instead of relying on spreadsheets, whiteboards, and phone calls to manage your field technicians, FSM software gives you a central hub to orchestrate everything. You can automate scheduling, optimize routes, track technician progress in real-time, and keep customers in the loop every step of the way.
Key Features of FSM Software
While the specific features of FSM software can vary, most platforms include these core functionalities:
- Work Order Management: Create, assign, and track work orders, ensuring technicians have all the necessary information, including customer details, equipment history, and job specifics.
- Scheduling and Dispatching: Optimize technician schedules and routes based on location, availability, and skillset, minimizing travel time and maximizing productivity.
- Inventory Management: Track parts and inventory levels, ensuring technicians have the right tools and materials on hand to complete the job efficiently.
- Mobile Access: Empower technicians with mobile devices to access work orders, customer information, knowledge bases, and communication tools in the field.
- Customer Communication: Keep customers informed with real-time updates, notifications, and two-way communication throughout the service process.
- Reporting and Analytics: Track key performance indicators (KPIs) such as first-time fix rates, response times, and customer satisfaction to identify areas for improvement and optimize service delivery.
Benefits of FSM for OEMs
Implementing a robust FSM solution can bring significant benefits to OEMs, including:
- Improved Efficiency: Streamline field service operations, reduce wasted time and resources, and optimize technician utilization.
- Increased Productivity: Empower technicians with the tools and information they need to work more efficiently, leading to faster job completion and increased productivity.
- Enhanced Customer Satisfaction: Deliver prompt, reliable service, keep customers informed, and proactively address their needs, leading to higher satisfaction and loyalty.
- Reduced Costs: Minimize downtime, optimize inventory, improve first-time fix rates, and reduce travel expenses, ultimately lowering operational costs.
- Improved First-Time Fix Rates: Provide technicians with instant access to equipment history, knowledge bases, and remote support, enabling them to diagnose and resolve problems correctly on the first visit.
- Better Data-Driven Decisions: Leverage data and analytics to gain insights into field service performance, identify trends, and make informed decisions to optimize operations.
The Evolution of FSM: From Reactive to Proactive
Traditionally, field service was often reactive, responding to breakdowns and emergencies as they arose. However, with the advent of FSM software and technologies like IoT and AI, OEMs can shift towards a more proactive approach. This involves:
- Predictive Maintenance: Using data and analytics to predict equipment failures before they occur, allowing for proactive maintenance and preventing costly downtime.
- Condition-Based Monitoring: Monitoring equipment health in real-time using sensors and data analysis, enabling proactive maintenance based on actual equipment condition rather than fixed schedules.
- Remote Diagnostics: Diagnosing and resolving equipment issues remotely, reducing the need for on-site visits and minimizing downtime.
Choosing the Right FSM Solution
When selecting an FSM solution, OEMs should consider factors such as:
- Industry-Specific Needs: Choose a solution that caters to the specific requirements of your industry and equipment.
- Scalability: Ensure the solution can grow with your business and adapt to changing needs.
- Integration Capabilities: Select a solution that integrates seamlessly with your existing systems, such as CRM and ERP.
- Mobile Functionality: Prioritize solutions with robust mobile capabilities to empower your field technicians.
- Reporting and Analytics: Choose a solution that provides comprehensive reporting and analytics to track performance and identify areas for improvement.
By implementing a comprehensive FSM solution, OEMs can transform their field service operations, improve customer satisfaction, and drive business growth.